3D Printing Design for Beginners: An In-Depth Guide
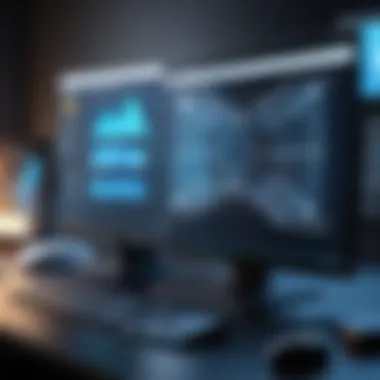
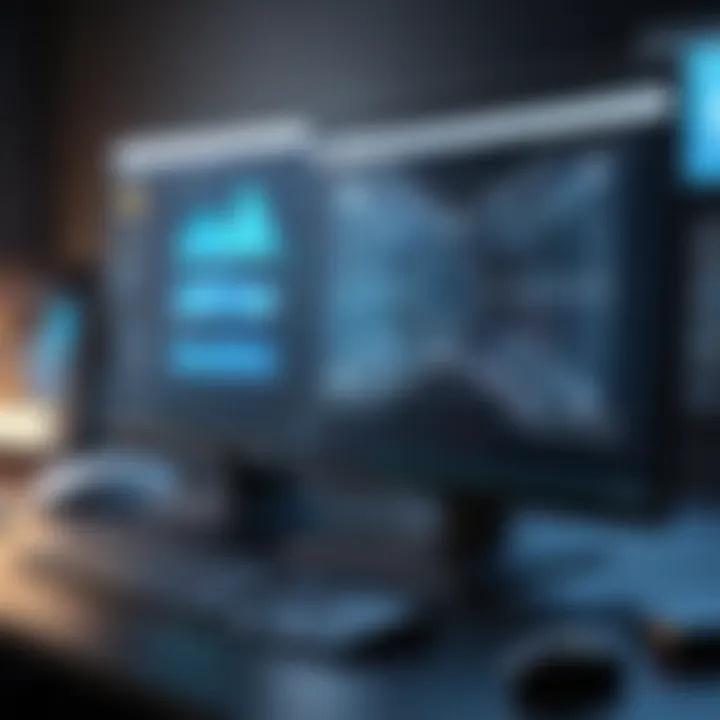
Intro
Stepping into the world of 3D printing can feel like a leap into the future, yet it’s more accessible than you might think. Whether you’re a hobbyist, a tech enthusiast, or someone looking to explore new possibilities in design, this guide will unravel the essentials of 3D printing. By understanding the foundation of design principles, tools, and techniques, you will be equipped to kickstart your journey into additive manufacturing.
3D printing isn't just a fad; it’s transforming how we approach design, prototyping, and production across various industries. As you navigate through this guide, we’ll highlight significant aspects of the 3D printing process. From design software essentials to understanding materials, every detail matters. This introduction aims to set the stage for a deeper dive into the mechanics of designing for 3D printing.
With an array of software available, knowing which one fits your needs is crucial. Additionally, selecting the right material can make or break your project. Let’s go beyond the basics and explore the intricacies of this innovative field together.
Preface to 3D Printing
3D printing has blossomed from a niche hobby into a significant player in manufacturing, design, and even art. As we venture through this article, understanding the fundamentals of 3D printing is crucial for anyone eager to tap into this technological marvel. It’s a game changer, providing versatility and creative freedom like never before. Not only can you design and produce complex shapes, but the potential for innovation is endless.
Definition and Overview of 3D Printing
At its core, 3D printing—often referred to as additive manufacturing—is the process of creating three-dimensional objects from a digital file. This is done by laying down successive layers of material until the entire object is created. You can liken it to building a cake: layer upon layer adds not just flavor, but structure as well.
The beauty of this technology lies in its ability to transform digital designs into tangible items. From toys to prototypes, and even functional machinery parts, 3D printing covers a vast range of applications. Each material and method can yield vastly different results, making it both a science and an art.
Historical Context
Tracing back its roots, 3D printing has a fascinating history. The first widely recognized method of 3D printing was stereolithography, developed by Chuck Hull in the early 1980s. Initially used mostly for rapid prototyping, it paved the way for a slew of methods that followed. Over the years, the technology has seen improvements, leading to a drop in costs and a rise in accessibility. By the 2010s, with the advent of desktop 3D printers like those from MakerBot and Ultimaker, hobbyists began to experiment with this technology, bringing it into homes and DIY workshops across the globe.
"3D printing is not just a technology; it represents a revolution in how we think about manufacturing and design".
— Anonymous
Current Applications
Today, the applications of 3D printing are as diverse as they are impressive. Some notable uses include:
- Prototyping: Engineers and designers create functional models quickly and affordably.
- Medical: From custom prosthetics to bioprinting tissues, the healthcare sector is leveraging 3D printing for personalized treatment.
- Aerospace: Components that can withstand extreme conditions are being fabricated with precision.
- Consumer Products: Everything from home decor to gadgets can be produced, offering personalization at scale.
The implications of 3D printing stretch across industries, altering approaches to traditional manufacturing, reducing waste, and encouraging sustainable practices. The technology is evolving fast, and keeping pace with its advancements is key for anyone serious about stepping into this domain.
Understanding the Basics of 3D Design
Understanding the basics of 3D design is a crucial stepping stone, especially for beginners in the world of 3D printing. Grasping the core principles here sets a strong foundation for tackling complex creations later on. At its heart, 3D design marries art and technology, demanding both creativity and analytical skills. With this knowledge, aspiring designers not only gain technical competency but also develop the ability to visualize their ideas in three dimensions.
Before diving into the various tools and technologies available, it is pivotal to distinguish the difference between 2D and 3D models, as these form the core of what one creates in any design software.
2D vs. 3D Models
2D and 3D models occupy distinct realms in design, and understanding their divergence is fundamental. Think of a 2D model as a drawing—flat and limited to width and height. Can you imagine how that looks? Like tracing a shadow without depth. On the other hand, a 3D model adds dimension—depth, height, and width. This transformation allows for a lifelike representation, adding a layer of realism to any project.
In practical terms, creating a 3D model allows designers to manipulate objects in a manner akin to sculpting in clay. They can rotate, scale, and view the model from all angles, leading to better planning and more effective execution of ideas. For instance, an architect designing a building needs a 3D model to grasp how the structure will fit into its surroundings, while a game designer may need dynamic characters that can be viewed and animated in three-dimensional space.
- Visualizing Projects: With 3D models, one gets a clearer sense of proportions and scales, which is often lost in 2D representations.
- Interactivity: The 3D model allows for extensive interaction, pushing the boundaries of creativity.
- Realistic Rendering: Creating photorealistic images is far easier with a solid 3D foundation.
Common File Formats
When starting out in 3D design, knowing the file formats is equally important. Various file extensions serve specific purposes, depending on the software being used and the end goal of the design. Here’s a brief rundown of some commonly used formats:
- STL (Stereolithography): The go-to for 3D printing, this format is widely recognized for its simplicity in representing a 3D model's surface geometry.
- OBJ (Wavefront): This format supports color and texture, useful for more detailed designs, especially in game and film industries.
- FBX (Filmbox): A favored choice for animation, FBX facilitates the transfer of 3D assets and animations between software.
- 3DS (3D Studio): Initially emerging from Autodesk’s 3D Studio, it remains popular for its compatibility with many modeling tools.
- PLY (Polygon File Format): This format is used frequently in 3D scanning as it can represent vertex color and additional attributes.
In a nutshell, when you’re ready to export or share your designs, knowing the correct formats empowers you to communicate your visual creativity effectively.
"A smooth sea never made a skilled sailor." Just as sailing demands practice and understanding, so does mastering 3D design. Each model created is a part of a larger journey in additive manufacturing.
Essential Software for 3D Design
In the realm of 3D printing, the software you choose can be the linchpin between a mediocre print and a masterpiece. Software tailored for 3D design not only boosts productivity but also enhances creativity. Knowing which software fits your needs is vital. Think of software as your digital sculpting tool; it shapes your ideas, turning imagination into reality. There are various options available, each with its unique features, benefits, and considerations.
Popular Design Software Options
When it comes to popular design software, the landscape is vast, but a few heavyweights stand out due to their features, usability, and community support.
- TinkerCAD: This browser-based application is perfect for beginners. Its intuitive interface allows users to create 3D designs with simplicity and ease. The drag-and-drop feature is user-friendly, making it ideal for those just starting out.
- Fusion 360: A favorite among professionals and hobbyists alike, Fusion 360 offers a comprehensive suite for CAD (Computer-Aided Design), CAM (Computer-Aided Manufacturing), and CAE (Computer-Aided Engineering). It provides powerful tools for both precision designing and rendering.
- Blender: Known for its versatility, Blender is an open-source platform that covers everything from design to animation. It is perfect for those who want to explore more advanced 3D modeling techniques. Its steep learning curve is often outweighed by its capabilities.
"The right software can transform a great idea into something exceptional."
Choosing the right software is akin to selecting the right brush for painting; it can define the outcome of your work.
Open Source Tools
In the world of 3D design, open-source tools are increasingly popular, especially among those who appreciate community-driven development and customization. They often allow for greater flexibility without the financial burden of commercial software. Consider these:
- FreeCAD: This parametric 3D modeler focuses on mechanical engineering and product design. Its functionalities allow users to create complex projects by modifying parameters easily, making it perfect for those who need precision.
- OpenSCAD: Unlike more traditional 3D modeling applications, OpenSCAD focuses on the programmer's perspective. You essentially create your model using code, which gives you unmatched control and repeatability in your designs.
- LibreCAD: While primarily a 2D CAD application, it’s robust enough to use for 3D printing preparation. It supports various file formats that can be handy during the design process.
Software for Specific Needs
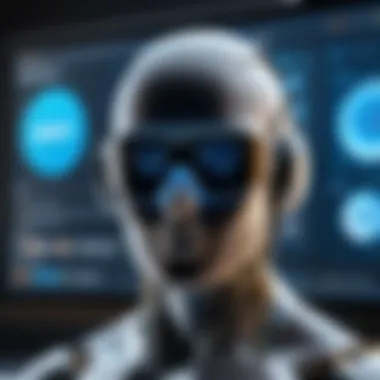
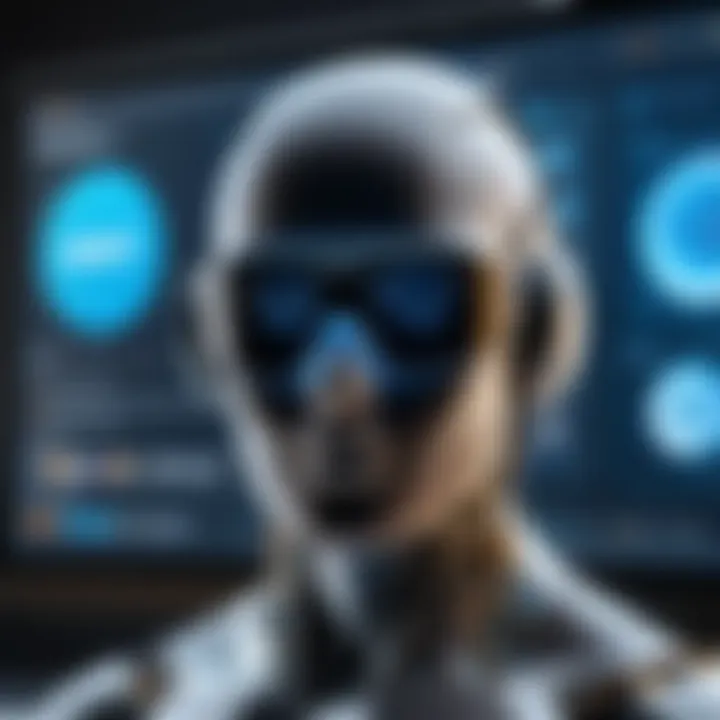
Different projects require different approaches, and specific software is designed to cater to niche needs:
- SketchUp: Widely used in architecture and interior design, this software’s simplicity and vast library of pre-made models set it apart. It’s perfect for visualizing spaces before they’re created.
- ZBrush: For those leaning towards character modeling or organic shapes, ZBrush is essential. It offers advanced texturing and details that elevate your models. Though on the pricier side, its capabilities are often considered worth the investment.
- Sculptris: If you're new to sculpting and want to dip your toes into organic modeling, Sculptris offers a more streamlined interface than ZBrush. It’s user-friendly and lets you experiment without overwhelming you.
3D Printing Technologies
Understanding the various 3D printing technologies is crucial for anyone looking to dip their toes in the waters of additive manufacturing. Each technology offers unique strengths, weaknesses, and applications. Familiarity with these methods can enhance the overall success of your printing projects. As you navigate through the different technologies, you’ll find that they can dictate not just the material used, but also the degree of precision and the final finish of your printed object. This section unpacks three prevalent 3D printing technologies: Fused Deposition Modeling (FDM), Stereolithography (SLA), and Selective Laser Sintering (SLS). Each technology holds specific attributes that can serve your creative endeavours based on your project’s needs.
Fused Deposition Modeling (FDM)
Fused Deposition Modeling is probably the most popular 3D printing technology among beginners. The process involves feeding a thermoplastic filament into a heated nozzle, which melts it and extrudes it layer by layer onto a print bed. This straightforward concept makes FDM accessible and relatively easy to grasp, particularly for newbies navigating the perplexing field of 3D printing.
One of the undeniable benefits of FDM is its cost-effectiveness. Affordable printers can produce reliable results without burning a hole in your pocket, making it an attractive entry point. Moreover, the variety of materials available—such as PLA, ABS, and PETG—enables users to select a filament that meets their specific project requirements. FDM isn’t just about saving coin; it can also create durable parts suitable for functional prototypes and end-use applications.
However, there are considerations to keep in mind. The layer-by-layer process can lead to visible layer lines, affecting aesthetics if not properly post-processed. Also, while the method is generally reliable, you might encounter issues like warping or under-extrusion if your printer isn’t calibrated correctly. Despite these quirks, FDM remains a solid choice for beginners.
Stereolithography (SLA)
Stereolithography is another technology worth your attention, especially if surface finish and detail are high on your priority list. Instead of extruding material, SLA uses a laser to cure liquid resin, solidifying it layer by layer. This process generally allows for greater resolution and smoother finishes compared to FDM. For those passionate about creating intricate designs, SLA might be where you want to set your sights.
The variety of resins available gives designers room to explore diverse characteristics, from flexible resins to those achieving high-temperature resistance. Print times can be faster for small, detailed models, since the method utilizes light rather than material mass to form objects.
Yet, SLA comes with its own set of challenges. The resins can be more costly, and post-processing usually requires washing and curing steps, which adds time to your workflow. Additionally, handling uncured resin requires safety precautions, as it can be toxic. If you are looking for high-quality prints where aesthetics matter, SLA is certainly a contender, but be prepared for the intricacies that come with it.
Selective Laser Sintering (SLS)
Moving to a different realm, Selective Laser Sintering presents an option for those who are willing to invest a bit more in capability and quality. In this process, powdered material—commonly nylon—is layered onto a build platform where a laser fuses the powder together to form solid structures. This technology excels in producing parts that are both strong and complex, making it a favourite for functional prototypes and end-use components in various industries such as automotive and aerospace.
A primary advantage of SLS lies in its ability to create intricate geometries without requiring support structures, thanks to the surrounding powder providing stability during the printing process. Moreover, the durability of SLS parts allows them to withstand significant stress, making them suitable for rigorous applications.
On the flip side, SLS printers tend to be on the expensive side, making them less accessible for a hobbyist or someone new to the craft. Additionally, the post-printing process involves sifting through powdered materials, which can create a mess and requires careful handling. For those willing to navigate these hurdles, SLS opens up a world of capabilities for professional-grade applications.
The choice of 3D printing technology can profoundly impact your project’s quality, cost, and timeline. Understanding these options helps in making an informed decision tailored to your needs.
Material Selection for 3D Printing
Selecting the right material is crucial in 3D printing. Each material brings unique properties, affecting the outcome based on the project’s needs. Beginners often underestimate this aspect, thinking any material will serve the purpose. However, using the right type can mean the difference between a successful print and a catastrophic failure. Not only does the choice impact durability and function, but it also plays a role in the aesthetics of the final product.
When considering materials, one must take into account factors such as strength, flexibility, thermal resistance, ease of use, and even cost. Ultimately, the goal is to align the performance characteristics of the material with the objectives of the printing project. Let’s dive deeper into the specific types of materials and how to choose wisely.
Types of 3D Printing Materials
The landscape of 3D printing is vast, filled with various materials suitable for different applications. Here is a closer look at some prominent options:
- PLA (Polylactic Acid): A biodegradable plastic, ideal for beginners due to its ease of use and good print quality. It’s friendly for the environment and emits a sweet smell while printing.
- ABS (Acrylonitrile Butadiene Styrene): Known for its toughness and impact resistance, ABS is often used for functional parts. However, it requires higher temperatures and proper ventilation due to fumes released during printing.
- PETG (Polyethylene Terephthalate Glycol): A hybrid of PET and glycol, it offers flexibility and strength. Suitable for containers, it’s also resistant to moisture.
- TPU (Thermoplastic Polyurethane): A flexible material, ideal for creating parts that need to bend, like phone cases.
- Nylon: Known for its strength and durability, nylon is great for functional prototypes. However, it can be challenging to print due to warping issues.
Consideration of these materials not only informs about the physical attributes but also about compatibility with the various 3D printing technologies discussed previously, such as FDM and SLA.
Choosing the Right Material for Your Project
In selecting the most appropriate material for 3D printing, one must analyze the specific requirements of the project. Here are a few considerations to guide this decision:
- Desired Strength: Assess how much durability is needed. For instance, if the item is a tool or a mechanically loaded part, take strength and toughness into account.
- Environmental Conditions: Determine if the printed object will be exposed to heat, moisture, or chemicals. For applications exposed to harsh environments, materials like ABS or PETG are preferable.
- Functionality vs. Aesthetics: Some projects highly value aesthetics, like clear models or detailed designs, which may lean toward materials like PLA. Others prioritize function, necessitating stronger options.
- Ease of Printing: Beginners should start with user-friendly materials like PLA to minimize issues during the printing process. As skills improve, experimenting with advanced materials can enhance capabilities and final outputs.
By carefully considering these aspects, beginners can make informed decisions, ultimately enhancing the success of their 3D printing projects. Making the right choice in material will set the foundation for effective printing, ensuring the prints are not only functional but also meet the aims envisioned at the outset of the design process.
"Material selection is not merely a technical decision; it’s an integral part of the creative process, influencing every step of your project's journey."
Design Principles for 3D Printing
Understanding the design principles for 3D printing is like having the compass that guides you through a dense forest. It’s essential to comprehend the unique aspects of additive manufacturing right from the get-go. Design principles impact not only the aesthetics of the final product but also its functionality, strength, and manufacturability. Thus, knowing these principles equips beginners to avoid common pitfalls while maximizing creativity and efficiency.
Understanding Design for Additive Manufacturing (DfAM)
Design for Additive Manufacturing, or DfAM, is about reevaluating traditional design approaches to leverage the capabilities of 3D printing technology effectively. In essence, it's not just about creating models; it’s about creating models that are tailored for production using 3D printers.
- Iterative Design: The beauty of 3D printing lies in its flexibility. Mistakes in design can be corrected with relative ease in comparison to conventional manufacturing. This encourages multiple iterations and refinements—essentially a trial-and-error approach.
- Complexity is Free: Unlike traditional manufacturing methods that may raise costs due to complexity, with 3D printing, intricate geometries and internal features become more accessible, allowing for innovative designs.
- Material Optimization: DfAM encourages users to rethink the materials utilized. For instance, using lightweight materials in specific applications not only enhances performance but also conserves resources.
- Hybrid Designs: Combining multiple functions into a single part can drastically simplify the assembly process. This stands in stark contrast to classic techniques which often involve joining many components together.
In short, understanding DfAM is not only about avoiding missteps—it's also a robust means to explore the new frontier of creativity in design.
Designing for Strength and Durability
When it comes to functional components, strength and durability are non-negotiable. For a novice, one could imagine designing a bridge that collapses under weight—definitely an undesirable outcome! Here’s how to ensure designs withstand the test of time:
- Material Properties: Different materials behave uniquely under stress. For instance, nylon is known for its strength and flexibility, while PLA, although easy to print, can be brittle. Assessing the material's properties aligned with the intended application is vital.
- Layer Orientation: The way layers are oriented affects strength. Parts printed with layers aligned with load lines generally exhibit superior strength. Understanding this can directly affect the lifespan of the printed model.
- Infill Patterns: The infill percentage and pattern, whether it’s a grid, hexagonal, or concentric design, significantly influence strength without overly increasing the weight.
- Design Redundancies: Incorporating features that allow for additional support—like ribs or gussets—can bolster a design’s resilience without dramatically altering its appearance.
"Good design is not just about how a thing looks; it’s about how it works."
— Steve Jobs
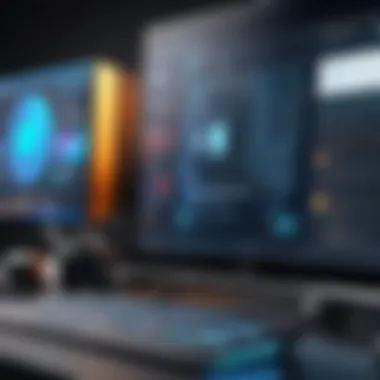
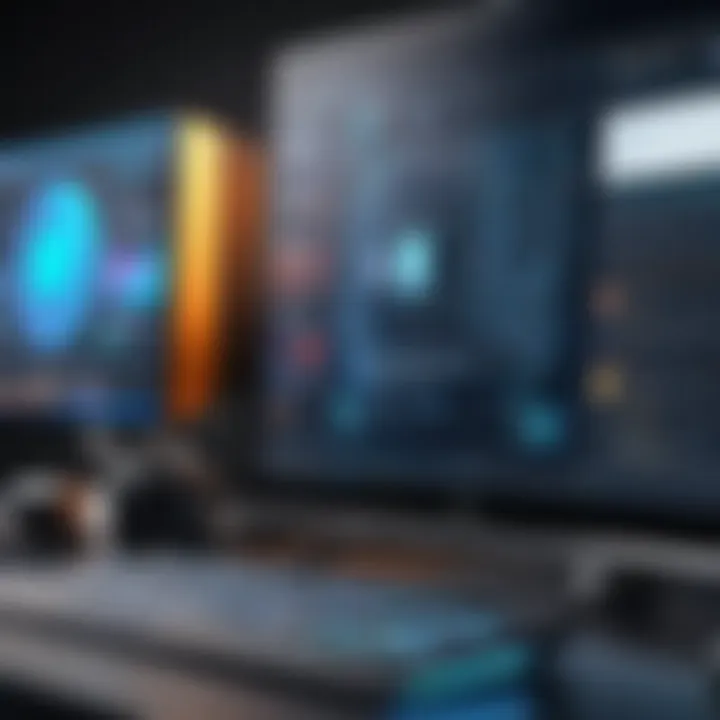
By focusing on these elements, you ensure that your creations are not only beautiful but reliable as well.
Exploring Aesthetics in Design
Turning attention to aesthetics, it's crucial to remember that design is as much about the eye as it is about the engineering. A visually appealing object can attract interest, inspire conversations, and bestow a sense of value. Here are points to ponder:
- Proportion and Scale: Getting the size right is often overlooked. A well-proportioned object catches the eye. Consider using design software tools that allow you to manipulate size and scale easily.
- Textures and Finishes: Experimenting with surface textures can significantly enhance visual appeal. Techniques like sanding, polishing, or adding a texture finish make the object more attractive.
- Color Psychology: The emotional responses triggered by colors shouldn’t be underestimated. Selecting hues that resonate with audiences might just be the cherry on top.
- Functionality Dictates Form: Sometimes the best “wow” factor comes from unexpected functionalities—like a lamp designed with a geometric structure that doubles as a conversation piece. Think outside the box!
Getting Started with 3D Printing
Diving into the world of 3D printing isn't just about the technology; it's about embracing a mindset of creation and innovation. For beginners, knowing how to get started lays the foundation for successful projects. Grasping the essentials of 3D printing ensures that newcomers enjoy the experience and avoid common pitfalls. Whether you’re aiming to create prototypes, hobbyist projects, or functional items, understanding the initial steps is crucial.
Getting your hands dirty with a 3D printer can be quite an adventure. However, setting things up right the first time can save you headaches later on. A well-prepared starting point means less frustration as you move along your learning curve. This section will detail the setup process, the components you need, and the fundamental steps of printing.
Setting Up Your 3D Printer
Setting up your 3D printer may seem daunting, especially if you’re not technically inclined. But, fret not. It’s more straightforward than it appears. Each printer has specific instructions, but let’s break down the common elements:
- Choose the Right Location: Find a stable, flat surface with ample space. Some printers can be quite large, and you don’t want to cram them into a corner.
- Unpack and Assemble: Carefully remove your printer from the box, following the manual for assembly.
- Level the Build Plate: This step is critical. If your build plate isn’t level, your prints can come out poorly. Most printers have a built-in leveling feature. Follow any instructions provided.
- Load Filament: Depending on whether your printer uses FDM, SLA, or another method, loading filament will differ. For FDM printers, simply insert the filament into the designated spot.
- Connect to Power and Software: Connect the printer to a power source and load any necessary software on your computer. This often involves installing a slicer program that converts 3D models into instructions for your printer.
- Check Calibration: Run a test print or use a calibration model available through your software. This practice helps ensure everything is functioning smoothly.
A well-set-up 3D printer can make all the difference in the quality of your work. Take a moment to read through the printer's manual—this isn’t just busywork; it’s a roadmap for success.
"A journey of a thousand miles begins with a single step."
– Lao Tzu
Step-by-Step Printing Process
Now that your 3D printer is set up nicely, it’s time to get into the nitty-gritty of printing. The process can be broken down into clear steps to follow:
- Select a 3D Model: Use websites like Thingiverse or MyMiniFactory to find models that pique your interest. You can also create your own using software discussed in earlier sections.
- Import the Model to Your Slicer Software: Open your chosen slicer, and import the 3D model file. Different slicers may have different interface layouts, but they typically share common features.
- Configure Printing Settings: Adjust settings such as layer height, infill density, and print speed. Beginners may benefit from sticking with default settings until they gain confidence.
- Slice the Model: This action converts the model into G-code, the language your printer understands. Review the estimated print time and filament materials usage—this can help in planning.
- Transfer the G-code to Your Printer: Depending on the model, you might use an SD card, USB, or direct connection to send the file over to your printer.
- Initiate the Print: Press start, and watch your design come to life! Keep an eye on the initial layers; they are crucial for adhesion.
- Post-Print Inspection: Once printing is complete, carefully remove the object from the build plate, check for quality, and assess any additional post-processing needed.
Remember, every print is a learning experience. Don’t get discouraged by setbacks; they’re part and parcel of working with this technology. Embrace the process, and with time you'll develop not only skill but also confidence in your 3D printing adventures.
Troubleshooting Common Issues
In the journey of 3D printing, no matter how skilled you become, you will encounter hiccups along the way. Troubleshooting common issues is not just an important skill to develop; it’s crucial for maintaining the quality of your prints and ensuring a smooth workflow. With this knowledge, you can quickly identify problems and apply solutions, which reduces downtime and enhances your overall experience.
Being proactive about troubleshooting means you aren’t just reacting to issues as they arise. Rather, you’re equipped to preemptively address problems that may emerge, saving you time and materials. Whether it’s a misalignment of the print head or a stubborn filament jam, knowing how to tackle these hurdles allows you to keep your printer performing at its best. Let’s delve deeper into identifying typical printing errors and the best ways to resolve them.
Identifying Common Printing Errors
When diving into the realm of 3D printing, understanding common errors is key to minimizing frustration. Errors can vary from minor blemishes to complete print failures. Here’s a closer look at some frequent issues:
- Layer Separation: This often happens when the printed layers aren’t adhering properly due to inadequate temperature or too much cooling.
- Under-extrusion: You may notice thin or missing sections in your print. This could be caused by a clogged nozzle or insufficient filament supply.
- Stringing: This pesky occurrence can manifest as unwanted strands of plastic that appear between different sections of a print. It’s usually a result of excessive melting in the nozzle during travel moves.
- Warping: If the corners of your print start to lift away from the bed, warping has occurred, often due to temperature differences between the bed and the surrounding environment.
- Z-Axis Issues: Misalignment in the Z-axis can lead to inconsistent layer height or, worse, adhesion issues between layers.
If you know these common problems, you not only enhance your troubleshooting prowess but also set realistic expectations for your prints.
Solutions and Best Practices
Now that you can identify common printing errors, it’s time to talk solutions. Here’s a list of targeted approaches to each issue listed above, ensuring you’re well-prepared to tackle obstacles as they arise:
- Layer Separation: Increase the temperature of both the nozzle and heated bed to improve layer adhesion. Also, assess your print speed.
- Under-extrusion: Ensure there are no clogs in the nozzle. If you notice consistent under-extrusion, it may be worth calibrating your extruder steps per millimeter.
- Stringing: Tweak the retraction settings in your slicing software. A higher retraction distance and speed can significantly decrease stringing.
- Warping: Utilize a heated bed and ensure your print is securely adhered to it. Trying out glue stick or painter’s tape can help with adhesion.
- Z-Axis Issues: Check the bed leveling and recalibrate it regularly, as even a slight misalignment can cause major displacement during printing.
"The art of troubleshooting lies in understanding that every error has a solution. Learn the signs, adapt, and improve."
By following these suggestions, you can increase your odds of success and produce clean and reliable prints. Remember, practice makes perfect, so don’t shy away from experimenting to find what works best for your setup.
Post-Processing Techniques
In the realm of 3D printing, post-processing techniques play an integral role. These methods can transform a printed object from a simple, rough prototype into a polished piece ready for display or use. While 3D printing can generate parts with complex geometries and features, the finished quality often requires additional steps to meet aesthetic or functional requirements.
The importance of post-processing cannot be overstated. Engaging in these techniques can improve the surface finish, enhance durability, and even alter the physical properties of materials used in a print. From simple cleaning methods to more advanced finishing techniques, this segment aims to cover the nuances that elevate a printed object from good to great.
Cleaning and Finishing Techniques
Once the print has been completed, the first task is often cleaning. Support material, glue, or leftover powder from the printing process can mar the final appearance of your design. Common cleaning techniques include:
- Warm Water Soaking: Soaking parts in warm water can dissolve PVA or HIPS supports.
- Mechanical Removal: For tougher supports or residue, using tools like tweezers or small knives can help.
- Isopropyl Alcohol (IPA): This solvent is popular for cleaning SLA prints, effectively washing away uncured resin.
After cleaning, finishing can dramatically enhance the look and feel. Techniques like sanding, polishing, or using specialized chemical baths can bring out the best in your design. A light sanding can soften rough edges, while a polishing step adds shine, resembling a factory-finished product. Furthermore, those inclined towards intricate designs may even explore resin casting or vapor smoothing for that professional touch.
Painting and Coating Options
Applying paint or coatings can breathe life into a dull print, adding color and character. There are numerous approaches one can take depending on the desired outcome. Consider these options:
- Acrylic Paints: Water-soluble and easy to work with; acrylics are a favorite among DIY enthusiasts for their quick drying times and vibrant colors.
- Spray Paints: For larger or detail-oriented projects, spray paints can lay down a uniform color coat swiftly. They often integrate well with plastics but require a well-ventilated area for safety.
- Specialized Coatings: Some coatings are specifically designed for 3D prints, offering enhanced durability or even UV resistance.
- Clear Coat Finishes: A final layer of varnish or clear coat can protect the paint job and add a glossy or matte finish.
The right approach to painting or coating is highly contextual and may depend on various factors including the type of material used and the intended use of the printed object.
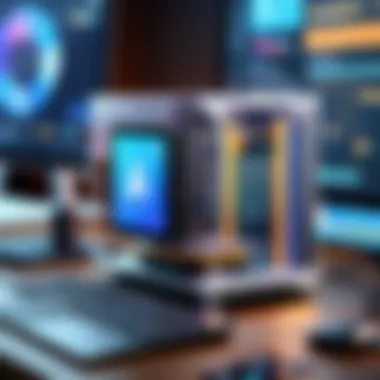
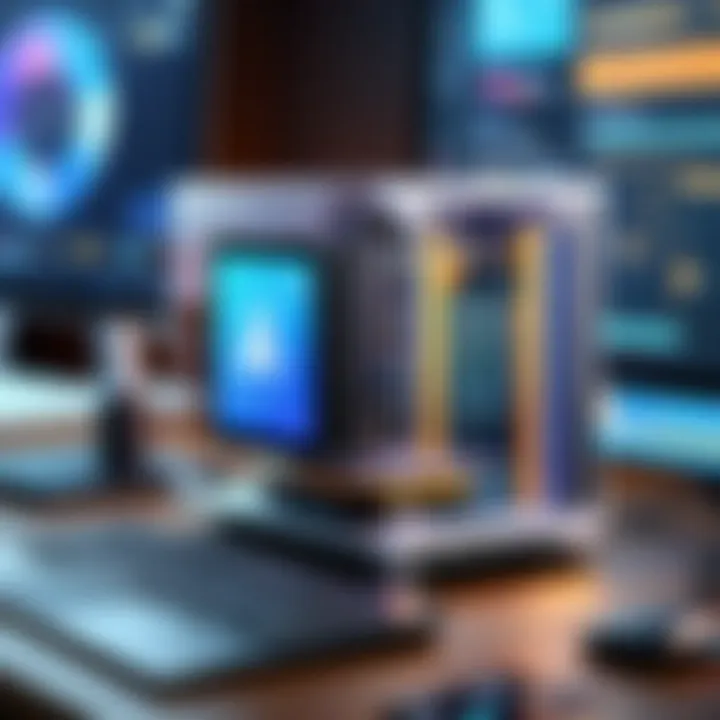
"Post-processing techniques not only enhance the beauty of 3D prints but also ensure their longevity and functionality, making every print a worthwhile venture."
Tackling post-processing effectively can truly define a project. A clean, well-finished, and beautifully painted piece can speak volumes about the creator’s attention to detail and dedication to craftsmanship. From simple cleanups to intricate painting methods, mastering post-processing will empower you in your 3D printing journey.
Exploring Advanced 3D Design Concepts
In the realm of 3D printing, diving into advanced design concepts is akin to stepping off the well-trodden path and forging into uncharted territory. These concepts not only enhance the creativity and efficiency of the designs but also unlock possibilities that fledgling designers might not have thought possible. Complex tolerances, material usage efficiency, and innovative aesthetics can be achieved through methods such as parametric design, topology optimization, and generative design. Understanding these advanced techniques is crucial for anyone looking to elevate their design skills from basic shapes to intricate masterpieces.
Parametric Design
Parametric design flips the usual process of 3D modeling on its head. Rather than pulling shapes and dimensions from thin air, it utilizes parameters—variables that can dictate the size, shape, and proportions of your model. This approach allows designers to make adjustments in real-time, ensuring that any changes propagate throughout the entire project. Imagine designing a chair where you simply alter one dimension, like seat height; this change automatically modifies the whole design to maintain proportions.
The benefits are multiple:
- Flexibility: Adapting designs based on user preferences or manufacturing requirements becomes far simpler.
- Efficiency: Instead of starting from scratch with each modification, the structure remains intact, cutting down design time.
- Precision: Parametric models often lead to higher levels of accuracy because rules govern the relationships between elements, minimizing human error.
Topology Optimization
Topology optimization is a game-changer in creating lightweight yet strong designs. It is a computational technique that adjusts the material layout within a given design space, subject to certain constraints, to maximize performance. Think of it as baking a cake; instead of just pouring in all the ingredients, you sift through to create a lighter, tastier final product.
For designers, the benefits are clear:
- Weight Reduction: By eliminating unnecessary materials, you can decrease the weight of your models, which is particularly crucial for industries such as aerospace or automotive.
- Material Efficiency: This practice not only saves money but also is more environmentally friendly, as it reduces waste.
- Enhanced Performance: Models that undergo this process often perform better in their intended applications, as the design focuses on functionality rather than mere form.
"Topology optimization is like sculpting marble—removing the excess to reveal the essence of your design."
Generative Design
Generative design takes things a step further by utilizing algorithms to generate numerous design alternatives based on specific input parameters. This means that the designer sets the goals—like material limits, weight restrictions, or performance requirements—and let the software suggests various configurations. It’s like giving a recipe to a chef and watching them create an entire menu based on your cabbage and chicken.
The implications of this are profound:
- Innovative Solutions: Often, the designs suggested are beyond what a human designer might conceive, yielding unique solutions that challenge traditional ideas.
- Time-Saving: Instead of laboriously iterating through designs, you receive several options at once, allowing for quicker decision-making.
- Integration of Constraints: Real-world factors like environmental conditions or production capabilities can all be factored into the designs generated by the software.
By diving into these advanced 3D design concepts, you're not just keeping up with trends—you’re becoming a pioneer in the field of additive manufacturing.
The Future of 3D Printing Design
The advancement of 3D printing technology holds the promise of transforming various industries. The future of 3D printing design goes beyond just creating prototypes; it encompasses a wide range of applications that can revolutionize manufacturing, healthcare, education, and even everyday consumer products. As we stand on the cusp of an era where the boundaries of what’s possible are continuously stretched, understanding these future dynamics becomes crucial for beginners who aspire to harness the full potential of 3D printing.
Benefits of Embracing the Future
New technologies and methods are emerging rapidly, enabling creators to push the envelope. For instance, sustainability is becoming a significant focus. By utilizing biodegradable materials and recycling old prints, designers can help reduce waste. Furthermore, customization meets the consumer’s demand for unique products, fostering a market where personalized items thrive. The drive for speed and efficiency in production processes is another key area where innovations can lead to significant time and cost savings. These elements highlight the importance of staying informed about future trends and adaptations in 3D printing design.
Considerations for The New Landscape
However, it is essential to consider regulatory aspects and intellectual property issues as the landscape evolves. With new technologies emerges the potential for misuse or infringement. As a designer, being mindful of these considerations not only safeguards one’s creations but also ensures ethical practices within the industry.
"3D printing will become the cornerstone of modern creativity, allowing ideas to be turned into reality with unparalleled ease."
As we delve deeper into the future, two key facets stand out: emerging trends and the increasing influence of artificial intelligence (AI).
Emerging Trends and Technologies
Several trends are shaping the path forward in 3D printing design.
- Bioprinting: One of the most exciting possibilities is bioprinting, where living tissues are created for advancements in medicine. This could potentially lead to customized organ implants that would reduce waiting lists for transplants.
- Mass Customization: Tailoring products to individual specifications is becoming more feasible with advanced software and printing techniques. The ability to create custom goods in bulk reflects a shift towards consumer-driven manufacturing.
- Multi-Material Printing: The ability to print with multiple materials simultaneously opens new doors for complex designs that can harness the strengths of various substances. This can enhance the performance and aesthetics of the final product.
- Integration with Robotics and Automation: As 3D printers become integrated with robotic systems, production could reach unprecedented speeds and accuracy, making large-scale manufacturing more cost-effective.
These emerging trends not only enhance the efficiency and capabilities of 3D printing but also invite designers to explore uncharted territories.
The Role of AI in Future 3D Design
Artificial intelligence is playing a pivotal role in shaping the future of 3D design. It can dramatically streamline the design process by automating basic tasks. Here are few ways AI is influencing this domain:
- Generative Design: AI algorithms can create multiple design alternatives based on predefined parameters and constraints. This allows designers to explore a broader range of possibilities while saving time.
- Optimization: AI can analyze designs for performance, suggesting improvements that may not be immediately apparent to the human eye. This can lead to stronger, lighter, and more efficient designs.
- Predictive Maintenance: In a production scenario, AI tools can predict when equipment is likely to fail, enabling proactive maintenance that minimizes downtime and improves productivity.
As technology advances, the synergy between AI and 3D printing design will continue to deepen, leading to breakthroughs that could redefine entire industries.
Finale
The closing chapter of this guide serves as a vital anchor, tying together the intricate threads of 3D printing design introduced earlier. In the world of additive manufacturing, the stakes can be high, and diversifying your knowledge base is truly the cornerstone of success. As we sum up the key insights, it's clear that this journey, though packed with technicalities, is profoundly rewarding.
Recap of Key Insights
In revisiting the main points discussed throughout the article, some essential takeaways deserve to be spotlighted:
- Understanding Basics: Recognizing the differences between 2D and 3D models laid the groundwork for effective design. Knowing common file formats is like having a trusty map on your 3D printing voyage.
- Software Choices Matter: Whether you opt for high-end or open-source software, your choice greatly impacts the design process. Each tool has distinct strengths, and knowing which one fits your style is crucial.
- Material Knowledge: Different projects call for different materials. The selection process is not just a checkbox; it’s about compatibility with your printer and desired result.
- Design Principles: Emphasizing aspects like strength, durability, and aesthetics makes all the difference in creating successful prints. Adhering to design for additive manufacturing ensures your creations hold up in both form and function.
- Practical Steps: From setting up printers to troubleshooting errors, real-world applications of these principles are what bring the designs to life after all.
The blend of technology, creativity, and practical insights paints a solid picture of what it takes to thrive in 3D printing.
Encouragement for Next Steps
As you stand at the precipice of your 3D printing journey, it’s imperative to carry the momentum forward. There’s no one-size-fits-all in the realm of design; consider your projects, your interests, and how you want to evolve. Take the knowledge you've gained here and explore further resources:
- Engage with online communities like reddit.com where enthusiasts share experiences, tips, and inspiration.
- Tap into dedicated podcasts and YouTube channels focusing on design and printing.
- Attempt small personal projects to apply your learnings — failure can often teach more than success.
Set realistic goals. Whether it’s perfecting a small object or tackling a complex design, approach each task with a learning mindset. In 3D printing, as with life, the journey truly matters. As new trends, tools, and technologies keep emerging, staying curious ensures you won’t be left behind. Go ahead, print your ideas into reality!