Crafting a 3D Print File: Step-by-Step Guide
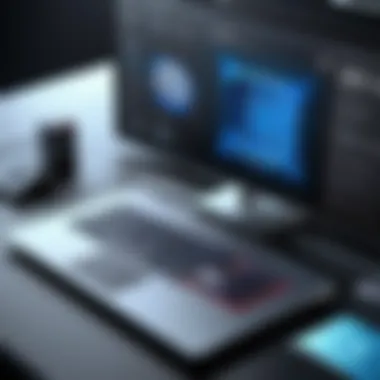
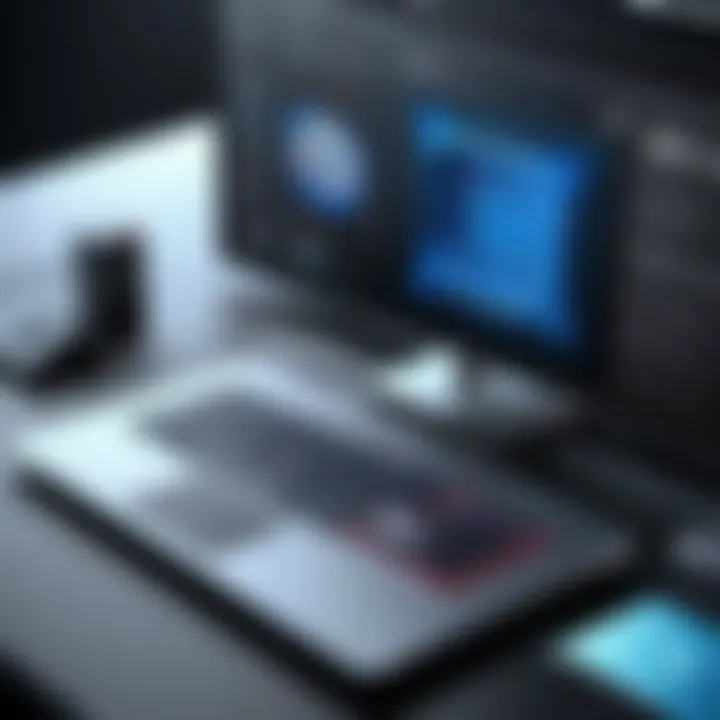
Intro
The realm of 3D printing is a captivating frontier, one that continues to evolve as technology advances. Creating a 3D print file is a crucial step in this fascinating process, serving as the bridge between a digital design and a tangible object. This guide aims to lift the veil on how to navigate through this intricate terrain, providing insights for everyone from curious novices to seasoned professionals.
With numerous methods at oneās disposal, the task may seem daunting at first. However, breaking it down methodically ensures a smooth sail. Weāll dive into different file formats, the essential tools required, and the step-by-step approach to transforming an idea into a fully realized model, ready for printing. Through this journey, readers will glean not just the mechanics, but also the art behind crafting efficient and viable 3D print files.
By the end of this guide, itās our aspiration that you feel empowered to create 3D print files confidently. So, letās roll up our sleeves and jump into the world of 3D file creation, setting the stage for innovation and creativity.
Product Overview
To effectively create a 3D print file, it's essential to understand the available software options. Here's a brief overview of some popular choices:
Brand Information
TinkerCAD: A user-friendly, web-based program ideal for beginners. It allows for easy modeling with a straightforward interface.
Fusion 360: A more complex tool suited for professionals. It combines CAD, CAM, and CAE in a single platform, perfect for High-end design tasks.
Blender: Open-source software known for its versatility in 3D modeling, sculpting, and animation. A bit of a steep learning curve, but immensely powerful.
Key Specifications
- TinkerCAD: Browser-based, easy drag-and-drop features, no installation required. Ideal for basic designs.
- Fusion 360: Cloud-based, collaborative features, parametric design, and simulation capabilities.
- Blender: 3D rendering, animation tools, Python scripting for customization.
Pricing
- TinkerCAD: Free to use.
- Fusion 360: Subscription model with offerings like free trials or educational discounts.
- Blender: Completely free.
Performance Comparison
When diving into 3D modeling software, performance can vary based on user needs.
Benchmark Tests
In terms of performance, hereās how these applications stack up:
- TinkerCAD: Quick rendering times due to its streamlined interface.
- Fusion 360: High-performance rendering but can lag on older computers.
- Blender: Excellent speed with complex models but needs a powerful computer.
Speed and Efficiency Comparisons
- TinkerCAD is great for rapid prototyping.
- Fusion 360 offers speed with complex designs, though it demands a bit more effort to master.
- Blender requires time investment to learn but yields stunning outputs once you get the hang of it.
Features and Technology
Unique Features
- TinkerCAD is great for beginners due to its highly visual interface.
- Fusion 360 stands out with its cloud capabilities, allowing for collaborative projects.
- Blender boasts extensive features for sculpting and texture painting, ideal for artists.
Technological Advancements
Each of these platforms continues to update and integrate advanced algorithms for improved modeling. From enhanced rendering engines to AI-assisted design, the technology is constantly evolving.
Compatibility with Other Devices
Most 3D modeling software can operate across various operating systems, though performance may vary. TinkerCAD being browser-based, is generally more accessible. Fusion 360 has mobile features, while Blender is often utilized on high-end gaming PCs for the best results.
Pros and Cons
Strengths of the Product
- TinkerCAD: Very few barriers for entry; excellent for educational purposes.
- Fusion 360: Robust features that cater to professionals; seamless collaboration.
- Blender: Unmatched versatility for creative projects, with a large online community.
Areas for Improvement
- TinkerCAD lacks advanced design features.
- Fusion 360 can be overwhelming for new users.
- Blenderās learning curve can deter beginners due to its complex interface.
Value for Money
Cost-Effectiveness
Both TinkerCAD and Blender are free, making them accessible to anyone. Fusion 360 offers a wealth of features for its price, especially for professionals.
Long-term Benefits
Investing time in learning Fusion 360 or Blender can lead to significant skill development and opportunities in design.
Comparision with Similar Products
Compared to alternatives like SketchUp or AutoCAD, these tools maximize both accessibility and features, catering well to a variety of users.
Overall, understanding these products helps lay the groundwork for creating quality 3D print files, steering you closer to successful prints. Whether you're just starting or brushing up on skills, there's always something new to learn in this vibrant landscape.
Understanding 3D Printing Basics
Getting to grips with the fundamentals of 3D printing is crucial for anyone looking to step into the world of additive manufacturing. This section sets the stage for the entire process of creating a 3D print file, ensuring that readers have a solid foundation to build upon. Understanding the principles behind this technology not only helps in developing better designs but also prepares one to tackle challenges that may arise during the modeling and printing phases.
Defining 3D Printing
3D printing, often referred to as additive manufacturing, is a process that transforms digital designs into physical objects. It works by laying down successive layers of material until the final shape is achieved. There are several different techniques involved, including Fused Deposition Modeling (FDM), Stereolithography (SLA), and Selective Laser Sintering (SLS). Each of these has unique characteristics and applications.
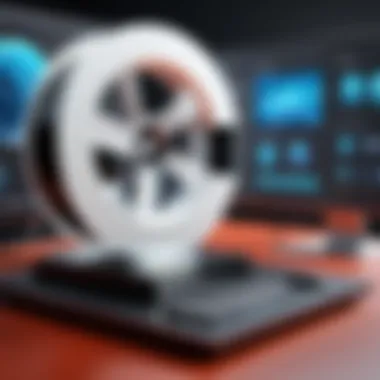
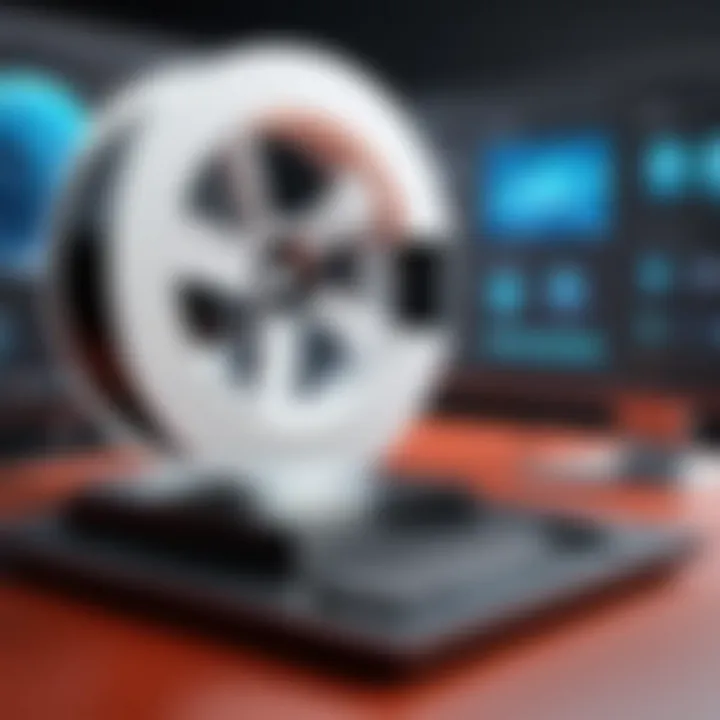
For instance, FDM is widely used for its cost-effectiveness and ease of use, while SLA offers higher resolution, making it suitable for intricate designs.
The definition of 3D printing covers a broad spectrum of possibilities but boils down to one key concept:
"Turning virtual concepts into tangible reality through layers of material."
This simple yet profound notion highlights the transformative power of this technology, which can be applied across a multitude of fields, ranging from prototyping in engineering to custom tools in medicine.
Applications of 3D Printing
The applications of 3D printing are extensive, driving innovation across various industries. Here are a few notable uses:
- Healthcare: Surgical tools, prosthetics, and even tissue scaffolds are being created with precision using 3D printing.
- Aerospace: Companies are producing lightweight components for aircraft that not only reduce fuel consumption but also enhance performance.
- Automotive: Customized parts and prototyping have made their way into assembly lines, speeding up the development of new vehicles.
- Consumer Goods: Businesses create everything from specialized kitchen gadgets to bespoke jewelry, catering to niche markets and personal preferences.
3D printing also enables rapid prototyping, allowing for quicker iterations. Thus, design flaws can be addressed at an early stage, saving time and costs. The flexibility of materials usedāfrom plastic to metalsāopens up avenues for innovation that simply were not possible before.
Understanding the basics of 3D printing empowers enthusiasts, gamers, and IT professionals alike to harness this technology effectively. With the groundwork laid, one can move on to the practical aspects of creating a 3D print file.
Essential Tools and Software
Creating a reliable 3D print file requires a toolkit of specific software and hardware. Understanding the utilities and equipment at your disposal is crucial for a successful 3D printing experience. From modeling to printing, the right tools can dramatically improve your workflow, ensuring the final product meets your expectations.
3D Modeling Software Overview
3D modeling software is the backbone of 3D printing. It allows users to create, modify, and prepare their designs for printing. Different programs cater to various skill levels and design requirements, making it important to choose one that fits your needs.
Blender
Blender stands out as a free and open-source tool that offers incredible flexibility for 3D modeling. Its powerful capabilities enable users to create complex shapes and animations. One of the key characteristics of Blender is its robust community, which contributes a wealth of tutorials and plugins.
A unique feature of Blender is its sculpting tools, which allow for advanced modeling techniques usually reserved for higher-end software. However, the learning curve can be steep and somewhat intimidating for novices. Despite this, its comprehensive toolkit makes Blender a popular choice for those serious about 3D design.
Tinkercad
On the other end of the spectrum lies Tinkercad, a web-based 3D modeling tool that's particularly friendly for beginners. Its drag-and-drop interface simplifies the design process, allowing users to construct models with ease. This toolās key characteristic is its accessibility, making it an excellent starting point for those new to 3D printing.
One major advantage of Tinkercad is that it requires no installation, and you can work directly in your browser. However, it may not provide the advanced features found in professional software like Blender, limiting its use for more intricate designs. Nevertheless, it's ideal for creating quick prototypes and educational purposes.
Fusion
Fusion 360 is a powerful tool developed by Autodesk that integrates parametric design capabilities with extensive modeling tools. A notable characteristic of Fusion 360 is its cloud-based collaboration features, allowing multiple users to work on a project simultaneously. This makes it a top choice for professionals working in teams.
The software offers a range of unique features, including built-in simulation tools and CNC machining capabilities. However, subscription costs can be a barrier for hobbyists, and its features may feel overwhelming for newcomers. Still, for those seeking robust functionality, Fusion 360 is an investment worth considering.
Choosing the Right Hardware
While software plays its part in creating 3D print files, your choice of hardware is equally important. A reliable computer equipped with sufficient processing power and memory can have a direct impact on your design and printing experience.
Computers and Laptops
When it comes to computers and laptops, having a machine tailored for 3D design can seriously enhance your workflow. A machine with a strong processor and ample RAM allows smoother rendering and faster modeling sessions. The key characteristic of a suitable computer includes a dedicated graphics card to handle intensive graphics tasks, which is crucial for complex designs.
Investing in a solid machine initially might seem steep, but it pays off with efficiency and time savings that help you focus on creating without frustration. On the flip side, lower-end machines could lead to lagging issues, which can hamper your productivity during crucial design phases.
Graphics Cards Considerations
The graphics card you select can make a world of difference. For 3D modeling, a powerful GPU can significantly speed up rendering times, especially if you're dealing with intricate designs. The key characteristic of a good graphics card for 3D modeling is its ability to handle high-resolution textures and complex visual effects.
For those creating detailed 3D models, opting for brands like NVIDIA or AMD can greatly benefit your projects. Yet, be mindful of budget limitations; high-end graphics cards can come at a premium. Nevertheless, they are often a worthy investment for serious projects, tending to deliver better performance in various 3D applications.
"Choosing the right tools can either propel your creativity or stifle itāit's not just about design, but about facilitating your ideas into tangible forms."
Creating a 3D Model
When it comes to bringing your ideas into the third dimension, creating a 3D model is the foundation upon which everything else rests. Getting this sketch right sets the stage for every aspect of the 3D printing process. From the design constraints to functional uses, a well-crafted model can mean the difference between a successful print and a failed attempt. This part of the guide sheds light on the pivotal elements of conceptualization and modeling techniques, two critical components in the whole shebang of 3D printing.
Conceptualization
Sketching Ideas
Sketching ideas is where imagination ignites. When you take a pencil and paper to begin drafting, itās a tactile experience that can lead to unforeseen creativity. This initial phase helps clarify thoughts, serve as a blueprint, and allows for experimentation without the fear of hitting delete. What's unique about this approach is that it encourages the free flow of ideas. The rawness of a sketch can often lead to original concepts, offering benefits like:
- Flexibility in changing designs quickly
- Personal touch, making each creation unique
- Visual feedback that aids in refining ideas further
However, it isnāt without its downsides. Some might struggle to translate those sketches into digital formats effectively. Thatās where attention to detail comes into play, as translating eye to hand can prove tricky.
Researching Existing Models
Researching existing models opens up a treasure trove of inspiration and guidance. By sifting through models in repositories like Thingiverse or MyMiniFactory, one can discover solutions to problems they may not have even considered. This part of the process shines a light on best practices, common pitfalls, and innovative ideas that can save hours of unnecessary work.
The key characteristic here is leveraging the community and knowledge thatās already out there. Advantages include:
- Avoiding common mistakes that others have faced
- Inspiration for designs based on proven works
- Access to tutorials and advice from experienced creators
On the flip side, relying too much on existing designs could stifle creativity, potentially leading to designs that feel derivative. Balance is key here.
Modeling Techniques
Polygon Modeling
Polygon modeling is the bread and butter for many 3D artists. It's based on creating a mesh, which is essentially a collection of points, or vertices, connected to form polygons. This method offers flexibility and control, allowing the artist to produce intricate shapes. The brilliance of polygon modeling lies in its adaptabilityāfor instance, adding detail in specific areas without affecting the entire model. Notable advantages include:
- Direct control over every aspect of the model
- Versatility to create organic shapes or hard surfaces
- Compatibility with most rendering engines
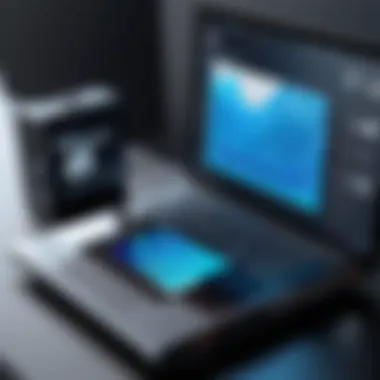
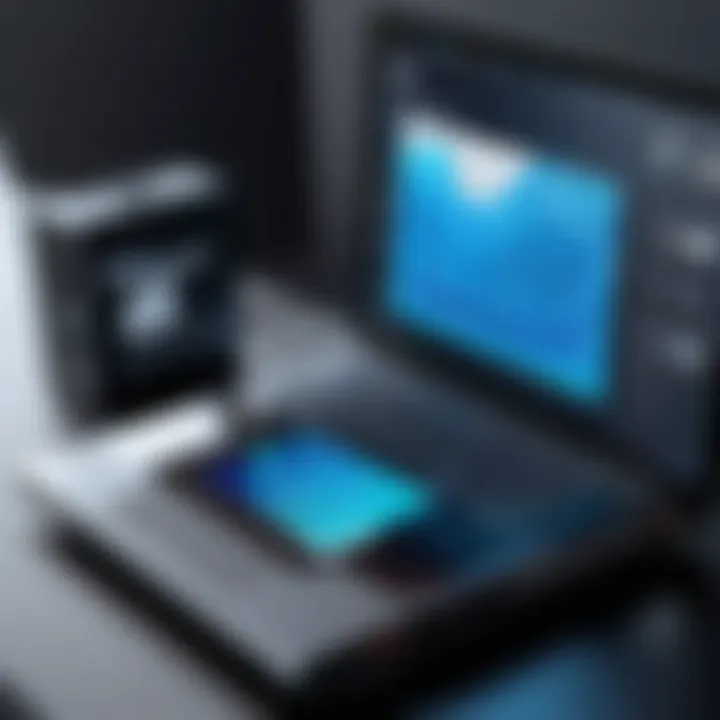
Conversely, it may require additional effort to produce clean topology. Models that donāt follow a logical flow can become troublesome when itās time for printing.
Parametric Modeling
Parametric modeling takes a different angle, focusing on parameters and constraints to shape the model. This methodology allows designers to input specifications so that changes will update the entire model dynamically. This represents an option some prefer for its precision and efficiency. Advantages of parametric modeling include:
- Easy modifications as changes reflect throughout instantly
- Designer-driven adjustments that require less guesswork
- Ideal for functional parts where dimensions matter
However, it isnāt always the first choice for creative ventures where freedom is essential. The rigidness of parameters can sometimes feel constraining, limiting artistic expression.
In summary, the creation of a 3D model is an essential step that lays the groundwork for successful 3D printing. Whether opting for freehand sketches or diving into various modeling techniques, a clear understanding of the different methods will greatly enhance the final outcome.
Exporting to the Correct File Format
When you arrive at the stage of generating a 3D print file, exporting it in the proper format is of utmost importance. Ensuring your model is saved in a format compatible with your 3D printer can make or break your printing experience. After all the time and effort put into designing a model, a simple error in format can lead to wasted materials, time, and potentially expensive print failures.
This section delves into various file formats used in 3D printing, highlighting their distinct contributions and functionalities. Understanding these formats not only aids in smoother transitions from design to production, but it can also empower creators to choose the right format specifically tailored to their printerās requirements and capabilities.
Common File Formats
STL
The STL file format is perhaps the most widely recognized in the 3D printing community. Its significance lies in its simplicity and its ability to effectively describe the surface geometry of a 3D object. An STL file contains a collection of triangular facets that represent the external surface of a model, making it an excellent choice when it comes to precise printing.
One of the standout characteristics of STL files is their compatibility with nearly every 3D printing software and hardware. This makes STL a go-to format for many enthusiasts and professionals. However, there are some drawbacks. For instance, an STL file does not support color information or complex textures, which can be a limitation when working on detailed models. Moreover, STL files can sometimes lead to conversion errors, which may necessitate additional repairs during the validation stage.
OBJ
The OBJ file format presents a more nuanced opportunity for 3D model designers. Itās known for its support of complex geometries and texturing capabilities, allowing for more detailed models that need to relay color information. This becomes particularly advantageous when creating rich, visually appealing designs.
A key characteristic of OBJ files is their ability to handle large and intricate models without sacrificing detail. This makes them a preferred choice for artists and designers looking to push the envelope of creativity. However, the downside to using OBJ files is their somewhat limited compatibility with certain slicing software compared to STL files. It's essential to check if your printing software can effectively read OBJ files to avoid any unexpected hiccups during the printing process.
AMF
Lastly, the AMF or Additive Manufacturing Format, is a newer candidate in the arena of 3D printing files. AMF has been developed to address some of the limitations inherent to STL, particularly in terms of color and material properties. Unlike its predecessors, AMF files can encode not only geometry but also support multiple materials and colors, providing a richer context for complex objects.
A notable feature of AMF is its ability to streamline the entire printing process, paving the way for more intricate designs without the typical headaches. Nonetheless, AMF's adoption isn't as widespread as STL and OBJ, which may pose challenges for compatibility with some older printers. Users need to confirm that their equipment or slicing software supports AMF to fully utilize its capabilities.
Choosing the Best Format for Your Printer
Selecting the right file format can greatly affect the outcome of your print. Factors contributing to this decision include the specifications of your printer, the complexity of your model, and the desired output quality. For example, if your printer has a strong preference for STL files, sticking to that format will lead to a smoother experience.
Preparing for Printing
Preparing for printing is a crucial phase in the 3D printing process. This step lays the groundwork for a successful print that meets the desired specifications. Emphasizing preparation can make the difference between a successful print that looks professional and one that ends up as a jumbled mess of plastic. Itās not just about hitting āprintā and hoping for the best; it requires careful planning and execution to ensure a smooth journey from digital design to tangible item.
Slicing the Model
Slicing Software Overview
Slicing software plays a pivotal role in transforming a 3D model into a series of instructions your 3D printer can understand. Think of slicing software as the translator between your design and the printer. It takes the 3D model and slices it into layers, creating a G-code file that directs the printer on how to move, extrude filament, and build the object layer by layer. Popular software options include Ultimaker Cura, PrusaSlicer, and Simplify3D.
One important characteristic of slicing software is its ability to customize settings based on the specific needs of the print job. For instance, you can adjust parameters such as layer height, print speed, and temperature settings, which can significantly impact the quality and precision of the final product. This customization ability makes slicing software appealing, as it offers flexibility depending on the project at hand. However, some software can have a steep learning curve, which might discourage beginners.
"The beauty of slicing software lies in its ability to turn the abstract into the concrete, making your vision a material reality."
Settings Adjustments
Once you've chosen your slicing software, the next step is making the necessary settings adjustments. Each printer and material has unique requirements, and understanding these can greatly influence print performance. Key characteristics here include adjusting layer height for finer details or modifying print speed for stronger infill.
Making informed adjustments to these settings ensures that your model is printed as intended. For instance, a lower layer height might yield a smoother finish, while higher speeds can decrease overall printing time but might compromise detail. Essentially, itās a balancing act between time efficiency and end result quality. A unique feature of settings adjustments is that they can be saved as profiles for future use, allowing for consistency in projects. However, if not done correctly, it can lead to wasted time and materials on failed prints.
Checking Model Integrity
Repairing Models
Model integrity is a vital factor to consider before firing up the printer. Examining your model for flaws can save time and ensure strong prints. Repairing models usually involves using specific tools that can identify and fix common issues like non-manifold edges or intersecting geometries. These problems can lead to failed prints or structural weaknesses. Many slicing softwares come equipped with built-in repair utilities, streamlining this process.
These tools are beneficial because they highlight areas needing attention, possibly enhancing your familiarity with common design pitfalls. However, over-reliance on repair tools can sometimes give a false sense of security, making it vital for the designer to hone their skills in detecting flaws directly within the modeling software.
Validating Mesh Quality
Mesh quality is another essential aspect to consider when preparing for printing. A model can look perfect on the surface, but underlying mesh issues can wreak havoc on the printing process. Validating mesh quality involves checking for any inconsistencies within the surface geometry that could lead to printing errors or compromised models.
Many professional software options offer mesh validation tools that evaluate the model and alert users to potential issues. This is especially advantageous for complex structures, where minor flaws could lead to significant problems down the line. Focusing on mesh integrity ultimately enhances the reliability of your prints, though itās essential to remember that not all software will have comprehensive validation tools, requiring some manual checking.
Common Challenges and Solutions
Creating a 3D print file isnāt always a walk in the park; several bumps along the road can cause frustration for both new and seasoned creators. Understanding these challenges and the solutions to overcome them is crucial for achieving success in 3D printing. Whether you're crafting a prototype or perhaps a unique piece of art, itās vital to know where pitfalls may lie and how to avoid them.
Dealing with Design Flaws
A common hurdle when embarking on 3D printing is encountering design flaws in your model. You may be excited about your design only to find it's not structurally sound or lacks the necessary details for a successful print. Recognizing potential flaws early can save a world of hassle later on.
Some key considerations include:
- Geometry Issues: Sometimes, the model might have non-manifold edges, which can cause printing failures. Using software like Blender can help check for these issues before printing.
- Scale Concerns: When scaling a model up or down, itās easy to miss details or create proportions that donāt make sense. Always verify dimensions in the modeling software to ensure fit.
- Overhangs and Support Needs: Designs with significant overhangs will need supports, which can complicate the print and the finish. Consider these elements during initial modeling rather than waiting till slicing.
By addressing these design flaws upfront, you can make the designing process smoother, saving time, materials, and of course, your sanity.
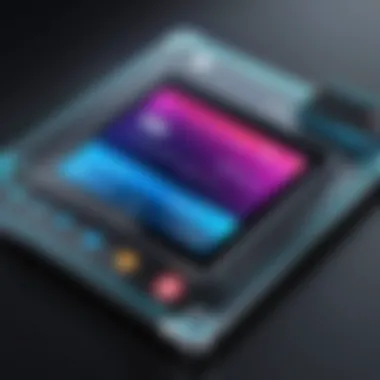
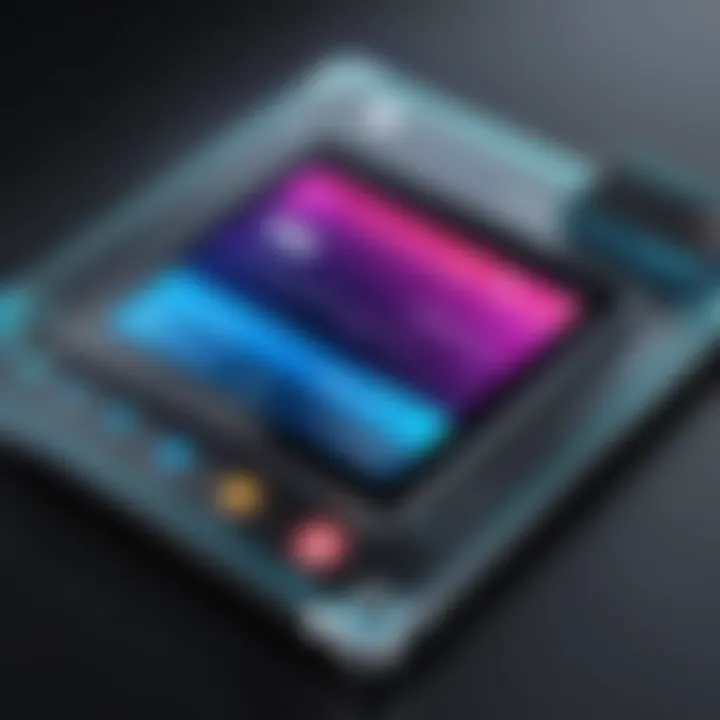
Material Considerations
Choosing the right materials significantly impacts the outcome of your 3D print. Understanding how different materials behave can inform your decisions, ultimately ensuring your projectās success.
Choosing the Right Filament
The filament you select can dramatically affect the final print. Popular choices include PLA, ABS, and PETG, each with unique characteristics. PLA is known for its ease of use and biodegradability, making it an excellent choice for beginners or those looking for environmentally friendly options. It adheres well to the build plate and usually works well on most consumer printers.
However, itās not as heat resistant as ABS, which can handle higher temperatures but is more notorious for warping during the printing process. Thus, picking filament comes down to understanding not just what prints well, but also what fits your particular needs.
- Key characteristic: Ease of use for PLA and high durability for ABS.
- Unique feature: PLA is biodegradable, ABS can be post-processed with acetone.
These factors make the right filament a cornerstone of your 3D printing success.
Understanding Material Properties
When it comes to materials, knowing their properties can furnish you with the insights needed for high-quality prints. This facet includes thermal characteristics, tensile strength, and flexibility, among others.
For example, knowing that PETG is more flexible than PLA means you might opt for it in applications that require a certain degree of bending without breaking. Being aware of a materialās reaction to different printing speeds and temperatures can also guide adjustments that enhance print quality.
- Key characteristic: PETGās flexibility can reduce the risk of failure in certain designs.
- Unique feature: Each material responds differently to post-processing treatments such as sanding or painting, which can influence the overall aesthetic of your print.
Understanding these material properties helps you select the most suitable options, leading to a more polished and reliable finished product.
"A great design demands great material choices; only then does a vision come to life on the printer."
By mastering the hurdles of design flaws and material considerations, you lay a strong foundation for successful 3D printing endeavors, ensuring your creativity finds its expression without unnecessary roadblocks.
Post-Processing Techniques
Post-processing is a crucial stage in the 3D printing process that takes place after the printing is complete. While creating a 3D print file may have captured most of the attention, the final touches can dramatically influence the quality and appearance of the print. Post-processing techniques can transform a basic print into a professional masterpiece, enhancing its functionality and aesthetic. The process typically includes cleaning the print and adding finishing touches, both of which play significant roles in the overall outcome.
Ignoring post-processing can lead to a mediocre final product. Thus, understanding and applying these techniques is vital for achieving desired results in 3D printing, whether for hobbyist projects or professional applications.
Cleaning the Print
Cleaning the print is often the first step in post-processing. After the printer has deposited all the materials and the final shape emerges, various residues such as support structures and unbonded powders may linger. This cleaning phase is important not just for aesthetics but also for durability. A clean print ensures better adhesion for any subsequent processes, like painting or sanding.
Common cleaning techniques include:
- Water Wash for washable filament, such as PVA.
- Isopropyl Alcohol for cleaning PLA or ABS prints, especially when using a resin printer.
- Soft brushes or toothpicks can help in getting rid of small particulates without damaging the structure.
After the print has been thoroughly cleaned, itās crucial to allow it to dry completely, avoiding any moisture that could interfere with painting or other finishing techniques later.
Finishing Touches
Adding finishing touches can elevate a print from basic to extraordinary. Two common methods are painting and sanding, both of which require different considerations and techniques.
Painting
Painting is arguably one of the most transformative post-processing techniques available to creators. Its primary contribution is in enhancing the visual appeal of a print. Paint can cover imperfections, add detail, and even protect the surface from wear and tear.
One key characteristic of painting is variety. From spray paint to brush applications, options abound, allowing for numerous styles and finishes. Using acrylic paints is a popular choice due to their fast drying time and versatility.
However, painting requires preparation. Priming the print can result in a smoother and more even finish. The unique feature of paint is that it can bring color and detail to life, but the disadvantage might be some prints needing multiple coats to achieve the desired vibrancy and depth.
Sanding
Sanding serves a different but equally important role. Itās primarily aimed at achieving a smooth finish by removing layer lines that are often visible in the printed object. This technique can enhance the tactile quality of a print, making it more pleasing to touch and observe.
One significant advantage of sanding is that it can greatly reduce the visibility of layer lines, leading to a finish that resembles a factory-produced piece. The use of varying grits, starting from coarse and moving to fine, allows for a gradual refinement of the surface. However, excess sanding can also lead to a distortion of fine details, which is something to be cautious about.
In the world of 3D printing, post-processing is not just an afterthought; it can define the success of your project.
Future Trends in 3D Printing
The world of 3D printing is rapidly evolving, combining ingenuity with technology to shape the future of design, manufacturing, and healthcare. Understanding these trends is crucial for anyone involved in the creation of 3D print files. As we wade deeper into the 21st century, advancements could radically transform our interactions with materials, pushing boundaries that define whatās possible in various industries.
Advancements in Technology
The pace of technological advancement in 3D printing cannot be overstated. Innovations such as multi-material printing, where different materials can be fused into a single object, open up new pathways for creativity. Furthermore, small scale robots and automation integrated into the printing process not only optimize the speed of production but also enhance precision, minimizing the risk of errors.
In addition, the adoption of artificial intelligence in design optimization is something to keep an eye on. AI can quickly analyze vast amounts of data, suggesting ideal adjustments to models before the printing process even begins. This ensures that the models are as effective and resource-efficient as possible, leading to a less wasteful production cycle.
Potential Applications in Various Industries
Healthcare
In healthcare, 3D printing is not just a trend; itās a revolution. The ability to create custom implants, prosthetics, and even biological tissues significantly enhances patient care. One of the key characteristics of 3D printing in healthcare is its personalization; each item can be tailored to the patient's needs, ensuring a better fit and functionality. For instance, using 3D bioprinting, researchers are experimenting with printing human tissues, which could lead to transformative breakthroughs in transplantation.
Advantages of this approach include reduced manufacturing time and costs. However, challenges like regulatory hurdles and ethical considerations persist, as the technology races ahead of governing frameworks.
Aerospace
In aerospace, the significant contribution of 3D printing lies in its ability to produce lightweight components, essential for fuel efficiency. Unique features of this sector include the production of spare parts on demand, which reduces the need for extensive inventory and streamlines operation processes.
Moreover, custom components can be produced without the intricate tooling typically required in manufacturing, allowing for rapid prototyping and testing. However, the main disadvantage is the stringent certification process that parts must go through to ensure safety and reliability, which often slows down implementation.
Automotive
3D printing in the automotive industry signifies a shift towards more sustainable practices. By allowing engineers to design complex parts that traditional manufacturing methods may struggle with, it enhances performance while reducing waste. A considerable benefit here is the agility in production; adjustments to designs can be made instantly without the significant overhead associated with changing molds or tooling.
However, the challenge lies in the varying material properties that may not yet match those of conventionally manufactured parts. Companies often face trade-offs between the speed of production and the durability of printed components, which is something to be mindful of as standards evolve.
"The future will be a blend of high-tech tools and traditional craftsmanship, as makers have the power to shape their visions into reality."
In summary, understanding these trends is limited to recognizing the intricate balance between innovation and practicality. With every advancement in technology, more industries are poised to benefit, leading us toward a future where 3D printing is ubiquitous. By grasping these shifts, tech enthusiasts, gamers, and IT professionals can stay prepared for the next wave of opportunities in this engaging field.