Creating 3D Printer Designs: A Comprehensive Guide
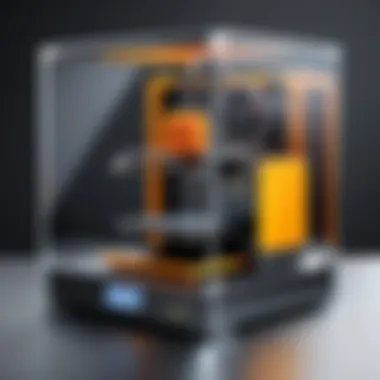
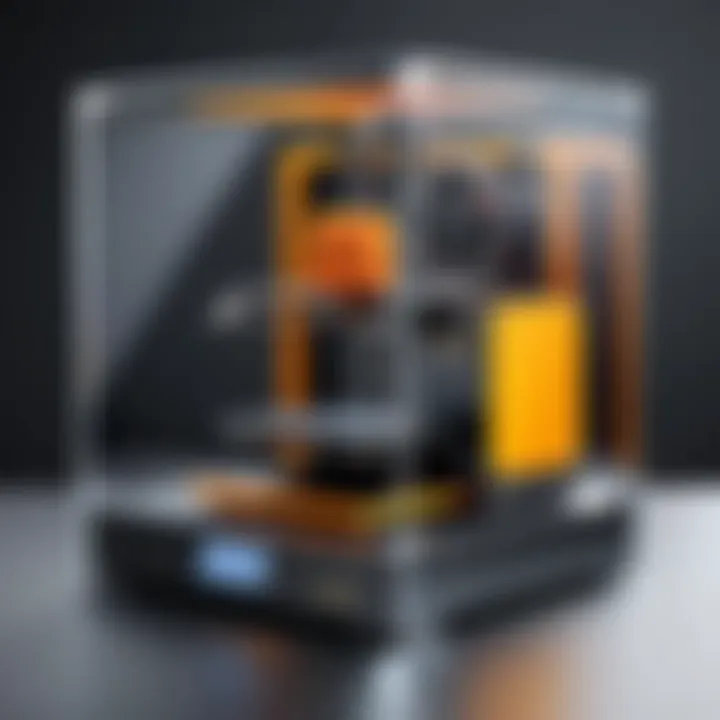
Intro
The world of 3D printing continues to grow, attracting tech enthusiasts and professionals alike. Creating effective 3D printer designs requires a thorough understanding of various components and processes. This guide will examine the important aspects of developing 3D printer designs, including essential tools, design principles, and practical approaches to common challenges.
In this guide, we will not only explore the tools and technologies behind 3D printing but also the concepts that ensure a successful design. The objective is to provide a comprehensive overview that can serve as a valuable resource for anyone interested in creating functional and innovative 3D printed models.
Product Overview
When discussing 3D printer designs, it is crucial to understand the variety of 3D printing technologies available today. These include Fused Deposition Modeling (FDM), Stereolithography (SLA), and Selective Laser Sintering (SLS), among others. Each technology serves a unique purpose and comes with different specifications.
- Brand information: Individuals may consider brands like Ultimaker, Formlabs, and Prusa Research.
- Key specifications: Attributes such as build volume, layer resolution, and material compatibility are significant. For instance, a typical Ultimaker printer might offer a build volume of 223 x 223 x 205 mm and a layer resolution down to 20 microns.
- Pricing: Price ranges vary widely among brands and models, with options available from budget-level printers around $200 to professional-grade models exceeding $10,000.
Performance Comparison
Performance differs not only between brands but also types of 3D printers. For instance, FDM printers might be faster but offer less resolution compared to SLA printers.
- Benchmark tests: Evaluations might include print speed and accuracy metrics.
- Speed and efficiency comparisons: A high-quality print created on an SLA printer may take longer but results in a much more detailed product than that of a standard FDM printer.
Features and Technology
New technologies regularly emerge within the 3D printing ecosystem. Understanding their applications can help in selecting the right tools for design.
- Unique features: Some printers come equipped with advanced features like automatic bed leveling or multi-material capabilities.
- Technological advancements: Innovations like resin-based printing and reinforcement filaments offer new possibilities in strength and detail.
- Compatibility with other devices: It is essential to ensure that your chosen printer is compatible with widely-used software like Autodesk Fusion 360 or TinkerCAD.
Pros and Cons
When choosing a 3D printer, weighing the strengths and weaknesses is vital.
- Strengths of the product: High-quality prints, versatility in materials, and ease of use can be significant pros.
- Areas for improvement: Some printers may have limited material compatibility, longer print times, or higher operational costs.
Value for Money
Assessing cost-effectiveness is important to determine if a 3D printer is worth the investment.
- Cost-effectiveness: Consider not only the price of the printer but also materials and maintenance costs over time.
- Long-term benefits: The capacity to create prototypes or personalized models may outweigh initial expenses.
- Comparison with similar products: Evaluating multiple brands and models assists in making a more informed decision.
"Investing in a 3D printer may enhance your creative capabilities and professional skills by providing hands-on experience in design and production."
In summary, understanding the intricacies of creating 3D printer designs can empower tech enthusiasts and professionals. By examining different technologies, features, and practical considerations, this guide aims to facilitate a fruitful journey in the world of 3D printing.
Prelims to 3D Printing Design
The field of 3D printing design has emerged as a crucial area of interest for tech enthusiasts and professionals alike. As technology advances, so do the capabilities of 3D printers, making the understanding of design principles essential. This section elucidates the significance of diving into the world of 3D printing design, shedding light on both the technical aspects and creative opportunities it offers.
Understanding 3D Printing Technology
Before delving into the design itself, itโs fundamental to grasp the underlying technology of 3D printing. At its core, 3D printing, or additive manufacturing, involves creating three-dimensional objects from a digital file. This process involves layering materials, often thermoplastics like PLA or ABS, until the final model takes shape. Each layer is precisely laid down according to the digital blueprint, allowing for intricate designs that traditional manufacturing methods might not achieve.
Recent advancements have greatly improved the accuracy and speed of 3D printers. High-resolution printers can create detailed objects, making it possible to prototype complex designs quickly and efficiently. This accessibility to advanced technology broadens the horizons for designers at all levels, from hobbyists to seasoned professionals.
The Importance of Design in 3D Printing
Design serves as the backbone of effective 3D printing. The quality of the final printed object relies heavily on a well-considered design. An effective design not only meets functional requirements but also considers aesthetic and practical factors. Understanding the implications of design helps reduce errors during printing, which can save both time and material costs.
Key points about the significance of design in 3D printing include:
- Functionality: The design must fulfill the intended purpose. For example, if creating a mechanical part, it should withstand the required stress and strain.
- Aesthetics: In many cases, the visual appeal of the final product matters. Designers must balance form and function creatively.
- Sustainability: With increased focus on the environment, designers are urged to consider materials that minimize waste and reduce the carbon footprint during the printing process.
Furthermore, a well-thought-out design often enhances the user experience. For instance, ergonomic considerations can significantly affect how a product is perceived and utilized. Thus, mastering the art of 3D printer design goes beyond technical skills; it intertwines creativity, function, and sustainabilityโa combination essential for modern innovations in various sectors.
"A fascinating design can intersect with practicality, pushing the limits of what's possible in 3D printing and leading to groundbreaking applications across industries."
With these foundational concepts in mind, one can appreciate the intricate relationship between design and technology in 3D printing. The coming sections will explore fundamental design principles and software tools crucial for producing effective 3D designs.
Fundamental Principles of Design
Understanding the fundamental principles of design is crucial in the realm of 3D printing. These principles help to ensure that designs are both functional and visually appealing. When creating 3D models, adhering to these core concepts can optimize the efficiency and effectiveness of the design process.
Basic Design Concepts
Basic design concepts involve understanding how elements interact in a 3D space. These include balance, proportion, hierarchy, and contrast.
- Balance refers to the distribution of weight in a design. In 3D printing, achieving a balanced design can prevent structural failure during printing and enhance the final product's usability.
- Proportion defines the size relationship between different elements in a model. Proper proportions ensure that parts of the design work together harmoniously, making the final output visually and functionally coherent.
- Hierarchy establishes the importance of different elements within the design. It guides the viewer's eye and helps convey the purpose of different features within a 3D printed object.
- Contrast enhances the visual interest of a design. It is achieved through variations in colors, shapes, and materials. Effective use of contrast can elevate the overall quality of a design.
Incorporating these concepts leads to designs that are appealing and functionally robust.
Prototyping vs. Production Design
There is a distinct difference between prototypes and production designs. Understanding these differences is essential for anyone involved in 3D printing.
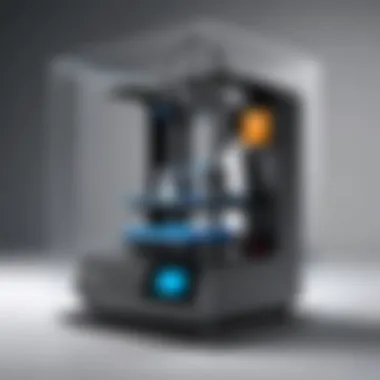
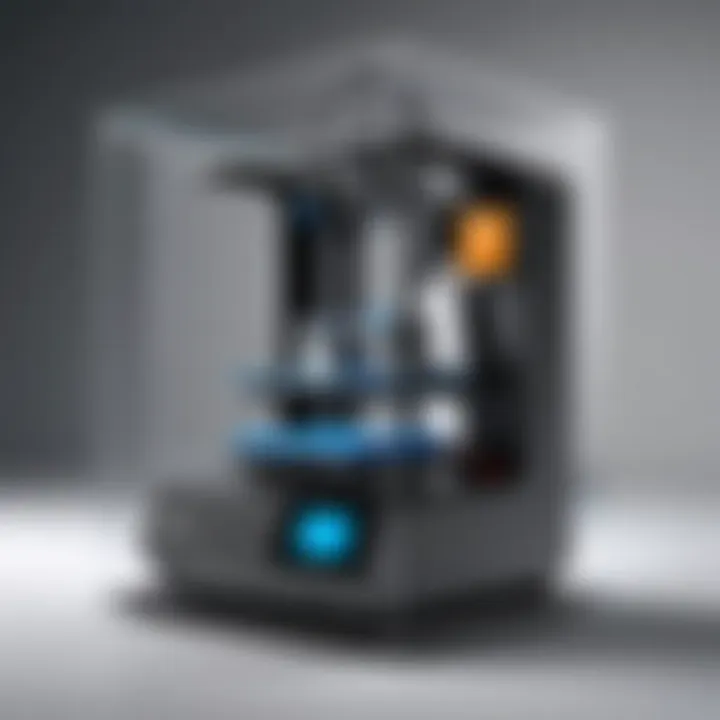
- Prototyping is generally the first step in the design process. It involves creating a preliminary model to evaluate ideas quickly. Prototypes help identify potential flaws in the design before actual production. They allow for rapid iterations and refinements without a significant investment of time and resources.
- Production design, on the other hand, is the final iteration that will go into mass production. This stage demands rigorous attention to detail, as it defines the quality and performance standards of the product. Produced items must meet specific requirements for strength, durability, and aesthetic standards.
Knowing when to prototype and when to move to production can save time and costs. It is a balancing act between understanding urgency and achieving perfection. A well-produced design can lead to effective outcomes in the intended use of 3D printed objects.
"Diverse design principles significantly influence the efficacy of 3D printed models. It is essential to understand both basic concepts and the distinction between prototype and production stages to create successful outcomes."
Software Tools for 3D Design
The selection of appropriate software tools is essential for effective 3D design. Technology plays a crucial role in the creation of 3D models, as it not only aids in visualization but also in ensuring precision and efficiency in the design process. Various software options cater to different user needs, ranging from beginners to advanced professionals. Understanding the strengths and limitations of these tools is vital for optimizing the design workflow.
Overview of CAD Software
Computer-Aided Design (CAD) software serves as the backbone for many 3D modeling projects. Tools like Autodesk Fusion 360, SolidWorks, and Rhino provide robust environments for drafting and modeling. They allow users to create 3D objects with high levels of accuracy.
These tools support features such as parametric design, which enables users to manipulate object parameters dynamically.
Why is CAD important?
- Provides accurate modeling for complex designs.
- Enables users to visualize designs in 3D early in the process.
- Often includes simulation capabilities to test functionality before printing.
Understanding how to utilize CAD tools effectively can streamline the design process and lead to superior end products.
Best Software for Beginners
For those just starting in 3D design, user-friendly software is crucial to ease the learning curve. TinkerCAD is a notable option that offers an accessible interface and intuitive controls, making it a great choice for novices. It is web-based, requiring no substantial computing resources.
Additionally, SketchUp can be a good choice, especially for architecture-oriented projects. Its vast library of pre-made objects aids beginners in visualizing 3D spaces.
Key benefits of beginner software include:
- Simple drag-and-drop functionality.
- Community resources for support and tutorials.
- Free or affordable entry points for users.
Advanced Software Options
For established designers seeking advanced capabilities, software like Blender and Maya provide extensive features. Blender is particularly powerful, offering modeling, animating, and rendering tools in a single package.
Maya is favored for its strength in character modeling and animation, often utilized in film and game design. Both options, however, do require a steeper learning curve compared to beginner tools.
When exploring advanced software, consider the following:
- The specific requirements of your projects.
- The existing expertise of users within your team.
- Support for various file formats suitable for 3D printing.
"Choosing the right software can greatly impact your 3D printing quality and efficiency. It is important to match your tool selection with your design goals."
By understanding the landscape of 3D design software, designers can take significant strides in enhancing their skills and output.
Types of 3D Printer Designs
The types of 3D printer designs are essential to understanding the overall impact of this technology. Each design category offers unique functionalities and benefits that cater to different needs and industries. Whether creating functional parts, aesthetic objects, or customizable models, the design type influences not just the printing process but also the material choice and end-use application.
In this section, we will explore three primary types of 3D printer designs: functional designs, aesthetic designs, and customizable designs. Each of these categories presents specific considerations and opportunities for creators.
Functional Designs
Functional designs are perhaps the most pragmatic application of 3D printing. These designs serve specific purposes, such as mechanical parts, prototypes, or even tools. They are meant to function effectively under real-world conditions, which demands a careful selection of materials and design techniques. The importance of precision is vital here; a slight error can compromise the entire functionality of the printed object.
Key aspects of functional designs include:
- Material durability: Choosing resilient materials like ABS or PETG is often necessary for parts that endure stress.
- Mechanical properties: Designers must understand how load and stress will affect the printed object.
- Prototyping: Many industries rely on rapid prototyping for product development which allows for testing and modification before mass production.
Functional designs are widely used in areas like automotive and aerospace engineering, making this type of design a critical aspect of 3D printing applications.
Aesthetic Designs
Aesthetic designs focus on visual appeal rather than functionality. These designs are more artistic and can include sculptures, decorative items, or custom designs for personal or artistic expression. Aesthetic designs often allow greater freedom of creativity, resulting in unique and innovative forms.
Considerations for aesthetic designs include:
- Surface finish: The appearance after printing can vary greatly depending on the 3D printer's resolution and material used.
- Color options: Many modern printers can handle multiple colors, offering more ways to enhance visual appeal.
- Design complexity: Detailed designs can push the limits of what a printer can achieve, challenging the designer's skills.
Consequently, this type of design is popular among artists and creators who aim to push the boundaries of creativity in 3D printing.
Customizable Designs
Customizable designs allow for the personalization of 3D printed objects. This approach caters to customer preferences and requirements, making them highly relevant in today's consumer market. Customization can vary from simple adjustments to complex modifications depending on user interaction with the design process.
Benefits of customizable designs include:
- User engagement: Consumers can engage with brands by choosing features that matter to them.
- Market differentiation: Businesses can stand out by offering unique, custom solutions.
- Technology utilization: Many design software tools now offer user-friendly interfaces, allowing non-professionals to create or modify designs.
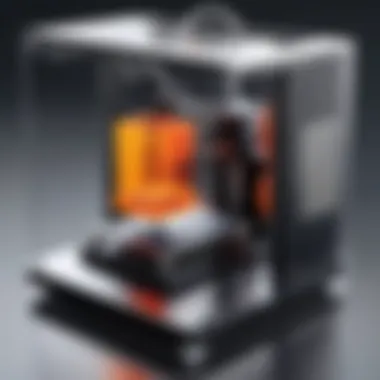
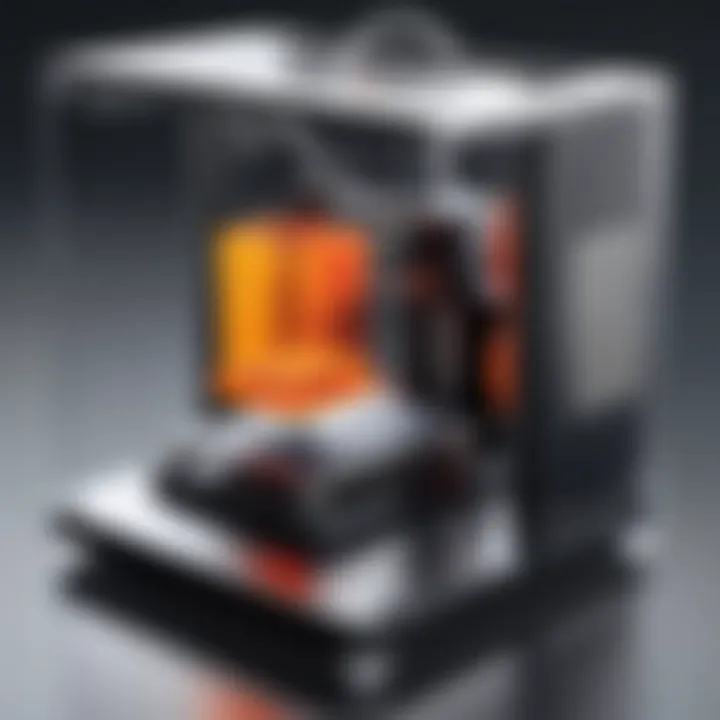
In summary, the variety of 3D printer designs provides distinct advantages and challenges. Understanding functional, aesthetic, and customizable designs is fundamental for anyone looking to leverage 3D printing technology effectively.
Steps for Creating 3D Printer Designs
The steps involved in creating 3D printer designs are a vital aspect of the entire process. These stages are not just procedural tasks; they are interlinked elements that determine the quality, usability, and final outcome of the printed models. The importance of these steps is primarily to provide a structured approach that reduces errors, optimizes design efficiency, and enhances creativity.
Conceptualization
The conceptualization phase serves as the foundation for any 3D design. During this stage, the designer identifies the purpose and intended application of the model. Understanding why a design is needed and how it will be used ultimately influences all subsequent decisions.
Key considerations during conceptualization include:
- User requirements: Who will use the final product? This informs practicality.
- Environment: Will the product be used indoors, outdoors, or in specialized settings?
- Aesthetic versus functional needs: Sometimes, designs must blend both demands.
Developing a clear concept reduces ambiguities, ensuring that designers can move into the modeling phase with confidence.
Modeling Techniques
Modeling techniques refer to the methods employed to bring the conceptualized idea to a visual form using software tools. There are various methodologies that can be used, each with pros and cons.
- Parametric Modeling: In this method, designers create objects with defined parameters. Changes in parameters adjust the model dynamically, promoting flexibility.
- Direct Modeling: This approach offers freedom, allowing designers to manipulate geometry without the need to define parameters.
- Mesh Modeling: Mesh techniques are useful for organic shapes and detailed designs. They can be more complex but can yield highly intricate results.
Using the right technique is essential as it can influence not only the ease of design but also the compatibility of the model with different printing technologies. Remember that collaboration with others can enhance this step. Getting feedback from peers can spark new ideas.
Preparation for Printing
Preparation for printing is crucial. It involves various pre-print tasks to ensure successful execution during the actual printing phase. This step converts the model into a format that a 3D printer can understand, often using slicing software.
Important actions during this phase include:
- Slicing the model: This process divides the 3D model into layers, preparing it for the printer. Each layer's thickness can significantly impact the quality of the print.
- Adjusting settings: Effective adjustment of print speed, temperature, and infill density is necessary. Each printer has specific requirements.
- Validating the model: Checking for errors like non-manifold edges or intersecting geometries helps prevent printing failures.
Effective preparation minimizes waste of materials and time, leading to a successful print.
"Understanding each step is crucial for a seamless design-to-print workflow, which often makes the difference between success and failure in 3D printing."
Through methodical steps of conceptulization, modeling, and preparation, designers can navigate the complexities of 3D printing with greater finesse, leading to innovative and effective outcomes.
Material Selection and Its Impact
Material selection plays a crucial role in the process of creating 3D printer designs. The choice of material not only influences the final appearance of the printed object but also affects its durability, functionality, and cost. Understanding the properties of different materials can make a significant difference in achieving the desired outcome for a project.
Choosing the right material is about striking a balance between performance and practicality. For example, certain materials may provide high strength and heat resistance, which is important for functional parts. Others may offer a wide range of colors and finishes that enhance aesthetic appeal. Each type of material has unique characteristics, and understanding these can help creators make informed decisions that align with their project's objectives.
Benefits of selecting the correct material include:
- Enhanced functionality: Using the right material can ensure that the printed object performs its intended function effectively.
- Cost-efficiency: Some materials are more cost-effective than others, especially in large-scale production.
- Sustainability: Increasingly, there are more environmentally friendly materials available, catering to eco-conscious designers.
Considerations in material selection involve understanding the requirements of the project, including strength, flexibility, weight, and appearance. These factors can dictate the appropriateness of a specific material for a given application. By addressing these elements, designers can maximize the effectiveness of their 3D designs, ultimately leading to successful outcomes.
Common 3D Printing Materials
The realm of 3D printing encompasses a diverse array of materials. Each serves specific needs and applications. Some of the most common materials include:
- PLA (Polylactic Acid): This biodegradable plastic is widely used, especially in hobbyist projects. It is easy to print with and offers good appearance, but its heat resistance is lower compared to other materials.
- ABS (Acrylonitrile Butadiene Styrene): Known for its strength and durability, ABS can withstand higher temperatures and is ideal for functional components. However, printing requires careful temperature control to avoid warping.
- PETG (Polyethylene Terephthalate Glycol): This material combines the ease of use of PLA with the durability of ABS. It is chemically resistant and less prone to warping.
- Nylon: Renowned for its strength and flexibility, Nylon can be more challenging to print due to its tendency to absorb moisture.
- TPU (Thermoplastic Polyurethane): A flexible material, TPU is excellent for applications requiring rubber-like qualities, such as phone cases or wearable items.
Each material has its benefits and potential drawbacks, making it essential for designers to consider their project requirements closely before making a selection.
Material Properties and Their Implications
Understanding the properties of materials is fundamental for effective 3D design. Key properties include:
- Mechanical Strength: The resistance to deformation and breakage under stress is crucial for functional applications.
- Thermal Stability: The ability to withstand high temperatures without losing integrity can impact the usability of printed parts in elevated heat environments.
- Flexibility and Rigidity: Depending on the application, some designs may require flexible materials, while others need rigidity for structural integrity.
- Surface Finish: Aesthetic qualities like smoothness and texture can enhance the visual appeal of a printed item.
"The choice of material can significantly alter not only the durability but also the visual quality of a 3D printed object."
Each of these properties may alter how a design is conceptualized and executed. For instance, mechanical strength is vital for parts that bear loads, while aesthetic properties might play a larger role in artistic creations.
Challenges in 3D Design Creation
Creating effective 3D printer designs is a complex endeavor. This complexity arises from various challenges that can impede the design process. Addressing these challenges is vital. Understanding them can lead to better design outcomes and improve the printing phase. Successful navigation of these obstacles not only enhances product quality but also reduces waste and saves valuable time.
Technical Limitations
Every 3D design begins with ideas but soon faces technical limitations. These limitations often include software capabilities and hardware constraints. Software may not always support the features a designer envisions. For instance, a robust computer-aided design application might lack the capability to handle intricate mesh structures effectively. Likewise, the printer itself might not support certain design features due to its build volume or resolution.
- Resolution Issues: High detail can be lost if a design exceeds the printerโs resolution capabilities.
- Material Limitations: Each material has its properties. Not every design can be manufactured using all materials. Some designs may require flexible materials, while others need rigidity.
- Printing Speed: The speed of the printer can affect the overall quality. Faster printing may result in quality issues.
In summary, recognizing these technical limitations allows designers to align their concepts more closely with what is practically achievable.
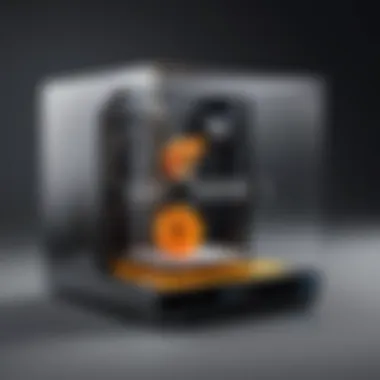
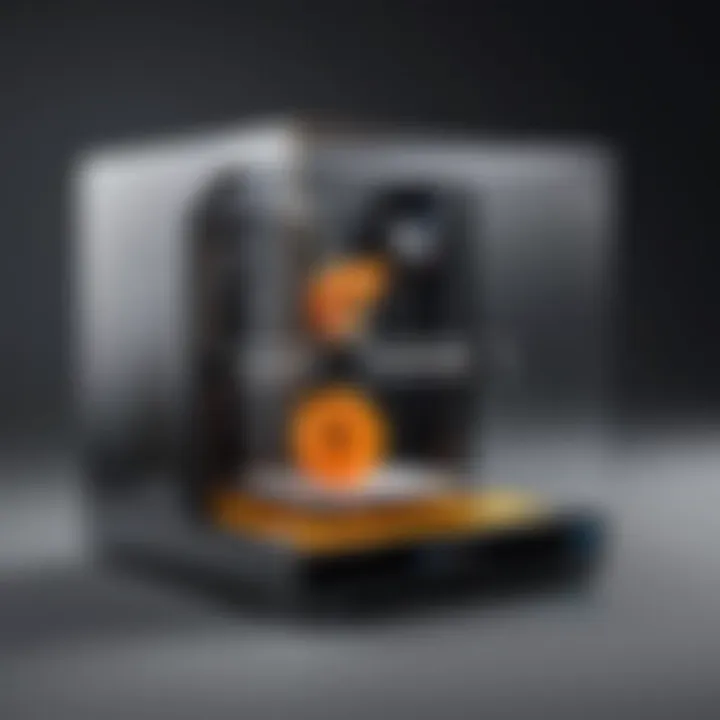
Design Constraints
Design constraints are also a significant concern in the 3D printing process. These constraints can be based on various factors including performance specifications, regulatory needs, and even aesthetic considerations. Each constraint shapes the outcome and should be meticulously pondered during the design phase.
- Functional Constraints: The design must meet its intended function without sacrificing safety.
- Aesthetic Boundaries: While functionality is paramount, visual appeal can also play a crucial role. A design that is visually engaging could lead to greater user acceptance.
- User Experience: Ensuring usability is essential. Designs should cater to the userโs needs and ergonomic factors.
Understanding these challenges allows designers to innovate within a set framework, ensuring that while creativity is not stifled, it is adequately directed toward feasible and marketable outcomes.
Best Practices for Efficient Designing
In the realm of 3D printing, best practices for designing models are crucial for ensuring both functionality and aesthetic appeal. Implementing efficient design practices can significantly impact the success of a project. These practices help minimize errors, reduce waste, and promote a smoother workflow. When designs are optimized from the start, they can save material and time, which are vital resources in the 3D printing process. Therefore, understanding and applying best practices becomes essential for tech enthusiasts and professionals alike.
Iterative Design Process
An iterative design process is foundational in creating effective 3D printer designs. This approach emphasizes continuous improvement through repeated cycles of designing, prototyping, and refining. By embracing an iterative mindset, designers can address flaws early and test various concepts before committing to a final model. This process allows for adjustments based on real-world performance rather than assumptions.
"Iteration is key to innovation. Through refining ideas, we can achieve optimized results."
To implement an iterative design process:
- Start with a rough concept: Begin with a basic idea and sketch it out.
- Create prototypes: Use 3D software or even 3D print basic versions of the design to test functionality.
- Gather feedback: Share the prototypes with peers or potential users to gather their insights.
- Refine the design: Apply feedback and rework the model. This may involve adjusting dimensions, materials, or aesthetics.
- Repeat: Continue this cycle until the design meets the desired standards.
By following this method, designers can ensure that the final product is not only usable but also meets user needs effectively.
Feedback and Testing
Feedback and testing are integral components of the design process. They provide valuable insights that help improve designs. Collecting user feedback ensures the final product aligns with what the intended audience wants. Testing, on the other hand, allows designers to validate assumptions about the model's function and design.
To effectively incorporate feedback and testing:
- Engage users early in the process: This can include surveys, interviews, or practical tests of a prototype.
- Conduct functional tests: Ensure that the design operates as intended under different conditions. This could include stress tests or user scenarios.
- Be open to criticism: Constructive criticism can identify blind spots in design considerations.
- Document findings: Keep detailed notes on what worked and what did not, which can inform future projects.
Finally, always remember that design is not a one-time event but a dynamic and evolving process. Incorporating feedback and rigorous testing enhances the probability of creating a successful 3D printed model.
Case Studies and Applications
Case studies and applications are crucial in understanding the practical implications of 3D printer designs. They offer a tangible representation of theoretical concepts, bridging the gap between design and real-world usage. By examining specific instances where 3D printing has been effectively utilized, we can discern best practices, common pitfalls, and innovative solutions. This exploration not only enhances comprehension but also inspires creativity and informed decision-making among designers.
Industry Use Cases
In various industries, 3D printing technology has redefined traditional processes. Manufacturers, in particular, have harnessed this technology for rapid prototyping and custom parts production, thus minimizing costs and lead times.
- Aerospace: Companies like Boeing utilize 3D printing for lightweight components, which contribute to fuel efficiency and reduced emissions.
- Healthcare: Medical devices tailored to individual patients, such as prosthetics or surgical instruments, demonstrate how personalized solutions enhance care.
- Automotive: Ford, for instance, employs 3D printing for producing prototype parts quickly, allowing for faster design iterations.
These examples illustrate the vast potential of 3D printing across sectors. The adaptability and efficiency of 3D designs create competitive advantage while fulfilling specific industry requirements.
"3D printing signifies not only a technological advance but also a paradigm shift in product development and manufacturing processes."
Artistic and Creative Applications
Beyond industry, 3D printing has also made significant inroads into the arts and creative fields. Artists and designers leverage 3D printing technology to explore new forms and mediums, creating unique pieces that may be challenging to produce via traditional methods.
- Sculpture: Artists can fabricate intricate sculptures that would be difficult or impossible to mold or carve.
- Fashion: Designers such as Iris van Herpen incorporate 3D printed elements into fashion, resulting in innovative and avant-garde collections.
- Architecture: 3D printing allows architects to create complex models that accurately detail their visions for projects, improving client presentations and understanding.
These artistic applications reveal how 3D printing technology transforms the creative landscape. It empowers creators to push boundaries, experiment freely, and realize their visions, thus fostering a new level of expression and originality.
Future Trends in 3D Design and Printing
The realm of 3D printing is undergoing significant transformation, shaped by rapid advancements in technology and design methodologies. Understanding these future trends is essential for professionals and enthusiasts alike. Knowing where the industry is headed can help individuals adapt their skills and designs to meet evolving standards and consumer demands. Notably, this section focuses on innovations in design software and advancements in printing technology, underscoring their relevance in effectively navigating the future of 3D design.
Innovations in Design Software
The development of design software has been pivotal in expanding the horizons of 3D printing. As software solutions become more sophisticated, they integrate features that enhance user experience and design capabilities. Innovations to note include:
- Cloud-Based Platforms: These allow for collaboration among users, making it easier to share ideas and prototypes without geographical restrictions.
- AI-Assisted Design Tools: Artificial intelligence streamlines the design process, helping users make informed decisions based on data analytics and existing designs.
- User-Friendly Interfaces: An emphasis on accessibility is seen in software like TinkerCAD and Fusion 360, which cater to both beginners and experts.
Such innovations not only foster creativity but also enhance efficiency. With improved tools, designers can iterate faster, test different concepts, and refine their work with precision. This shift will likely lead to higher quality outputs and open new avenues for creative expression.
Advancements in Printing Technology
As important as design software is, the role of printing technology cannot be underestimated. Developments in this area have direct implications on the types of designs that can be produced. Key advancements include:
- Multi-Material Printing: This allows for the creation of objects using different materials, thus offering greater versatility in design.
- Higher Resolution Printing: Advances in printing processes lead to finer details, making it possible to create intricate designs that were previously unattainable.
- More Sustainable Materials: The focus on eco-friendly options is growing, leading to increased use of biodegradable filaments and recycled materials in the printing process.
These technologies not only enhance design possibilities but also contribute to sustainability in the industry. Recognizing the impact of these changes allows designers to prepare for shifts in consumer preferences and regulatory demands.
The future of 3D design and printing promises exciting possibilities, driven by continuous innovation and evolving technologies.
Ending
Summary of Key Points
- Understanding 3D Printing: Comprehending the principles of 3D printing technology is fundamental to effective design.
- Design Principles: The article highlighted various design principles that guide how models should be conceptualized and executed.
- Software Tools: A range of software tools were introduced, offering tailored solutions for both beginners and advanced users.
- Types of Designs: Discussed functional, aesthetic, and customizable designs, providing insight on how they meet different requirements.
- Material Selection: An understanding of different materials and their implications is essential for successful printing outcomes.
- Challenges: Addressing common challenges fosters better preparedness when creating designs.
- Best Practices: Emphasized efficient design processes and the importance of feedback.
- Case Studies: Real-world applications illustrate design versatility.
- Future Trends: Innovations and advancements in the field point towards exciting possibilities for design and printing.
Final Thoughts on Design Creation
Ultimately, the journey of creating 3D printer designs is multifaceted and rewarding. By applying the detailed guidelines discussed, individuals can not only enhance their understanding but also improve their skills in tangible ways. As technology advances, staying informed and adaptable will be vital in the ever-evolving landscape of 3D printing. Embracing this mindset can lead to groundbreaking designs and impactful creations that push the boundaries of what is currently imaginable in the world of 3D printing.