Digital Soldering Iron Station: Insights and Features
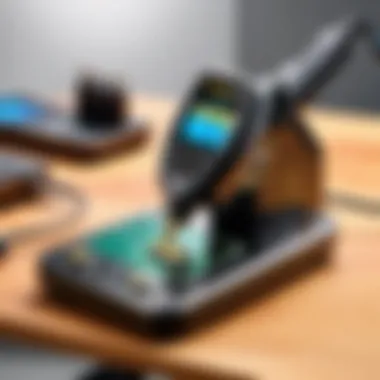
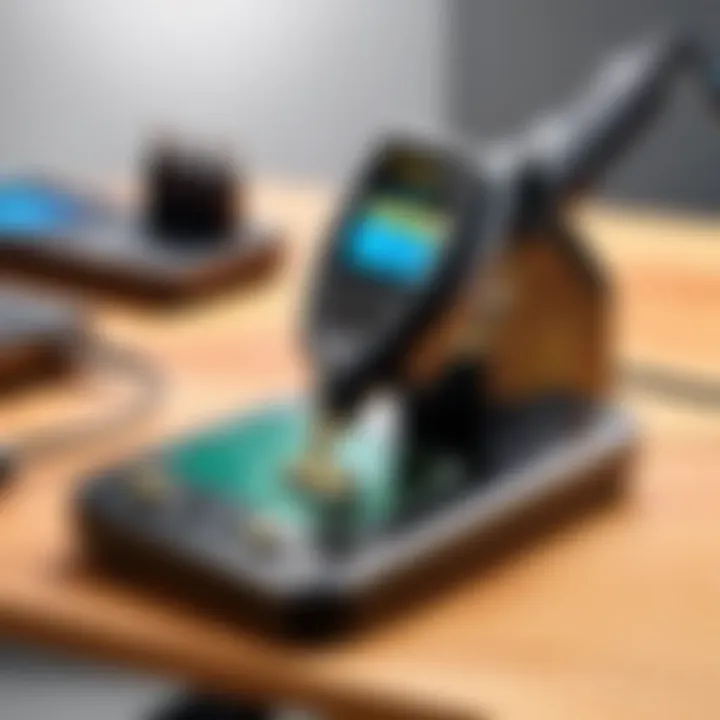
Intro
Digital soldering iron stations have carved a niche in the toolkit of hobbyists and professionals alike, becoming indispensable in numerous fields including electronics, robotics, and DIY repair projects. These stations do more than just heat metal; they provide precision, control, and technology that transform the soldering process. As we navigate through this detailed overview, we'll unpack the nuances of these devices, exploring how they tick, what makes them tick, and why they are critical in today's tech-heavy world.
Let’s face it, soldering might seem straightforward on the surface, but having the right tools can make all the difference between a botched job and a flawless connection. Knowing the ins and outs of digital soldering iron stations can elevate your work, ensure longevity in projects, and ultimately save both time and resources.
In this article, we’ll explore:
- Product Overview: Examining brands, specifications, and pricing to help you make an informed choice.
- Performance Comparison: Conducting benchmark tests to highlight speed and efficiency.
- Features and Technology: Discussing unique features and advancements that set these stations apart.
- Pros and Cons: Laying out the strengths and weaknesses of digital soldering irons.
- Value for Money: Analyzing cost-effectiveness and potential long-term benefits.
Through this comprehensive exploration, you'll gain a solid grasp on digital soldering iron stations and feel empowered to select the right one for your needs.
Prelude to Digital Soldering Stations
In today’s fast-paced tech-centric environment, understanding digital soldering stations is paramount for professionals in electronics, gaming, and IT sectors. These tools are not just for the hobbyist; they are vital instruments for precision work, creating and repairing electronics effectively. A digital soldering iron station distinguishes itself from its analog counterparts through superior temperature control and versatility, making it indispensable for various applications.
Definition and Overview
A digital soldering station comprises several key components, including a soldering iron, a power supply, and a control unit, often featuring a digital display to read and set temperatures accurately. This setup allows users to achieve consistent heating, greatly reducing the risk of damage to both components and the operator. The adjustable temperature settings ensure that soldering can be performed on different materials without unnecessary fuss. Unlike basic soldering tools, digital stations come equipped with advanced features like programmable temperature settings and sleep modes that enhance efficiency and safety.
"Having the right tools can mean the difference between success and failure in electronics work; a digital soldering station is a key to precision."
History and Evolution
The evolution of soldering stations reflects technological advancements in the electronics industry. The earliest soldering tools often lacked the ability to control temperature, leading to inconsistent results and potentially damaging sensitive components. Until the introduction of digitalization in soldering, most setups were rudimentary. Older models required constant monitoring and adjustment, which was prone to human error.
With the advent of microcontroller technology in the mid-20th century, digital soldering iron stations began to take shape. Learning from historical practices, manufacturers started integrating features that allowed for more accurate temperature management. Initially seen as luxury items, they have become accessible and standard in both professional and hobbyist environments. This transition signifies not just improvements in efficiency but also the growth of safety standards in electronics soldering practices.
Today, many soldering stations boast a range of features, including programmable profiles, advanced heating elements, and the ability to switch between different soldering tips seamlessly. This growth illustrates a commitment to enhancing usability while addressing the intricate needs of modern electronics applications.
Components of a Digital Soldering Station
When assessing a digital soldering station, it’s critical to understand the various components that make it function effectively. Each part plays a unique role in ensuring that the soldering process is not only efficient but also precise. Below, we'll explore the core components, detailing their significance and how they contribute to the overall performance of the soldering station.
Soldering Iron
At the heart of any soldering station is the soldering iron itself. This tool is not just the wand that melts and applies solder, but a vital instrument that requires careful selection. The soldering iron's tip material, size, and shape dramatically affect its performance. For instance, a finer tip can be beneficial for detailed work on miniature components, while a broader tip may be suited for larger electronic connections. Moreover, the power rating of the iron, typically measured in watts, is fundamental as it determines the heating capability. More power allows quicker heating and recovery times, making for smoother transitions between soldering tasks.
Selecting the right soldering iron can greatly improve work quality; having a reliable and adjustable temperature range enhances control and precision, ultimately leading to better solder joints.
Power Supply Unit
The power supply unit (PSU) is another cornerstone of digital soldering stations. This component feeds power to the soldering iron and, crucially, must provide a steady and reliable current. Most modern stations utilize compact switching power supplies that adjust voltage and current based on the iron's demands. This adaptability not only extends the life of the equipment but also ensures that the work is done consistently and efficiently.
A good PSU will come with safety features like over-temperature protection and short-circuit protection, which safeguard both the user and the equipment from potential damage. Having a quality PSU can be the difference between smooth sailing and frustrating setbacks in your work.
Control Interface
Next in our line-up is the control interface, which operates as the bridge between the user and the soldering station. This might be in the form of dials, switches, or even a digital touchscreen interface. The interface tends to vary between models, with some being very basic and others offering advanced features, including programmable settings for different soldering tasks.
A well-designed control interface grants you ease of access to adjust the temperature and other settings quickly. Some advanced stations even allow for temperature profiles, where a user can save specific temperature settings for specific tasks. Such functionality can be especially useful in environments where multiple technicians are using the same unit, ensuring that everyone can work to their preferences seamlessly.
Temperature Sensor and Calibration
Last but certainly not least is the temperature sensor, a crucial component for maintaining precision during soldering. The temperature sensor monitors the tip's heat, providing feedback to the control unit to maintain the desired temperature.
Moreover, calibration is a significant process, ensuring that the temperature displayed on your soldering station matches what is actually occurring at the tip. A mismatch can lead to poor solder joints or even damage to sensitive components. Therefore, regular calibration is essential to uphold accuracy.
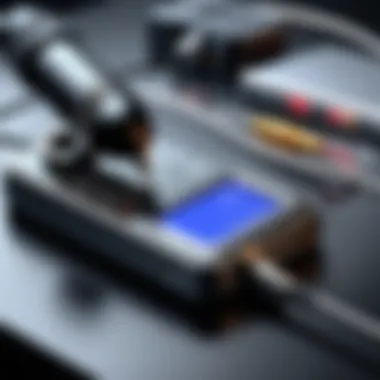
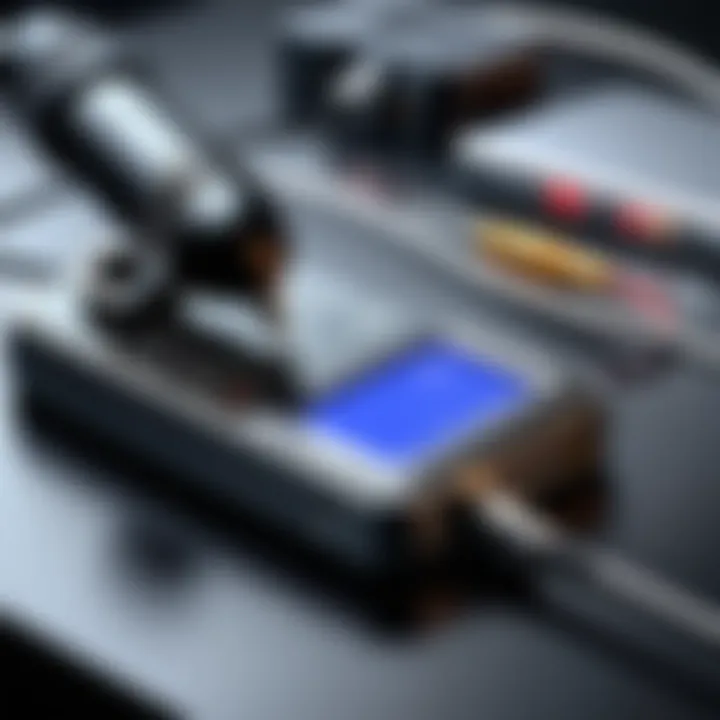
Providing a precise temperature control, calibrating options allows for a range of soldering applications—from delicate electronic devices to larger scale tasks. Regular monitoring and calibration can make your soldering job far more efficient and effective, decreasing frustration and increasing the quality of work.
"A quality soldering station is like a fine-tuned instrument; it requires the right components, maintained with care, to achieve the best sound— or in this case, the best solder joints."
Understanding these core components not only helps in choosing the right digital soldering iron station but also enhances your soldering skills, making each project less daunting and more rewarding.
Benefits of Using Digital Soldering Stations
Digital soldering stations have become a favorite among electronics hobbyists and professionals alike. Their rise in popularity can be attributed to a number of compelling benefits that enhance the soldering experience. In this section, we will explore the significant advantages that digital soldering stations offer compared to their analog counterparts, making a strong case for their use in various projects.
Precision and Control
One of the standout characteristics of digital soldering stations is their ability to deliver precision and control that is hard to match in traditional analog models. With a digital interface, users can set specific temperature levels to the exact degree. This feature is crucial in soldering delicate components where overheating can lead to irreversible damage. For instance, if you're working on a circuit board for a high-speed graphics card, adjusting the temperature with pinpoint accuracy becomes essential.
Moreover, many models come equipped with temperature stability indicators, which ensures that the desired temperature is maintained throughout the soldering process. This minimizes the risk of thermal shock to sensitive components and enhances the overall quality of the solder joint.
Safety and Reliability
Safety is a paramount concern when dealing with soldering tools. Digital soldering stations are designed with advanced safety features that increase their reliability. Many units come with auto-shutoff capabilities, meaning they can power down after a set period of inactivity. This not only conserves energy but also greatly reduces the risk of accidental burns or fires.
In addition, the digital display often provides clear readings of the current temperature, allowing users to gauge their working environment effectively. This sense of control gives peace of mind, particularly for those new to soldering or those working in shared spaces such as workshops or maker spaces.
"When safety features are combined with precise controls, the user experience is not only improved; it also turns soldering into a craft rather than just a task."
Versatility for Different Applications
Another great benefit of digital soldering stations is their adaptability across a variety of applications. Whether you are repairing old circuit boards, creating intricate DIY electronics projects, or even engaging in fine-scale production runs, these stations can handle a wide range of soldering tasks. The programmable features allow users to save specific temperature profiles for different types of solder and components.
This flexibility is crucial for tech enthusiasts and professionals who often switch between tasks that require diverse soldering techniques. For example, switching from a high-temperature setting for heavy-duty soldering to a mild setting for more delicate electronics can be done with just a few button presses, minimizing downtime in projects.
In summary, the integration of precision, safety, and versatility makes digital soldering stations an essential tool for anyone serious about soldering tasks, from professionals to hobbyists. By investing in a quality digital station, users can elevate their skills and outcomes in the world of electronic assembly and repair.
Choosing the Right Digital Soldering Iron Station
Selecting the correct digital soldering iron station is crucial for both hobbyists and professionals alike. For those engaged in electronics repair, DIY projects, or intricate circuit board work, the right tool can make the difference between a successful solder joint and a frustrating experience. This section will help you navigate the often overwhelming sea of options available in the market, ensuring that you make an informed choice tailored to your specific needs.
Assessing Your Needs
Before you make any decisions, it's vital to evaluate what you actually need from a digital soldering station. Consider the following:
- Project Type: Are you working on delicate components or larger assemblies? Tasks can vary greatly in difficulty and precision requirements.
- Frequency of Use: If you solder frequently, investing in a high-end unit may be justified. Conversely, a less costly option might suffice for occasional use.
- Skill Level: Beginners might benefit from a station with simpler controls, while experienced users may seek advanced features.
"Knowing what you'll be working on helps you to choose the right tool for the job. Or else, it’s like trying to cut a steak with a butter knife."
Key Specifications to Consider
Having assessed your needs, it's time to turn your attention to the specifications that truly matter when choosing a digital soldering iron station. Here are essential elements to keep in mind:
- Temperature Range: A good range typically spans from around 200°C to 480°C. Different materials have different melting points, so flexibility in temperature control is important.
- Wattage: The wattage of the soldering iron affects heat recovery time. A 60W station can heat up more quickly, which saves time during lengthy projects.
- Digital Display: Look for a clear, easy-to-read digital interface. It should provide precise temperature readings and possibly even allow for setting memories.
- Interchangeable Tips: Having various tip options is beneficial for different applications, from fine soldering to broader connections.
- Safety Features: Over-heat protection and automatic shut-off features can prevent mishaps, especially in a busy workshop environment.
Brand and Model Comparisons
With many respected brands on the market, choosing the right one can be tricky. It's wise to do some brand comparison before making a decision. Factors to weigh include:
- Reputation and Reliability: Brands like Weller, Hakko, and Metcal have established themselves as industry leaders, renowned for their durability and performance.
- Customer Reviews: Look at user experiences—what do other hobbyists and professionals say? Platforms like Reddit often have discussions that can help clarify common concerns or praises.
- Warranty and Support: A reliable warranty and good customer support can save you a lot of headaches down the line, should issues arise.
- Price vs. Performance: More expensive models often come with advanced features, but it’s essential to avoid overpaying for things you may not need. Find a balance that offers both quality and value.
By carefully thinking through your needs, understanding key specifications, and comparing brands and models, you'll be better positioned to select a digital soldering iron station that meets your requirements. This decision can enhance your soldering experience and contribute significantly to the quality of your work.
User Considerations and Practical Application
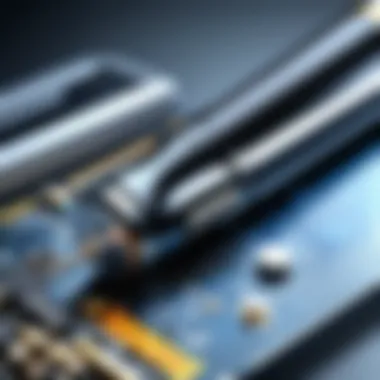
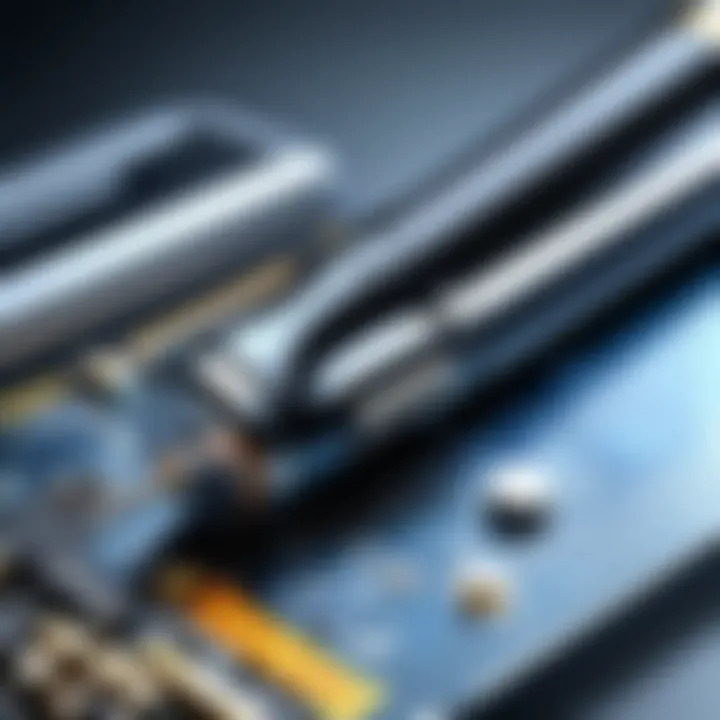
When it comes to digital soldering iron stations, user considerations are crucial for anyone looking to achieve successful, high-quality results in their projects. This section serves not just as a guideline but also emphasizes the significance of understanding how different aspects of the soldering process can impact overall performance and satisfaction. The users’ skill level, project requirements, and equipment familiarity play a significant role in the effectiveness of any soldering endeavor.
Best Practices for Usage
To get the most out of a digital soldering station, following best practices is key. Here are some essential tips:
- Read the Manual: Taking the time to familiarize yourself with the user manual may seem tedious, but understanding the specific features and settings of your device is essential. Every model has its unique quirks.
- Temperature Calibration: Before diving into a project, it’s wise to calibrate the temperature settings. Using a thermometer to check the tool’s temperature can ensure you’re soldering at the right heat, reducing the risk of damage to sensitive components.
- Use the Right Tip: Utilizing the appropriate soldering tip can make a world of difference. For fine work, a smaller tip will offer precision, while a broader one is better suited for larger connections.
- Regular Cleaning: A clean soldering tip will conduct heat more effectively. It’s a good habit to keep the tip clean by periodically wiping it on a wet sponge or brass pad. This prevents oxidation buildup.
- Practice Patience: Rushing can lead to mistakes. Allow the solder to flow naturally, and avoid pushing it too hastily. Remember, you’re not in a race, and taking your time can yield the most satisfying results.
Implementing these strategies will not only enhance the quality of your soldering but also extend the life of your equipment.
"A stitch in time saves nine"—taking care of your tools and process now pays off in the long run!
Common Mistakes to Avoid
There are several pitfalls one might encounter when using a digital soldering iron station. Recognizing these can help you sidestep unnecessary frustrations:
- Overheating Components: It’s easy to get carried away with heat. Remember that excess heat can damage the components you're working on. Always choose the lowest temperature suitable for your application.
- Neglecting Safety: Soldering involves the use of hot tools and potentially harmful materials. Wearing safety goggles and working in a well-ventilated area should never be overlooked.
- Using Low-Quality Materials: Opting for cheap solder can result in poor connections. Always choose high-quality solder that meets the standards required for your project.
- Ignoring the Environment: While soldering, make sure your workspace is organized. A cluttered surface increases the chance of accidents. Keep your tools in order, and ensure not to leave hot tools unattended.
- Lack of Testing: Skipping the initial connection testing can lead to larger issues down the line. It’s vital to verify connections with a multimeter after soldering to ensure everything’s functioning as it should.
Temperature Management in Soldering
The significance of managing temperature during soldering cannot be overstated. Precise temperature control ensures the success of delicate soldering tasks. Whether you're working on intricate circuit boards or assembling electronic devices, understanding temperature management is key to achieving reliable and durable connections.
When soldering, if the temperature is too low, the solder may not flow properly, leading to weak joints that easily fail over time. On the flip side, excessive heat can damage components, causing irreversible harm. In essence, a balanced approach to temperature is paramount for effective soldering.
Importance of Temperature Control
Temperature control serves multiple purposes. First and foremost, it safeguards the integrity of both the components and the joints. For instance, sensitive parts like capacitors and ICs can be particularly vulnerable to heat. Even a moment of excessive warmth could fry the delicate connections within. Proper temperature management not only protects these components but also ensures the solder flows into the joint effectively, creating a strong physical bond.
Secondly, optimal temperature settings can enhance the aesthetics of the solder joints. Smooth, shiny solder joints are often criteria for professional work, as opposed to dull, brittle, or overly burned appearances.
"Good soldering requires not just skill, but the right balance of heat – too little and it’s weak, too much and it’s ruined.”
Adjusting Temperature Settings
Most digital soldering stations come with built-in controls for adjusting temperature settings. A standard practice in this process is to begin with a temperature that fits the base materials. For soldering, this often hovers around 350–400 degrees Celsius, depending on the type of solder used. However, it’s crucial to remember that every job has nuances.
- Know Your Solder: Different solders have different melting points. Lead-based solder typically melts around 183 degrees Celsius, whereas lead-free solders may need higher temperatures, sometimes reaching up to 220 degrees Celsius.
- Assess Component Specifications: Always check the specifications of the components you’re using. You don’t want to inadvertently overheat a sensitive piece. Manufacturers usually provide guidance on recommended soldering temperatures.
- Experimentation: It can be beneficial to test temperate settings on a scrap piece before diving into the main project. This will give you a feel for practical outcomes based on your station's capabilities.
- Adjust for Heat Dissipation: Remember that components can dissipate heat at different rates. Adjust your temperature settings according to the environment and the materials in play.
Maintenance and Care
Taking care of a digital soldering iron station is crucial for maintaining its performance and ensuring long-term usability. Just like a car needs routine oil changes to run smoothly, your digital soldering station deserves regular attention to keep it in top working order. Neglecting maintenance can result in decreased precision, faulty solder joints, or even hazards like overheating. Proper care not only extends the longevity of your tools but also improves the quality of your work, ultimately saving you time and frustration during projects.
Another critical aspect is that proper maintenance can prevent expensive repairs down the line. Regular care allows users to identify minor issues before they escalate, which can drastically reduce costs and downtime. Whether you are a seasoned professional or a hobbyist, establishing a maintenance routine tailored to your specific needs can make all the difference in your soldering experience.
Regular Maintenance Tips
Regular upkeep involves a mix of cleaning, inspection, and minor adjustments. Here are some essential tips that will help keep your digital soldering station performing well:
- Clean the Tip: After each use, make it a habit to clean the soldering iron’s tip. A dirty tip can cause poor heat transfer and affect your soldering quality. Use a damp sponge or brass wool to wipe off residue.
- Check Temperature Calibration: Periodically verify that the temperature settings align with actual temperatures. This ensures accuracy, which is essential in electronics work.
- Inspect Cables and Connections: Regularly examine the power cables and connections for wear and tear. Any frayed wires could lead to shorts or inconsistent heating.
- Secure Storage: When you’re done, place the soldering iron back in its stand to prevent damage to the tip. This also minimizes safety hazards, preventing accidental burns or contact with flammable materials.
- Replace Worn Components: If you notice that the tip is getting excessively worn out, replace it. A worn tip can be a source of unreliable solder connections and possible disappointments during advanced projects.
Following these basic maintenance steps can go a long way in ensuring that your soldering iron remains in excellent shape for years.
Troubleshooting Common Issues
Despite your best efforts in maintaining your digital soldering iron station, issues may still arise. Here’s a guide to some common problems you might encounter and how to address them:
- Temperature Fluctuations: If you experience inconsistent temperatures, check the calibration first. If recalibrating doesn’t help, the temperature sensor may be faulty and need checking or replacement.
- Poor Solder Joints: If your solder joints are weak or cold, consider cleaning the tip. Also, ensure you are using solder appropriate for your work. Different materials require different solder compositions.
- Power Supply Problems: If the soldering iron doesn’t heat up, inspect the power supply unit. Make sure it's properly plugged in and delivering the correct voltage. If this doesn’t resolve the issue, the power supply may need repair or replacement.
- Overheating: If your station becomes too hot, turn it off immediately to cool down. Often, overheating can be a sign of a malfunctioning thermostat or other internal components.
"Routine checks and repairs can save both time and money in the long run, so don’t overlook those small tasks."
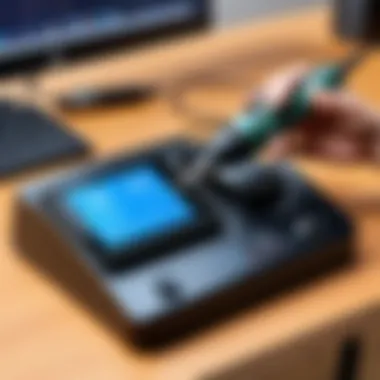
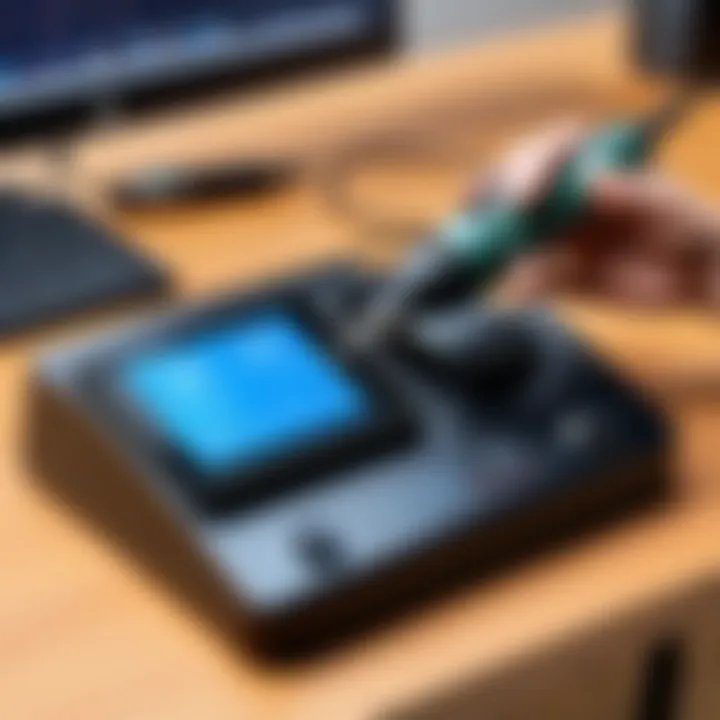
By addressing these potential problems swiftly and effectively, you’ll not only increase the lifespan of your station but also prevent them from ruining an otherwise successful project. Getting familiar with the common issues can also enhance your confidence when you’re working on intricate tasks.
Comparative Analysis of Analog vs Digital Soldering Stations
In the realm of soldering, the choice between analog and digital soldering stations can be a make-or-break decision for many tech enthusiasts or professionals. Understanding the nuances of both types is essential. Each has its own strengths and weaknesses, making it crucial to match the needs of your application with the appropriate tool.
Basic Differences Explained
Analog soldering stations are, for the most part, quite straightforward. They rely on traditional rheostats or simple settings to control temperature. It's like driving an old pickup truck - there’s a charm in its simplicity, but it might not give you the most precise performance. This method, while reliable, can lead to fluctuations in temperature, often requiring the user to pay close attention to the heat levels. For example, if you’re working on a circuit board with delicate components, the risk of overheating can lead to catastrophic failures.
On the other hand, digital soldering stations utilize microprocessors and screens to provide real-time temperature readouts and exact control. Imagine driving a hybrid car that provides your fuel usage stats as you go - it’s a way better approach for efficiency. Given their programmable features, these tools can offer higher precision, allowing for a consistent and stable performance ideal for intricate electronic tasks.
In terms of usability, digital stations often come equipped with various presets for specific tasks, while analog versions usually just allow for a manual adjustment of the heat level. For the user who seeks efficiency and versatility, the added functionalities of a digital station can make a noticeable difference—especially in professional settings or skilled DIY projects.
When to Choose Digital Over Analog
Choosing digital over analog is often a matter of project requirements, budget, and user experience. If precision is paramount, like when soldering tiny components on a circuit board, a digital station is your best friend.
Considerations include:
- Specific Projects: For complex electronics, the accuracy of a digital soldering station can save you time and reduce errors.
- User Skill Level: If you’re less experienced with soldering, digital stations are usually easier to handle, thanks to their intuitive interfaces.
- Heat Sensitivity: Many types of electronic components are sensitive to heat, and a digital station will help regulate temperatures better than its analog counterpart.
- Warranty and Support: Typically, digital stations come with better customer service and warranties, recognizing their often higher price point.
When adapting to new technology, it’s essential to weigh the benefits against your needs. Digital soldering stations present solid advantages that cater to precision and efficiency.
Each choice, analog or digital, has its place, but understanding their unique characteristics can guide users toward making informed decisions that best align with their hobbyist or professional practices.
Future of Digital Soldering Technology
As with any field tied to technology, the future of digital soldering stations is a topic that's steeped in anticipation and evolving expectations. This sector continues to develop new trends and innovations that promise to enhance user efficiency, effectiveness, and overall experience. As the demand for intricate soldering tasks grows across various domains—like electronics manufacturing, gaming, and DIY projects—it's vital to take a closer look at what lies ahead in the world of soldering technology.
Trends and Innovations
One major trend is the integration of smart technology into digital soldering stations. This means newer stations are equipped with advanced sensors that provide real-time feedback on temperature and tip condition. Moreover, we are witnessing the rise of app connectivity. Some digital soldering stations now enable users to connect with their smartphones to customize settings and access tutorials. Such features make soldering not just a task but an educational experience.
Another notable innovation is energy efficiency. Modern soldering tools are being designed to consume less power without sacrificing performance. This trend not only benefits the environment but also reduces electricity bills for users who perform extensive soldering work. Additionally, it's not uncommon to find soldering stations that have features like auto shut-off to enhance safety and conserve energy.
Technological advancements have also paved the way for multifunctional soldering stations. Some devices can now handle a variety of tasks beyond soldering, such as desoldering, hot air rework, and even 3D printing components. This shift towards multifunctionality appeals broadly to tech enthusiasts who desire a single tool for multiple applications.
"The future of digital soldering stations is moving toward enhanced precision and user engagement, which can revolutionize the way we think about soldering tasks."
Potential Developments in Design
The design of digital soldering stations is evolving, not just in terms of functionality but also in user interface. An interesting future direction will likely involve ergonomics. With prolonged use often leading to strain, there's an increasing focus on making devices more comfortable for extended operation. Adjustable stands and lighter iron models are just the start. Manufacturers are likely to invest more heavily in how users physically interact with their devices.
Moreover, modularity in design is expected to gain traction. For a long time, soldering stations were relatively straightforward in terms of user options. However, there’s a shift toward customizable setups that allow users to swap out tips, power supplies, and even interfaces. Such modularity empowers the user to tailor their soldering station for specific tasks, which could widen the scope of applications in the hobbyist and professional realms.
Finally, the ongoing shift towards sustainability is likely to affect design considerations. Consumers are increasingly aware of the environmental impact of their devices, pushing manufacturers to adopt greener materials and practices in production. This not only ensures compliance with regulatory standards but enhances brand loyalty among eco-conscious users.
In summary, the future of digital soldering technology appears bright and promising. These advancements will aim to enhance user-friendliness while also addressing efficiency and environmental concerns. As we look ahead, it's clear that digital soldering stations will continue to evolve, promoting innovation across diverse applications.
Closure
Wrapping up our exploration of digital soldering iron stations, it’s essential to reflect on their impact in both professional and hobbyist realms. The significance of this topic is immense, as these tools play a pivotal role in electronics manufacturing, repairs, and DIY projects. They offer precision that can make or break delicate components, ensuring that the art of soldering isn't just a matter of heat and metal, but understanding the nuances of temperature control and technique.
Summary of Key Points
- Precision and Control: Digital soldering stations provide a level of accuracy that analog counterparts struggle to achieve. This precision leads to better connections and overall product quality.
- Safety Features: Many models are equipped with safety features, such as automatic shut-off functions and temperature regulation, reducing the likelihood of accidents.
- Versatility: These stations are adaptable for various applications, whether it’s working on intricate circuit boards or larger electronic appliances, making them invaluable in any toolkit.
- Maintenance Importance: Proper upkeep of these stations ensures longevity and consistent performance, saving time and money in replacements or repairs.
"The importance of selecting a suitable soldering station cannot be overstated; it’s the bridge between a good project and a great one."
Final Thoughts on Selection and Use
When it comes to choosing a digital soldering iron station, one must consider various factors. Knowing your specific needs—be it for hobby projects or professional use—will guide your decision. Brand reputation, customer feedback, and features such as adjustable temperatures and ease of use are pivotal.
Moreover, understanding the way you work will significantly affect your choice. If you’re frequently on the go, a portable unit with a quick heat-up time might be ideal. On the other hand, if you are working in a steady location, consider a more robust unit with advanced controls.