Generative Design and 3D Printing: Trends & Futures
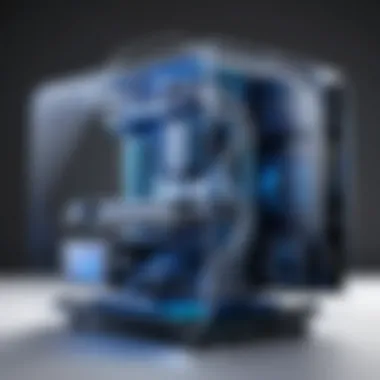
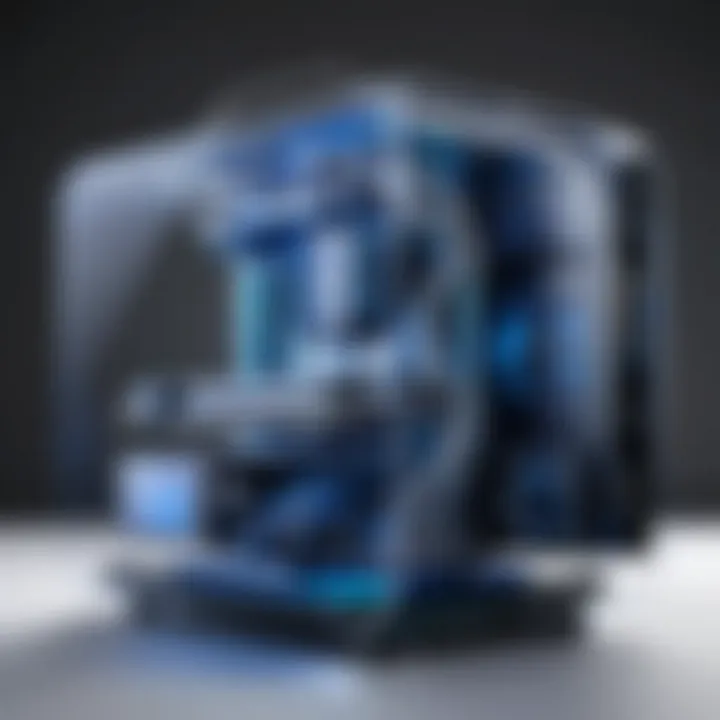
Intro
The rapidly changing landscape of technology has ushered in novel approaches to design and manufacturing. Generative design, in conjunction with 3D printing, is creating a shift in how we perceive and execute the production process. This combination leverages advanced algorithms and artificial intelligence to create optimized designs, leading to significant benefits for various industries ranging from automotive to healthcare. Understanding their interaction and applications is imperative for tech enthusiasts, gamers, and IT professionals who are keen on staying updated with the forefront of innovation.
In this exploration, we outline the core principles of generative design, analyze its integration with 3D printing, and discuss implications for diverse fields. We will dissect advantages and challenges while looking towards future possibilities. By emphasizing analytical perspectives and the role AI plays, this article offers in-depth insights into these transformative technologies.
Product Overview
When examining the role of generative design in 3D printing, it is essential first to oversee the products involved. The most recognized brands contributing to this sector are Autodesk, Siemens, and Altair. Each has made substantial strides in developing tools that dwarf traditional methods regarding design efficiency and adaptability.
- Brand Information:
Autodesk is prominently using its Fusion 360 for generative design, allowing creators to input parameters and constraints seamlessly. Siemens integrates generative design in its NX package for more extensive industrial applications. Altair is committed to making complex problem-solving accessible through its Inspire platform focused on achieving superior model performance. - Key Specifications:
Each software features specific performance and compatibility specifications such as high computational efficiency, user-friendly interfaces, and extensive material libraries tailored for various printing technologies. - Pricing:
Pricing structures vary largely depending on features offered; Autodesk Fusion 360 follows a subscription model that generally starts at around $495 annually. Siemens and Altair offer several tiered pricing options, reflecting the flexibility and scale of their applications.
Performance Comparison
Generative design implementations are often evaluated on performance metrics, particularly efficiency and speed in different benchmarks. For instance, tests comparing models designed through traditional means against those produced with generative design show substantial performance differentials in material utilization and timeline efficiencies. Benchmarks illustrate a marked decrease in production cycles for generative models, showcasing the affordances that AI brings into the fray.
- Benchmark Tests:
Analysis by industry leaders have indicated that parts produced via generative design could show up to 30% lesser material requirements, reflecting noteworthy gains in sustainability as well. - Speed and Efficiency Comparisons:
Users report that through streamlined production methods and shortening iteration cycles, time-to-market can improve by as much as 50% depending on design complexity and printing capabilities.
Features and Technology
As generative design dives deeper into 3D printing processes, unique features make it increasingly essential in this technological crossroads.
- Unique Features:
Generative design excels in creating hundreds or thousands of design solutions and ranking them per user-set criteria, enabling them to focus on key metrics like strength and weight. - Technological Advancements:
Integration with AI enhances the capabilities of traditional CAD software tremendously. Real-time feedback adjustments can lead designers to suitable solutions far quicker than by manual methods. - Compatibility With Other Devices:
Flexibility in material choices, alongside printing processes, solidifies operations across various types of printers—such as Fused Deposition Modeling (FDM) and Selective Laser Sintering (SLS)—increases generative design outreach.
Pros and Cons
Despite its transformative nature, generative design coupled with 3D printing is not without scrutiny.
- Strengths of the Product:
- Areas for Improvement:
- Efficient material use maximizes resources while minimizing waste.
- Accelerates design iterations well beyond conventional approaches.
- Offers abundant customizability in production
- Costs tied to advanced software can be prohibitive for smaller operations.
- Learning curve associated with sophisticated tools may discourage practical application initially.
Value for Money
The financial aspect of generative design in producing components through 3D printing is multifaceted.
- Cost-Effectiveness:
While upfront software and equipment costs may seem deferential, long-term savings emerge through waste reduction and enhanced productivity. - Long-Term Benefits:
Companies often witness a boost in performance and rapid turnaround leading to increased profitability as operations scale. - Comparison With Similar Products:
When contrasted with traditional design methods or simpler CAD tools, the generative design wave emerges dominant, especially for organizations emphasizing reduce environmental footprint amidst global financial pressures.
Embracing generative design in 3D printing spells a paradigm shift—shaping a future marked by unprecedented productivity and sustainability checks in valid synergy.
Foreword to Generative Design
Generative design is a powerful concept that is reshaping the way products are designed and manufactured. This method emphasizes the collaboration between design tools and natural forms, which allows for innovation that can produce efficiencies and solve problems that may have not been considered previously. In the context of 3D printing, generative design serves as a catalyst for enhancing capabilities in every industry.
It is important to understand that generative design is more than just a trend; it fundamentally changes design thinking. The application of this approach can lead to light-weight structures as well as topologically optimized components that might be too complex or impossible to create using traditional methods of manufacturing.
Further emphasizing the benefits of generative design in 3D printing include:
- Improved Design Outcomes: Generative design leverages algorithms to evaluate thousands of design permutations quickly. This leads to discovering options that a human designer often misses.
- Increased Material Efficiency: By quantifying costs associated with different materials, generative design reduces waste, ultimately positively affecting environmental sustainability.
- Faster Prototyping Cycles: Agile iterations through automated simulations streamline the prototyping phase.
Delving deeper into this topic requires studying its definitions and historical relevance to understand how it came to be a necessity in modern design.
Defining Generative Design
Generative design refers to a design exploration process in which algorithms are used to generate a body of design alternatives from a set of input parameters. These parameters can range from specific constraints like material properties and budget to desired performance specifications. Various solutions emerge, helping designers to find optimal configurations for their challenges without a prolonged manual investigation.
Genertive design operates through a feedback system where the output is further refined based on performance data. Essentially, computers become the designers' assistants, venturing into imagined solutions that push beyond traditional limitations. A stable relationship stands at the crossroads where designers and machines help one another.
This is critically important when considering the unique capabilities generative design provides:
- Unique and custom configurations based on desired physical properties
- Better exploration of performance and structural integrity through simulations
- Repurposing of designs refined over time instead of every iteration being a fresh start
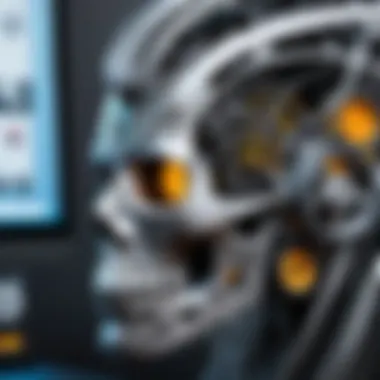
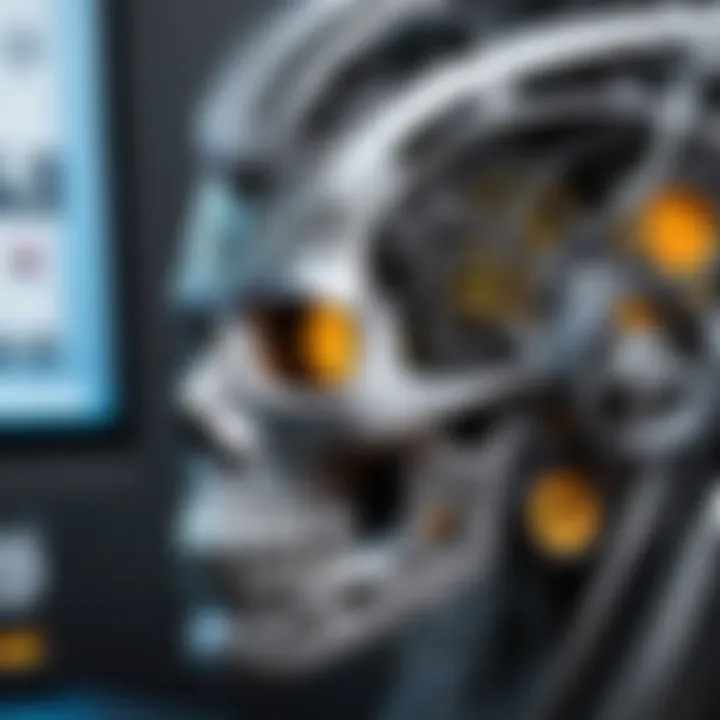
Historical Context and Evolution
Generative design is not a new concept but originated in the mid-to-late 20th century. The roots lay within computer-aided design and constrained optimization techniques, where numerous iterations were explored to ne feedback loop.
Historically, generative design was not readily attached to 3D printing; instead, it thrived in strictly computer-aided environments where optional feedback and constraints took shape. The shift began in the late 2000s with advances in computing power and cemented with the rise of 3D printing technologies, which allowed innovative designs digitally conceived to be fabricated physically.
The evolution checks several identifying points, including:
- The rise of parametric technologies influencing design rulesets.
- As 3D printing technologies began permeating wider industries, it prodded exploration within the generative design methodology.
- Foray into niche industries leading to successful applications across automotive, aerospace, and medical associated projects.
The powerful convergence of generative design with 3D printing marks a remarkable path forward. Teams participating in these processes gain not only advanced prototypes but tools for thinking differently in product lifecycle management.
Understanding generative design provides the groundwork for its intersection with 3D printing technology, and prepares us to explore these trends further. Starting specifically with the underpinnings of 3D printing technology, one can appreciate how both schools benefit exponentially by merging.
Understanding 3D Printing Technology
Understanding 3D printing technology is crucial in the context of this article because it lays the foundation for integrating generative design principles. 3D printing transforms ideas into tangible objects, making it a significant part of modern manufacturing. Its adaptability offers immediate applicability across various sectors. Moreover, it enables rapid prototyping and complex geometries that align well with the capabilities offered by generative design.
Basic Principles of 3D Printing
3D printing, also known as additive manufacturing, is a technique that builds objects layer by layer from a digital model. It uses additive processes, where materials are joined together rather than subtracted. This principle makes it possible to create intricate structures denied by traditional methods, which often rely on subtractive processes. The essential stages of 3D printing typically include:
- Designing the Model: Using computer-aided design (CAD) software to create a blueprint of the intended object.
- Slicing the Model: Converting the 3D model into thin horizontal layers for the printer's comprehension.
- Adding Material: Utilizing various materials to build objects layer by layer.
These principles underscore the efficiency and innovative possibilities within the technology. In particular, the ability to customize and drive down manufacturing time attracts many industries.
Types of 3D Printing Techniques
Numerous 3D printing techniques exist, each with unique attributes and suitable applications. Among them, significant methods include:
- Fused Deposition Modeling (FDM): This common method involves melting thermoplastic filament and laying it down layer by layer. It is ideal for constructing designs quickly and cost-effectively.
- Stereolithography (SLA): Employs a laser to cure liquid resin into solid forms. This technique provides highly detailed objects, which can be useful in industries requiring precision.
- Selective Laser Sintering (SLS): In this technique, a laser fuses powdered material into solid structures. It enables strong and complex parts, without the need for extensive support structures.
Choosing the appropriate technique is vital for optimizing design implementation. Understanding these types ensures that professionals can decide effectively, preserving integrity in production outcomes.
The Convergence of Generative Design and 3D Printing
The convergence of generative design and 3D printing marks a significant shift in both design and manufacturing processes. The integration of these two advanced technologies presents numerous opportunities and considerations. This union promotes innovation by allowing designers and engineers to explore complex geometries and shapes that would be impossible to achieve using traditional manufacturing methods. Moreover, generative design enhances the capabilities of 3D printers, enabling the production of lightweight and durable components tailored to specific requirements.
How Generative Design Enhances 3D Printing
Generative design employs algorithms to suggest design alternatives. It considers various constraints, including material usage, performance requirements, and production methods. When applied to 3D printing, practitioners can generate optimal models that improve the utility and efficiency of printed parts. This leads to several remarkable benefits:
- Improved Material Utilization: As generative design seeks to minimize waste, the resulting models are often reduced in mass while maintaining structural integrity. This aligns well with the additive nature of 3D printing, which builds objects layer by layer from materials.
- Enhanced Performance Characteristics: 3D printing can manufacture components that are substantially lighter and stronger than conventional methods. Generatively designed parts can be created to enhance functionalities, such as thermal performance and load distribution.
- Rapid Prototyping Capabilities: The synergy of these technologies allows faster turnaround on prototypes. Designers can quickly iterate designs, with direct adjustments fed into the 3D printer, fostering an accelerated feedback cycle.
Thus, generative design not only streamlines the 3D printing workflow but also leads to innovations that set new standards in various industries.
Feedback Loops in Design and Production
Effective feedback loops in design and production processes are essential for continuous improvement. Unlike linear models, adopting an iterative approach with generative design and 3D printing promotes learning from real-world applications. Feedback can stem from:
- Performance Testing Results: Generated designs can be prototyped using 3D printing and then tested under operational conditions. Data gathered here informs new iterations of generative design.
- Material Full OK Feedback: Experiences on how different materials react during printing can influence design adjustments. Knowledge gained during the printing phase can create improvements in subsequent generative outputs.
- User Interactions: In sectors like healthcare, user feedback can guide modifications to user-centric designs to provide improved ergonomics and effectiveness.
This dynamic exchange of information plays a key role in refining designs and optimizing production processes. The mutual influence allows companies to better adapt to changing market demands and leverage the latest technological advancements with maximized efficiency.
Applications Across Industries
Generative design and 3D printing demonstrate significant potential across various sectors. Their spectrum of applications ranges from aerospace innovations to enhancements in healthcare. This section outlines these diverse applications, emphasizing the importance of generative design in creating customized solutions that meet modern demands.
Aerospace and Automotive Sectors
In the aerospace and automotive sectors, generative design offers an unprecedented approach to product development. Aerospace companies, like Boeing and Airbus, employ this technology to optimize weight and enhance performance. Generative design enables engineers to experiment with different geometries at a rapid pace, importantly influencing aerodynamics traits such as drag and efficiency.
The automotive industry benefits similarly. Companies like Ford and General Motors harness generative design for creating lightweight components. These components lead to improved fuel efficiency and overall vehicle performance. Additionally, the integration of 3D printing allows for prototypes to be developed quickly, enabling faster iterations in design.
A geared approach is often adopted, using simulation and modeling software together with 3D printing resources. As a result, engineers can focus on the practicality of designs while pushing creative boundaries. Real-time feedback in model testing allows teams to refine and optimize designs profitably.
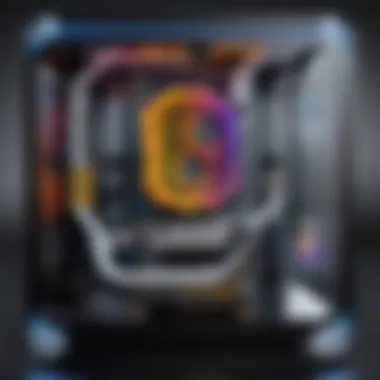
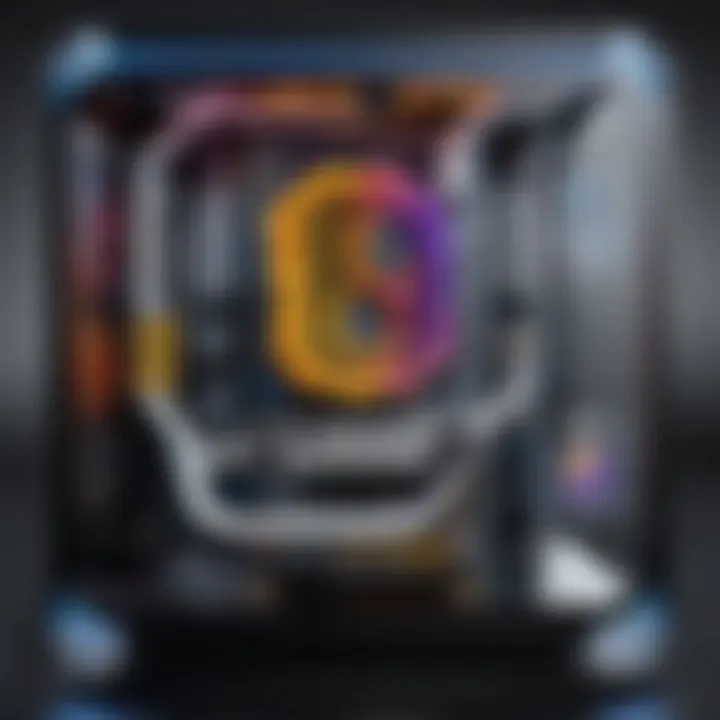
Healthcare Innovations
Healthcare stands to gain immensely from the adoption of generative design and 3D printing. Customization plays a central role here, evidenced by the production of personalized medical devices and implants. Companies such as Materialise have pioneered the generative method to create implants tailored to anatomical contours of individual patients.
Another important consideration is speed. In urgent medical situations, the ability to produce specific parts rapidly saves lives. For example, during surgeries, 3D printed tools and supports reduce the time surgeons typically spend on custom equipment.
Additionally, the sterilization processes that many emerging generative designs factor into manufacturing drugs abnormalities via 3D printing also stand out for medical benefits—not only improving treatment prospects but resetting standards across multiple practices.
Consumer Goods and Electronics
The consumer goods and electronics market represents another area benefiting from the integration of generative design and 3D printing. Designers leverage technology for product personalization, seamlessly adjusting the aesthetics or functionality based on consumer feedback. Brand driven differentiation is crucial in a saturated marketplace.
Smartphone manufacturers like Apple and Samsung are exploring additional value with unique casing utilizes enhanced sound systems, layouts backed both in structure and personalized elements aiding user ease solutions across sustained attempts in launch products.
3D printing allows companies to prototype products efficiently. Timely responses to design changes create better opportunities to meet customer demand promptly. Therefore consolidating resource efficiency across outreach prevents too much material waste during production.
“The convergence of generative design with traditional manufacturing methods is not merely a trend; it signals profound changes in how consumer products will be produced and customized in the future.”
Overall, applications from aerospace industries, healthcare, and consumer goods reveal the multifaceted advantages of generative design in 3D printing.
Benefits of Integrating Generative Design and 3D Printing
The integration of generative design with 3D printing is no mere trend; it represents a significant advancement in manufacturing capabilities. This synergy not only enhances innovative design processes but also addresses practical manufacturing challenges. As various industries look to improve efficiency and output quality, understanding these benefits proves crucial.
Cost Efficiency and Resource Management
One of the standout advantages of incorporating generative design in conjunction with 3D printing is the impressive cost efficiency it delivers. When companies employ generative design software, they utilize algorithms to examine numerous design options. These designs typically optimize material usage while improving functional performance.
For instance, traditional manufacturing often leads to wasted material due to the constraints of subtractive methods. In ff contrast, 3D printing allows for the creation of intricate shapes that minimize excess waste, making it more sustainable. Not only do these technologies lower production costs, they also facilitate better resource management by making use of affordable materials and reducing overproduction. Thus, businesses benefit from improved forecasts and decreased inventory costs.
The following aspects encapsulate the impact on cost efficiency and resources:
- Reduction in Material Waste: 3D printing's layer-by-layer build process optimally uses materials.
- Lower Production Costs: Integrating these technologies leads to streamlined methodologies.
- Custom Supply Chains: Companies can produce small batches of customized products without incurring significant overhead costs.
Customization and Flexibility
The landscape of product design is evolving rapidly, with customization and flexibility at its core. Generative design takes user specifications and computes potential solutions, accommodating unique demands effectively. Combined with 3D printing, this leads to a highly adaptable production process, which is particularly essential in today's fast-paced market.
Manufacturers can quickly pivot in response to customer feedback or shifting trends in consumer preferences. For example, an automotive company could rapidly develop tailored components that align precisely with performance specifications or aesthetic desires. This is a distinct advantage over conventional methods that often rely on large batch production runs.
Furthermore, the capability for real-time adjustments fosters true innovation as designers can test different variations without the burden of long lead times. The benefits in this realm include:
- User-Centric Designs: Products are not just built but tailored to specific user requirements.
- Rapid Prototyping: Feedback loops give developers the ability to prototype within hours, speeding up the innovation cycle.
- Versatile Applications: These technologies can cater to various fields, from health to industrial design.
This transforming nature of generative design and 3D printing empowers companies to not only meet demand but to exceed it, turning visualization into creation efficiently and effectively.
As companies strive to offer personalized experiences, the integration of generative design with 3D printing is paving the road forward. Overall, the benefits translate into direct competitive advantages, setting businesses apart in increasingly crowded marketplaces.
Challenges in Implementation
The implementation of generative design and 3D printing holds significant promise for diverse industries. However, there are crucial challenges that organizations must address as they navigate this landscape. Understanding these challenges is vital for realizing the full potential of these transformative technologies. This section elaborates on two core aspects: technical limitations and the essential skills gap. Both elements exemplify the complexity surrounding effective integration into current workflows.
Technical Limitations of Current Technology
Although generative design and 3D printing have made remarkable strides, technical limitations remain prominent. These limitations are not just isolated issues; they influence the broad adoption of these technologies across various sectors.
- Material Constraints: At present, the range of materials compatible with generative design processes and 3D printing is limited. The common materials, such as PLA and ABS, have attributes that may not meet advanced requirements for durability or temperature resistance in critical applications. Emerging materials are on the horizon, but their adoption may lag due to production workflows and testing hurdles.
- Resolution and Detail: The resolution at which current 3D printers operate is insufficient for high-precision applications. Especially in industries like healthcare, where accuracy can be life-critical, these limitations can impact the effectiveness of printed solutions. Furthermore, the adaptability of currently available printers to match diverse design requirements can stifle innovation.
- Post-Processing Requirements: Many additive processes need extensive post-processing to achieve optimal results. This adds time and resource costs, counteracting the advantages that 3D printing offers—speed and efficiency.
In sum, organizations reliant on generative design should proactively look to
The Role of Artificial Intelligence in Design
Artificial Intelligence (AI) is an increasingly significant part of the generative design framework. It enables methods for analyzing complex data and optimizing designs beyond traditional capabilities. The incorporation of AI not only expedites the design process, but it also improves accuracy and functionality of the 3D printed items.
AI facilitates the generation of highly performance-oriented designs by processing vast amounts of variables that would otherwise overwhelm human designers. This technology helps to find the ideal solution considering parameters such as materials, costs, environmental conditions, and user requirements. Overall, the role of AI in generative design manifests profound benefits, including enhanced productivity, resource management, and improved innovativeness.
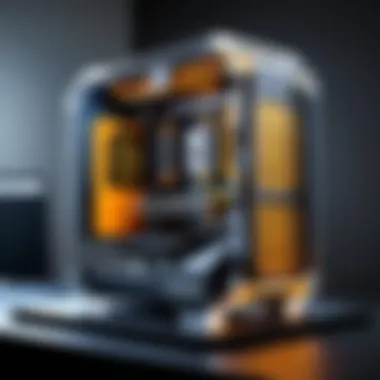
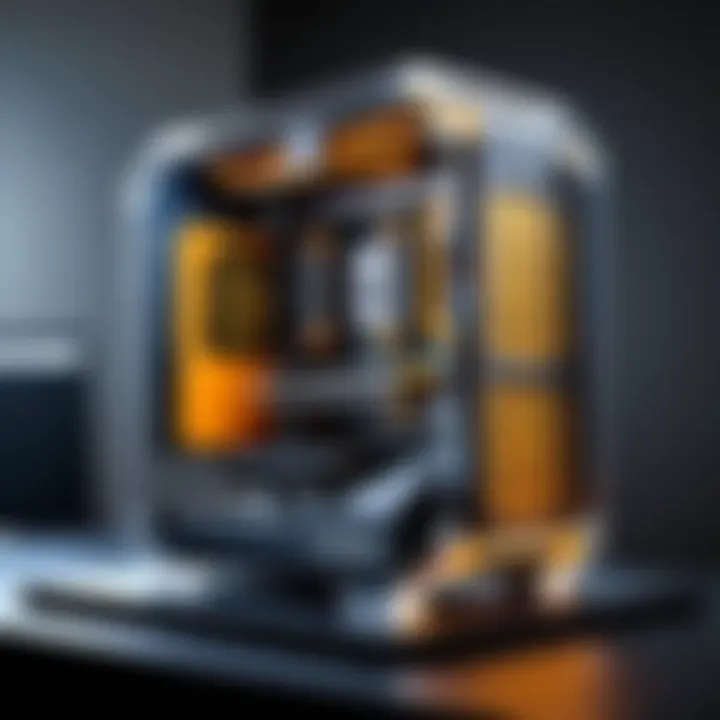
Machine Learning and Design Optimization
Machine learning is a core component of AI that harnesess patterns from data to inform decisions. Machine learning algorithms can modify design elements based on performance data gathered from simulations or previously manufactured parts. This creates a cycle of continuous improvement.
In practice, design teams may feed a range of designs into these algorithms. The systems analyze factors like stress distribution, weight efficiency, and material orientation, then suggest modifications.
Notably, machine learning reduces development time and error rates. Designers can iterate rapidly as idea generation becomes data-backed. Thus, teams utilize their time more strategically, focusing on refining and enhancing ideas instead of sifting through mountains of options.
Data-Driven Decision Making
Data-driven decision making emphasizes collecting data to make informed choices during the design process. By incorporating real-time data about manufacturing methods, material properties, and market trends, organizations can develop designs aligned closely with user needs and operational capabilities.
Implementing such data-centric methods can lead to significant advantages:
- Enhanced Precision: Leveraging accurate datasets improves design outputs and product reliability.
- Mitigated Risks: Understanding market demands and technological changes lowers the chances of project failures.
- Customer Satisfaction: Designing around data-driven insights improves how well products meet user preferences and requirements.
Fundamentally, integrating AI in design can set a pathway for smarter, efficient design cycles that escalate the potential of generative design in modern 3D printing workflows. It allows businesses to embark on innovative ventures with minimized risks and maximized gains.
Future Trends in Generative Design and 3D Printing
The future of Generative Design and 3D Printing holds transformative potential for various industries. As this technology evolves, several trends become quite evident that reshape our understanding and methodology of production. Notably, emphasis shifts towards innovative materials and a concerted focus on sustainability that respond effectively to the demands of contemporary manufacturing practices. Identifying these trends equips both tech enthusiasts and professionals with insights necessary to remain competitive in an ever-changing landscape.
Emerging Materials and Their Impact
The introduction of new materials in 3D printing enhances the scope and capabilities of generative design. Traditional options like plastics and metals are no longer the only players. Emerging materials include:
- Bio-based Polymers: These materials are derived from renewable sources and cater to both environmental concerns and aesthetic requirements.
- Metal Matrix Composites: Blending metals with ceramics or polymers leads to enhanced properties like improved strength and lightweight characteristics.
- Graphene-infused Materials: Uses of graphene drastically boost performance metrics, especially thermal and electrical conductivity.
Changes in material science change how generative algorithms function. Designers can create structures that are fundamentally stronger or lighter, directly affecting product lifecycle and performance. The learning curve associated with using these materials presents challenges, yet the benefits are undeniable:
Case Studies
Case studies provide vital insights into the tangible applications of generative design within the 3D printing landscape. They showcase how companies successfully implemented generative design principles and thereby reaped considerable benefits. Business implementations offer clear examples, illustrating scalability, customization, and sustainable manufacturing practices. They present documented evidence of the effectiveness of these technologies. Additionally, examining failures is crucial. Understanding mistakes made serves as invaluable lessons for industries aiming to adopt these technologies in the future. Together, successful implementations and lessons from failures cumulatively enrich the dialogue surrounding generative design.
Successful Implementations in Business
In today's market, various businesses have embraced generative design through 3D printing with striking results. Notable companies include:
- BMW: The automotive giant has employed generative design to optimize parts production by analyzing weight reduction without compromising robustness. This advancement enhances vehicle performance and increases overall fuel efficiency.
- Nike: Their Flyknit shoe technology showcases how generative design can create intricate structures that minimize material waste while also achieving a perfect fit for users. This not only boosts performance but makes manufacturing smoother.
- GE Aviation: General Electric's development of fuel nozzles using additive manufacturing highlights reductions in assembly time and overall costs. Their innovative nozzles’ designs are even more robust despite being significantly lighter.
These cases reinforce the effectiveness of generative design in practical applications across industries, showcasing improved production processes and sustainable practices.
Lessons Learned from Failures
While successful implementations offer fertile ground for growth, failures lend critical insights too.
- In some companies, overly ambitious design objectives have backfired. Engineers might not have accounted for practical manufacturing limitations. As complexity increased, prototypes became costly and logistically challenging to produce.
- Another risk is the technology skills gap. Some firms advanced without ensuring an adequately trained workforce, leading to poor outputs and ultimately wasted investments.
Lessons such as these emphasize the importance of setting realistic goals and aligning staff training sessions to technology upgrades.
Next time, industries adopting generative design in 3D printing should emphasize integration and communication throughout the project. Engaging the entire design-production chain is essential.
Gleaning experiences from industry case studies fosters an in-depth understanding of what works well and what needs reevaluation as technology progresses.
Closure and Insights
Generative design, combined with 3D printing, cultivates an expansive realm of possibilities within modern manufacturing. To understand the essence of this article, it is crucial to highlight key facets and contemplated outlooks. This section distills these insights comprehensively.
Summarizing Key Findings
In this discourse, several central themes emerge with substance.
- Integration Synergy: The alignment of generative design with 3D printing technology stimulates innovative solutions across various sectors, reshaping traditional manufacturing methodologies.
- Enhanced Customization: Customization is notably amplified. Generative design permits adaptation to complex design requirements, enabling personalized products that traditional manufacturing methods may not easily realize.
- Resource Efficiency: It substantially enhances sustainable practices. The approach minimizes material waste by optimizing structure without influencing overall functionality, showing true progress towards environmentally responsible manufacturing.
- AI's Contribution: The involvement of artificial intelligence serves as a keystone in advancing design processes. Machine learning not only enhances the complexities in design choice-making but certifies efficient processing within production lines.
- Challenges Addressed: This article accentuates pressing hurdles such as workflow integration and a current skills gap. Addressing these obstacles is pivotal for leveraging full potential within generative design and 3D printing sectors.
A summation of these findings highlights not just the nuances of combining generative design with 3D printing, but establishes a clear route toward engaging future engagements within this swiftly evolving industry. The concepts discussed can transform industries through innovative practices.
The Way Forward
Looking ahead, the convergence of generative design and 3D printing indicates transformative shifts in the approach to manufacturing. Future endeavors warrant consideration of multiple determinants:
- Investing in Skill Development: The inevitable need for a workforce trained in highly specific design techniques pairs exploring opportunities internally. Fostering educational paths will prove imperative as technologies advance.
- Pushing Technological Constraints: Robust research aimed at developing new materials further pushes the boundary capabilities of both design strategies and their impact on production methodologies.
- Exploration of Automated Systems: Understanding and incorporating automation in production workflows will dramatically increase efficiency, completeness of designs, and lead to longer production runs with significant downtimes minimized.
- Evaluate Sustainability Perspectives: By focusing on eco-friendly techniques nudging industries toward better practices, organizations greatly enhance reputations while also upholding responsibilities towards communities and environment.