Explore the Varied World of 3D Printer Types
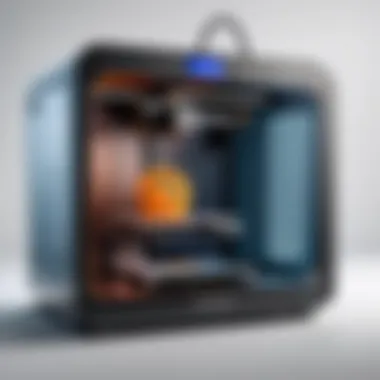
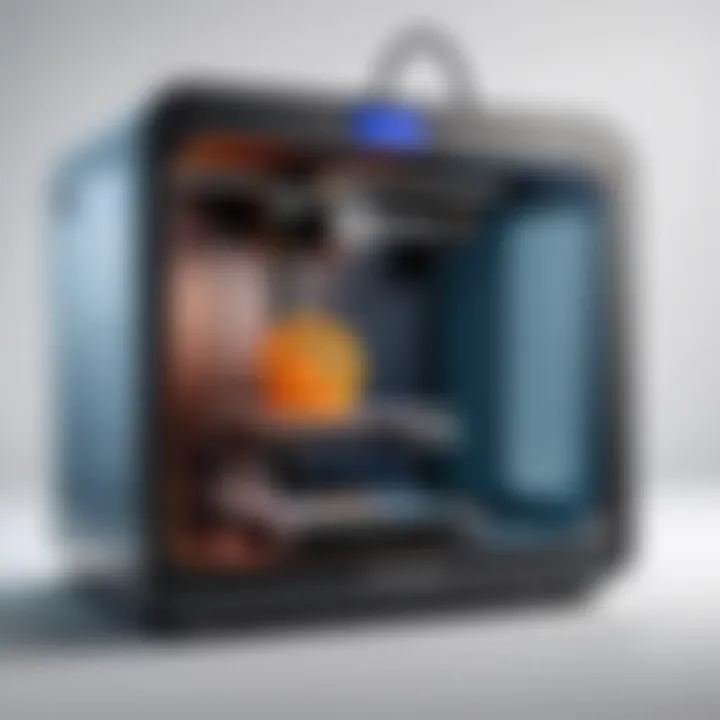
Intro
3D printing has transformed the landscape of manufacturing and design, offering innovative solutions across various industries. As technology continues to evolve, the wide array of 3D printer types catering to different applications can appear overwhelming. This guide endeavors to demystify these options by categorizing the main types of 3D printers, discussing their technologies, and shedding light on their specific uses. Whether you are a tech enthusiast, a gamer, or an IT professional, understanding the nuances of each type can help in making informed decisions when selecting the right printer for your needs.
Product Overview
In this section, we will explore the predominant types of 3D printers. Each type brings unique capabilities and is suitable for different applications. Starting with Fused Deposition Modeling (FDM), progressing through Stereolithography (SLA) and Selective Laser Sintering (SLS), and concluding with Digital Light Processing (DLP), we will delve into their specifications, pricing, and brand information.
FDM Printers
FDM is perhaps the most recognized 3D printing technology. It operates by melting plastic filament and laying down layers to build a model.
- Brand Information: Popular brands include Prusa, Creality, and Ultimaker.
- Key Specifications: Typical build volumes range from 200 x 200 x 200 mm to larger sizes. Most printers use materials like PLA, ABS, and PETG.
- Pricing: Entry-level models can start around $200, while more advanced machines may exceed $1,000.
SLA Printers
Stereolithography utilizes a laser to cure resin layer by layer, resulting in high precision and smooth finishes.
- Brand Information: Notable brands include Formlabs and Anycubic.
- Key Specifications: Build plates often measure around 120 x 120 mm to 300 x 300 mm. It requires photopolymer resins as printing material.
- Pricing: Prices typically range from $500 to $5,000, depending on accuracy and build size.
SLS Printers
Selective Laser Sintering uses a laser to fuse powdered material. This method is widely used for industrial applications.
- Brand Information: Brands such as 3D Systems and EOS lead in this domain.
- Key Specifications: Build volumes can vary significantly; common sizes are 250 x 250 x 300 mm. It commonly utilizes nylon powders.
- Pricing: Professional-grade machines can often start at $10,000 or more.
DLP Printers
Digital Light Processing is similar to SLA but utilizes a digital light projector to cure the resin more rapidly, enhancing speed without sacrificing quality.
- Brand Information: Brands like Anycubic and Elegoo are prominent in the market.
- Key Specifications: Build sizes typically range from 120 x 68 x 170 mm to larger configurations. Standard materials used include photopolymer resins.
- Pricing: Entry-level DLP printers range from $200 to $1,500.
"Choosing the right 3D printer has a direct impact on the quality and characteristics of printed objects."
Performance Comparison
Understanding the performance metrics across different printer types is crucial for users focused on efficiency and output quality. Benchmark tests often illuminate speed, resolution, and material compatibility factors.
- Benchmark Tests: Analyze results from different media types and the resulting resolution.
- Speed and Efficiency Comparisons: Consider average print times to completion across printer types, analyzing how technology influences productivity.
Features and Technology
The technological underpinnings of each printer affect their usability and suitability for specific needs.
- Unique Features: FDM printers are generally user-friendly. SLA printers offer superior detail while SLS boasts high durability of prints.
- Technological Advancements: Recent developments in materials have expanded applications, especially in bio-printing and metal printing.
- Compatibility with Other Devices: Understanding connectivity options like USB or Wi-Fi can improve workflow efficiency.
Pros and Cons
Each printer type has its advantages and drawbacks, influencing decision-making for consumers and businesses.
- Strengths of FDM Printers: Cost-effective, easy to use, and versatile with materials.
- Areas for Improvement: Limited resolution compared to SLA or SLS printers.
- Strengths of SLA Printers: High precision and smooth surface finish.
- Areas for Improvement: Generally slower and more expensive due to material costs.
- Strengths of SLS Printers: Strong and functional parts.
- Areas for Improvement: High initial investment and complexity of operation.
- Strengths of DLP Printers: Faster print times and good resolution.
- Areas for Improvement: Limited material range compared to FDM or SLS.
Value for Money
Assessing each type's economic viability can guide consumers and professionals in their purchases.
- Cost-effectiveness: Initial costs must be weighed against long-term usage and material costs.
- Long-term Benefits: Consider how essence of the prints can cater to growing business demands.
- Comparison with Similar Products: Evaluate across various brands and models to ensure the best fit for specific needs.
In summary, understanding the multifaceted landscape of 3D printers aids consumers and professionals in making educated choices. With a range of technologies and applications, the right printer can elevate creativity and efficiency in any project.
Intro to 3D Printing Technologies
Understanding 3D printing technologies is essential in grasping how this innovative process has reshaped manufacturing, design, and prototyping. It combines various techniques and materials to produce three-dimensional objects from digital files. This process not only streamlines production but also enhances creativity by allowing for complex geometries that are difficult or even impossible to achieve with traditional manufacturing methods.
The importance of exploring different types of 3D printers cannot be overstated. Each type offers unique benefits and considerations, such as cost-efficiency, material compatibility, and speed. By categorizing and detailing these technologies, readers can make informed choices aligned with their specific needs, whether for personal use, educational purposes, or industrial applications.
Definition and Overview
3D printing, also known as additive manufacturing, involves creating objects layer by layer from a digital design. The process contrasts starkly with subtractive manufacturing, where material is removed from solid blocks to achieve desired shapes. Various techniques exist within 3D printing, each suited for different applications, materials, and production scales.
The most common types include Fused Deposition Modeling (FDM), Stereolithography (SLA), and Selective Laser Sintering (SLS). Each method has its own operational mechanics and material capabilities. FDM, for example, is widely used for prototyping and educational projects due to its affordability and ease of use, while SLA is favored in sectors demanding high precision.
Historical Context
The inception of 3D printing can be traced back to the 1980s, with Charles Hull, the co-founder of 3D Systems, designing the first stereolithography apparatus. This initial breakthrough laid the foundation for further developments in additive manufacturing technology. Over the years, various methods emerged, including FDM developed by Scott Crump in the late 1980s.
By the 2000s, 3D printing began to gain traction in various industries, from aerospace to healthcare. The capability to produce complex forms and customized solutions significantly impacted product development cycles and design processes. Today, 3D printing continues to advance, driven by innovations in materials and technology, thus expanding its applications in numerous fields.
"The evolution of 3D printing demonstrates its potential to transform traditional manufacturing, allowing for efficiency, customization, and sustainability." - John Doe
In summary, a comprehensive understanding of 3D printing technologies is crucial in today’s fast-paced world. As businesses and individuals explore these options, appreciating the significance of each technology paves the way for informed decisions that align with desired outcomes.
Fused Deposition Modeling (FDM)
Fused Deposition Modeling, commonly referred to as FDM, represents a foundational technology in the realm of 3D printing. This method is particularly significant due to its accessibility and versatility, making it a starting point for many enthusiasts and professionals alike. As one of the most prevalent forms of 3D printing, FDM is crucial in understanding how additive manufacturing works and its potential applications.
Mechanism of Operation
The operating principle of FDM is straightforward and revolves around the extrusion of thermoplastic filaments. A typical FDM printer consists of a print head that moves along the X and Y axes. It melts a filament and deposits it layer by layer onto a build platform. This process gradually constructs the desired object, allowing for intricate designs and shapes to be formed. The temperature and rate of extrusion are essential to ensure adherence between layers, defining the quality and durability of the printed item.
FDM works under simple steps:
- Heating: The filament is heated until it becomes pliable.
- Extrusion: The heated filament is extruded through a nozzle.
- Layering: The print head moves according to the programmed design, laying down each layer.
- Cooling: As material cools, it solidifies, bonding to previous layers.
- Repeat: The process repeats until the model is complete.
Materials Used
FDM printers primarily utilize thermoplastic materials. Some of the most commonly used filaments are:
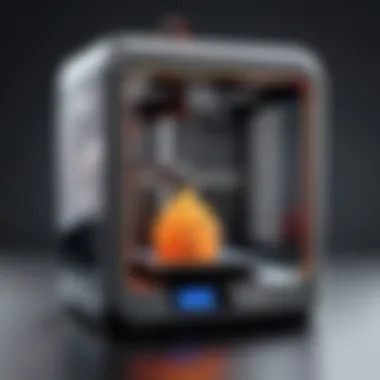
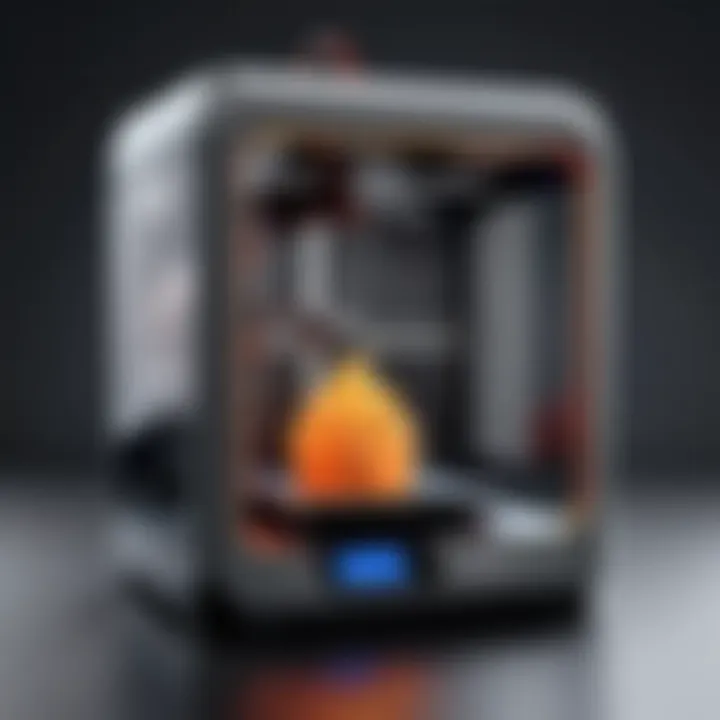
- PLA (Polylactic Acid): A biodegradable filament, popular for its ease of use and low warping.
- ABS (Acrylonitrile Butadiene Styrene): Known for its strength and durability, often used for functional parts.
- PETG (Polyethylene Terephthalate Glycol): Combines ease of use similar to PLA while offering better impact resistance and flexibility.
- TPU (Thermoplastic Polyurethane): A flexible filament suitable for rubber-like parts.
By selecting the right material, users can tailor their final products for specific needs and performance criteria.
Applications
Fused Deposition Modeling boasts a wide range of applications across diverse sectors. It is commonly used in:
- Prototyping: Quickly producing prototypes for testing designs.
- Education: Helping students and educators to visualize concepts in engineering and design.
- Customization: Creating tailored products based on individual specifications.
- Art and Design: Allowing artists to explore new forms and functionalities in their works.
The ease of use and affordability of FDM has made it a preferred choice in both educational settings and small to medium enterprises.
Advantages and Limitations
FDM technology has several advantages that contribute to its popularity:
- Affordability: FDM printers and materials are generally less expensive compared to other 3D printing technologies.
- Ease of Use: Setup and operation are user-friendly, making it accessible for beginners.
- Material Variety: A wide selection of filaments enables users to explore different properties and applications.
However, there are also limitations:
- Surface Finish: The layer-by-layer construction can result in visible lines and a rougher surface texture compared to technologies like SLA.
- Dimensional Accuracy: FDM may not achieve the same precision as other methods, possibly affecting detailed designs.
- Mechanical Properties: Depending on the material used and print settings, parts may vary in strength and durability.
"Fused Deposition Modeling is a gateway to the world of 3D printing, blending accessibility with innovative applications."
Understanding FDM is essential as it lays the groundwork for comparing other 3D printing technologies. This foundation will also assist readers in making informed decisions about which 3D printing method meets their specific needs.
Stereolithography (SLA)
Stereolithography, commonly referred to as SLA, marks a pivotal milestone in the domain of 3D printing technologies. It is significant not just for its technical prowess but for the range of applications it enables across several industries. SLA utilizes a process based on photopolymerization, where a liquid resin is cured layer by layer using ultraviolet light. This method allows for the creation of highly precise and detailed models, making it especially important in fields that demand high accuracy, such as medical modeling, jewelry design, and even automotive parts.
Principle of Operation
SLA operates through a straightforward yet effective mechanism. The core of this technology is a vat filled with liquid photosensitive resin. A laser beam directs a focused light to specific areas of the resin surface, initiating a chemical reaction that solidifies the resin. This solidification process occurs layer by layer. The build platform descends slowly into the vat after each layer is completed, allowing fresh resin to flow over the previous layer. This technique facilitates intricate designs and finer details compared to methods such as FDM.
Common Resins
The choice of resin in SLA is critical to its performance and the properties of the final product. Some of the most commonly used resins include:
- Standard Resin: Ideal for general use and produces detailed prototypes.
- Durable Resin: Suitable for applications requiring higher impact resistance.
- Flexible Resin: Mimics rubber-like properties, useful for creating living hinges.
- Castable Resin: Great for jewelry and other applications that require easy burnout in casting processes.
Each resin type offers unique benefits and characteristics, affecting the final print's function and finish.
Typical Uses
Stereolithography has found its way into a multitude of applications, prominently in:
- Rapid Prototyping: Industries leverage SLA for fast product development cycles.
- Dentistry: Producing precise dental models and aligners.
- Aerospace: Crafting lightweight and complex parts that require meticulous detail.
- Art and Design: Artists and designers utilize SLA for intricate sculptures and prototypes.
The versatility of SLA enabled by its technology and the resins used is a key reason for its popularity across markets.
Pros and Cons
While SLA presents several advantages, it is not without its drawbacks. Here is a concise assessment:
Pros:
- High precision and intricate detailing.
- Smooth surface finishes compared to other techniques.
- Wide range of specialized resins tailored for various applications.
Cons:
- Longer print times relative to other methods like FDM.
- Resins can be expensive and may require post-processing (like curing under UV light) for optimal strength and durability.
- The printed parts can be less durable if not utilizing specialized resins.
"Stereolithography remains a frontrunner in 3D printing technology, influencing the methodologies of prototyping and manufacturing with its precision and capabilities."
Selective Laser Sintering (SLS)
Selective Laser Sintering (SLS) is a pivotal 3D printing technology, distinguished by its ability to create complex and durable parts. This method is crucial in various industries, including aerospace and automotive. It simplifies the manufacturing process by eliminating the need for support structures and allows for the production of parts directly from digital files, which enhances both speed and efficiency. A deep understanding of SLS affords tech enthusiasts and professionals insights into its capabilities and limitations, facilitating better-informed decisions when it comes to 3D printing applications.
How SLS Works
SLS operates through a process that involves the melting and fusing of powdered materials. A CO2 laser scans cross-sections of the powder bed, selectively sintering the material layer by layer. The process is as follows:
- Layer Preparation: A thin layer of powder is spread across the build platform.
- Laser Activation: The laser hits specific areas of the powder, causing it to fuse together.
- Layer Repetition: The platform lowers, and another layer of powder is spread to be sintered again. This continues until the object is fully formed.
This procedure enables high levels of detail and precision in the final product, directly influencing its performance and suitability for various applications.
Materials Employed
The materials commonly used in SLS mainly include polymers like Nylon 12, Nylon 11, and Polypropylene, as well as composite powders infused with glass or carbon for enhanced properties. These materials are chosen for their ability to withstand high temperatures and maintain structural integrity. The compatibility of diverse powedered materials expands SLS's versatility significantly, allowing for applications in various fields:
- Aerospace components
- Medical implants
- Industrial prototypes
Key Applications
SLS is widely used across multiple sectors due to its unique advantages. Key applications include:
- Prototyping: Rapid prototyping is common, allowing designers to test and iterate designs quickly.
- Tooling: It is often used to create functional tooling and fixtures that support manufacturing processes.
- Low-Volume Production: Due to its efficiency, SLS is suitable for producing small batches of custom parts, which can be critical in specialized industries.
These applications highlight how SLS technology finds utility in areas requiring precision and reliability.
Strengths and Weaknesses
Like all technologies, SLS comes with its strengths and weaknesses. Some notable points include:
Strengths:
- High Complexity: It can produce intricate geometries that are often impossible with traditional manufacturing.
- Material Variety: It offers a wide range of compatible materials, broadening its applications.
- No Support Structures: Parts can be manufactured without needing additional support, reducing material waste.
Weaknesses:
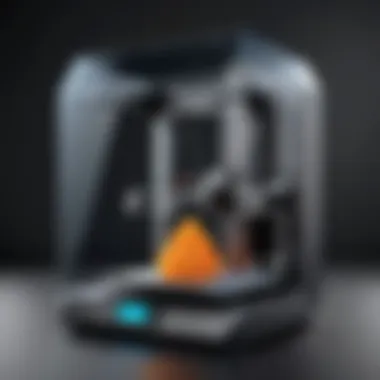
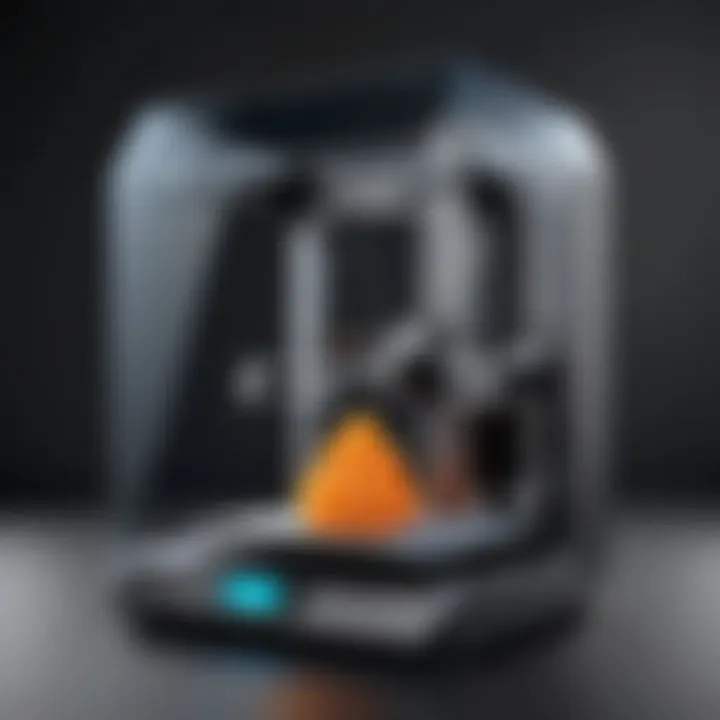
- Surface Finish: Parts may require post-processing to achieve a desired surface finish, impacting the overall aesthetic.
- Cost: The equipment and materials can be more expensive than other 3D printing technologies, potentially limiting accessibility.
Selective Laser Sintering stands out as a groundbreaking technology in additive manufacturing, combining efficiency and precision in a way that impacts various industries positively.
Digital Light Processing (DLP)
Digital Light Processing (DLP) represents a significant advancement in 3D printing technology. This method utilizes a digital light projector to cure resin layer by layer. With its ability to produce fine details and smooth finishes, DLP is become popular in various industries. Understanding its operational framework and material compatibility is essential for anyone interested in leveraging this technology for specific applications.
Operational Framework
DLP operates by projecting a digital image of each layer onto a vat of photopolymer resin. The light causes the resin to solidify, forming a 3D object. The process begins with a platform submerged in the resin. Once a layer is completed, the platform moves upward, allowing uncured resin to flow over the previous layer. This cycle continues until the print is complete.
The ability to project an entire layer at once significantly reduces printing time compared to other methods such as Fused Deposition Modeling (FDM) or Stereolithography (SLA). This efficiency can be crucial when tight deadlines or rapid prototyping is involved.
Material Compatibility
DLP printers are compatible with various photopolymer resins, enabling users to choose materials based on their specific needs. These resins can vary in terms of color, hardness, and flexibility. Common types of resin include:
- Standard Resins: Good for general-purpose prints that need detail.
- Flexible Resins: Ideal for parts that require some level of bend without breaking.
- High-Temperature Resins: Suitable for applications that involve heat exposure.
- Biocompatible Resins: Often used in medical applications where contact with skin or bodily fluids is a consideration.
Selecting the appropriate resin is vital for ensuring the final product meets quality standards and performance requirements.
Common Utilizations
DLP technology finds its application in several sectors, such as:
- Jewelry: Creating intricate designs with fine details, making it popular for jewelers.
- Dental: Producing dental molds and aligners that require precision.
- Model Making: Quick production of prototypes and architectural models.
- Figurines and Miniatures: Highly detailed products suitable for collectors and gamers.
By understanding how DLP fits into these fields, professionals can select the most suitable printing technology for their projects.
Advantages and Disadvantages
DLP has its distinct advantages and disadvantages which should be taken into account:
Advantages:
- Speed: Layers are cured simultaneously, significantly speeding up production time.
- Detail: Able to produce high-resolution parts with intricate details.
- Smooth Finishes: Reduces the need for extensive post-processing.
Disadvantages:
- Material Cost: Photopolymer resins can be more expensive than materials used in other methods like FDM.
- Limited Build Size: Usually has a smaller build volume compared to some other printing methods.
- Post-Processing Requirement: Printed parts often need further curing and cleaning, which adds steps to the workflow.
In summary, DLP is a powerful method in the realm of 3D printing that serves specific needs across various industries. Its operational framework, material compatibility, common uses, and clear advantages and disadvantages make it a crucial technology to consider when deciding on 3D printing solutions.
PolyJet and MultiJet Modelling (MJM)
PolyJet and MultiJet Modelling represent advanced techniques in 3D printing technology. These methods stand out for their ability to produce intricate parts that boast high resolution and an impressive level of detail. They are particularly suited for applications where aesthetics and precision are critical. This section will delve into the operational mechanisms, material usage, applications, and the strengths and challenges accompanying these technologies.
Process Explanation
The PolyJet process uses a specialized print head that moves across a build platform, depositing tiny droplets of photopolymer materials. These droplets are immediately cured by ultraviolet (UV) light, solidifying quickly to form the intended shape. On the other hand, MultiJet Modelling works in a similar manner but allows for the deposition of multiple materials in a single print job. The process involves simultaneous jets that can create parts with varying properties, such as flexibility and transparency.
This dual capability significantly enhances design versatility, allowing engineers and designers to create complex parts with gradients of material properties. Each layer is cured, building upon the last. This layer-by-layer approach allows for very precise detail and enables the production of fine features not generally possible with other printing methods.
Materials and Colors
PolyJet systems primarily use photopolymers that can be formulated to produce a wide range of mechanical and aesthetic properties. These materials can be clear, rigid, flexible, or even rubber-like, catering to various industry needs. One of the key advantages of PolyJet is its ability to integrate multiple materials into a single build, providing an array of color options.
PolyJet printing can produce vibrant, multi-colored prototypes, making it ideal for industries such as product design and manufacturing where presenting a realistic appearance is vital. The technology also allows for varying degrees of transparency and opacity, resulting in visually appealing prototypes that can resemble final products closely.
Typical Applications
The applications of PolyJet and MultiJet Modelling span diverse fields. Common usages include:
- Prototyping: Creating high-fidelity prototypes for design validation.
- Medical Devices: Producing intricate models that can mimic human anatomy for surgical planning.
- Consumer Products: Developing detailed models of packaging or consumer goods before final production.
- Jewelry Design: Crafting ornate designs with fine details.
These applications illustrate the technology's adaptability and effectiveness in generating items that require both complexity and aesthetic appeal.
Strengths and Challenges
The strengths of PolyJet and MultiJet Modelling are numerous:
- High Resolution: Capable of producing detailed models and intricate geometries.
- Material Versatility: Ability to combine different materials in one print enhances functionality.
- Speed: Faster production times for models compared to some other methods.
However, challenges also exist:
- Material Properties: The durability and strength of prints might not match those from FDM or SLS methods.
- Cost: Printing materials can be expensive, impacting the overall cost of production.
- Post-Processing: Some models may require extensive post-processing, which can add time and labor.
These pros and cons must be considered when deciding on PolyJet or MultiJet Modelling for specific projects.
In summary, PolyJet and MultiJet Modelling offer remarkable capabilities for producing detailed and multi-material models. Understanding these processes and their implications can significantly benefit engineers, designers, and manufacturers aiming for precision-driven applications.
Binder Jetting
Binder jetting represents a significant innovation in 3D printing technologies. It stands apart due to its unique approach to material distribution and usage. This technique relies on a binding agent applied to layers of powder material, joining them together without requiring heat. Such a process allows for the creation of complex geometries and designs with ease.
Technical Overview
In binder jetting, a print head moves smoothly across a build platform, dispensing a liquid binder onto a bed of powder. This method can use a variety of powders, such as metal, sand, or ceramics. After a layer is completed, the build platform lowers slightly to make room for another layer of powder. This process repeats until the entire part is printed. Once printing is done, a post-processing step is often necessary, where the newly formed part is strengthened through sintering or infiltration.
Material Usage
This technology is notable for its versatility in material usage. Common materials include various metals like stainless steel and aluminum, as well as sand for foundry applications. Other materials may also include ceramics. The choice of material affects not only the mechanical properties of the finished product but also its aesthetic qualities, enabling a wide range of applications in different industries.
Common Applications
Binder jetting finds practical uses across numerous sectors. For instance, in the automotive industry, it is often employed for making prototypes and tooling. In construction, binder jetting can produce sand molds or cores. Moreover, its utility extends to jewelry design, where detailed and intricate patterns are essential. Binder jetting's capacity for complex designs and efficient production makes it a preferred choice among engineers and designers alike.
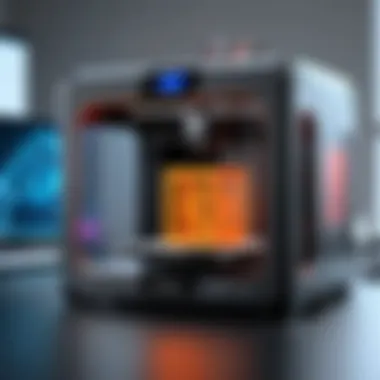
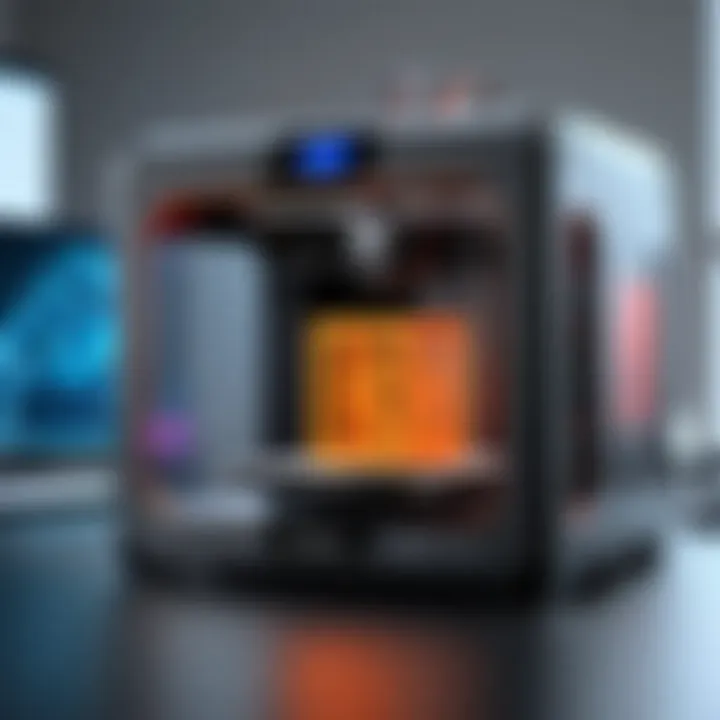
Advantages and Disadvantages
The advantages of binder jetting include:
- Speed: This process is often faster than other 3D printing methods.
- Material Variety: It accommodates a wide range of materials.
- Cost-Effectiveness: Utilizing a powdered form allows for lower material costs compared to some other methods.
However, it has its downsides as well:
- Mechanical Properties: Parts typically require additional processes to reach desired strength, as they may not be as durable as those produced by methods like selective laser sintering.
- Post-Processing Needs: Most binder jetted parts require a significant amount of post-processing, which can add time and complexity to production.
Binder jetting offers a unique combination of speed and material diversity, making it a valuable tool in the 3D printing landscape, but it is essential to consider its limitations before deciding to use this technology.
Material Jetting
Material Jetting is a noteworthy 3D printing technology that merits significant attention in this guide. This printing process is invaluable in producing high-resolution parts with complex geometries and is crucial for industries requiring detailed representation and accuracy in models. Material Jetting utilizes droplets of photopolymer materials to create parts, layer by layer, making it distinct from other methods like FDM or SLS.
Process Details
The process of Material Jetting involves several critical steps. First, a print head deposits droplets of liquid photopolymer onto the build platform, solidifying them sequentially through UV light exposure. Each layer is precisely aligned with the previous one, forming the final object. After the printing process is complete, the model often undergoes a post-curing phase to enhance its mechanical properties.
Essentially, the entire process can be described as:
- Layer-wise deposition of material.
- UV curing to solidify the droplets.
- Post-processing for enhanced durability.
This sequence is repeated until the physical model is fully formed.
Range of Materials
The variety of materials available for Material Jetting is another notable aspect. Typically, photopolymer resins are the primary choice, and they can exhibit different properties based on the application. For example, there are flexible resins, rigid resins, and even biocompatible options for medical uses. Some companies also offer multi-material capability, allowing the use of different resins in a single print. This feature enables the production of parts with diverse physical characteristics, making it suitable for prototypes as well as functional end products.
Applications in Industry
Material Jetting finds its application across various sectors.
- Aerospace: Utilizing high precision and lightweight materials for complex components.
- Medical: Producing custom prosthetics and dental aids, where detail is crucial.
- Consumer Goods: Creating prototypes and final products, especially in the field of consumer electronics and cabinetry.
This technology is favored in situations where fine details and high surface quality are prioritized, supporting fast iterations and development processes.
Key Advantages and Disadvantages
It is important to weigh the benefits and drawbacks of Material Jetting.
Advantages:
- High-resolution parts with intricate details.
- Capability to use multiple materials in one print.
- Excellent surface finish, reducing the need for post-processing.
Disadvantages:
- Typically higher material costs compared to FDM or other methods.
- Limited build size due to the constraints of the machinery.
- Sensitivity to light, which may affect storage and handling.
"Material Jetting stands out for its ability to produce high-quality, detailed parts suitable for advanced manufacturing needs."
In summary, Material Jetting is a robust 3D printing technology that excels in precision and versatility, making it vital to modern manufacturing applications. Its unique process and material options enable innovative design solutions, especially for those who demand both form and functionality in their projects.
Electron Beam Melting (EBM)
Electron Beam Melting (EBM) is a distinct 3D printing method that stands out due to its unique approach and capabilities. This technology utilizes an electron beam as its primary energy source, enabling it to achieve high-quality metal parts. EBM is particularly significant in industries that require precise and durable components, such as aerospace and medical sectors. Its ability to process metal powder into complex geometries makes it highly relevant in today’s manufacturing landscape. Understanding the nuances of this technology is crucial for professionals aiming to leverage its benefits for advanced applications.
Mechanism and Process
The process of Electron Beam Melting is quite intricate. It begins with a powdered metal material spread across a build platform. An electron beam then selectively melts the powder layer by layer according to the digital model provided. As the electron beam moves, it can quickly and accurately fuse the powdered particles. This layer-by-layer approach not only facilitates complex geometries but also allows for material efficiency. After each layer is processed, the platform moves down, and a fresh layer of powder is applied. This cycle continues until the part is fully constructed. The overall speed of EBM can be enhanced by its ability to fuse large areas at once.
Material Characteristics
EBM is primarily associated with metal materials, particularly those that are difficult to weld or shape using traditional methods. Common materials include titanium alloys, cobalt chrome, and nickel alloys. These materials possess specific properties such as high strength-to-weight ratios, oxidation resistance, and biocompatibility, making them ideal for demanding applications.
The powders used in EBM must conform to stringent specifications to ensure consistent melting and solidification processes, resulting in the required mechanical properties. The particle size and morphology play a significant role in determining the overall quality of the finished part.
Applications in Aerospace and Medical Fields
The applications of EBM span several critical industries, notably aerospace and medicine.
Aerospace applications often involve the creation of lightweight yet strong components, such as turbine blades, support structures, and complex brackets, where weight savings yield substantial fuel efficiency benefits.
In the medical field, EBM offers immense potential for producing custom implants and prosthetics. The technology allows for tailored designs that match patient-specific anatomical requirements. For example, titanium implants designed for orthopedic applications are often created through EBM due to the material's compatibility with human tissue and bones.
Benefits and Limitations
EBM presents several key benefits, including:
- High precision and detail: EBM excels at creating complex geometries.
- Material Efficiency: Minimal waste due to the additive nature of the process.
- Mechanical Properties: Parts often display enhanced properties compared to conventionally manufactured items due to rapid cooling and solidification.
However, there are also limitations to consider:
- Higher Cost: EBM machines and the required materials can be expensive.
- Longer Build Times: Compared to some other methods, the process can be slower due to the careful melting of materials.
- Surface Finish: Parts may require post-processing to achieve desired surface qualities.
"EBM is not just a manufacturing process; it is a game-changer in the way we produce complex metal components."
Finale
In the rapidly evolving field of 3D printing, a comprehensive understanding of the diverse printer types is essential for anyone looking to navigate this technology. The conclusion serves as a vital synthesis of the knowledge accrued throughout the article, reinforcing the significance of different 3D printing methods like FDM, SLA, SLS, and others. Each technology has its unique mechanisms and applications, which influence the ultimate outcome, whether in a prototyping environment or for production.
Summary of Key Points
- Diverse Technologies: There are various types of 3D printers, each serving specific purposes depending on the desired material and end-use. Technologies like Fused Deposition Modeling (FDM) are prevalent for beginners and hobbyists, while more specialized methods like Stereolithography (SLA) and Selective Laser Sintering (SLS) cater to professional requirements.
- Applications: The applications covered extend across different fields, including engineering, medicine, and consumer products. Each printing technology offers unique advantages, making them suitable for specific tasks and industries.
- Advantages and Limitations: Each printer type presents its strengths and weaknesses. For instance, while FDM printers are cost-effective, they may lack the precision offered by SLA printers. Understanding these nuances helps readers make informed decisions based on their specific needs.
- Current Trends and Future Directions: Awareness of evolving trends adds context to decisions regarding 3D printing technology. Innovations continue to emerge, potentially expanding applications and refining existing processes.
Future Outlook of 3D Printing Technologies
Looking ahead, the future of 3D printing continues to be promising. As materials improve and technology advances, there are several considerations:
- Innovative Materials: Research into new materials, including bioprinting and composites, is likely to grow. This opens avenues for wider applications in fields like healthcare and sustainable manufacturing.
- Automation and AI Integration: The integration of artificial intelligence and machine learning into 3D printing processes is becoming more common. Such advancements could automate the printing process, allowing for more efficient production cycles.
- Regulatory Considerations: As the technology advances, legal and safety regulations will have to evolve. This may impact how 3D printing technologies are adopted, especially in sensitive sectors like aerospace and healthcare.
- Customization Trends: Tailored solutions are gaining traction. As customers increasingly seek personalized products, 3D printing’s capacity for customization places it at the forefront of manufacturing.
"3D printing not only revolutionizes efficiency but also emphasizes the importance of adaptability in design and production processes."
The insights gathered in this guide culminate in a holistic view of 3D printing technologies. Awareness of these elements, along with considerations for future trends, equips enthusiasts and professionals alike to effectively harness the potential of 3D printing.