In-Depth Analysis of Resin Printer Test Prints: A Detailed Exploration
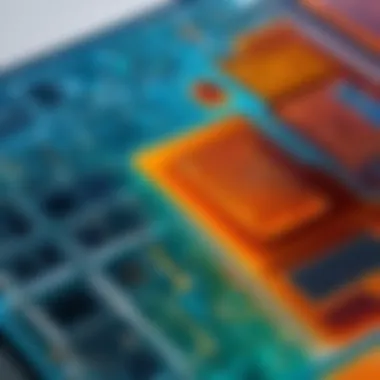
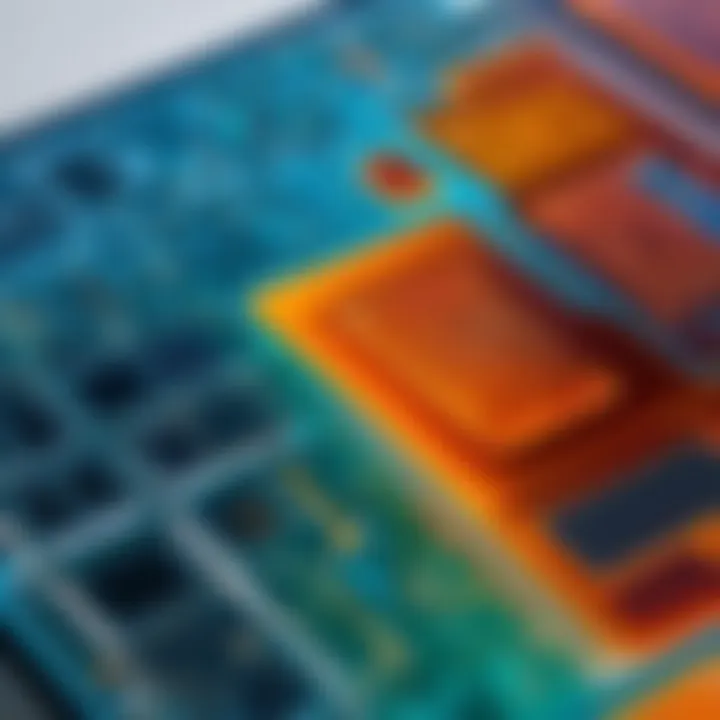
Product Overview
When delving into the realm of resin printer test prints, it is crucial to grasp the essence of the product being analyzed. In this context, understanding the underlying brand stands as a fundamental starting point. By comprehensively examining the brand information associated with the resin printer under scrutiny, consumers can gain a clearer insight into the ethos guiding the product's development. Moreover, elucidating the key specifications of the resin printer sheds light on its technical capabilities and performance benchmarks. Shaping the reader's expectations by delving into the pricing structure further refines the narrative landscape.
Performance Comparison
As we venture deeper into the analysis of resin printer test prints, a vital facet to explore revolves around benchmark tests that ascertain the print quality, accuracy, and overall performance of the printer. Conducting detailed speed and efficiency comparisons unveils how the resin printer fares against its counterparts in the market landscape. Such meticulous evaluations serve as valuable touchpoints for discerning individuals seeking optimal printing solutions.
Features and Technology
The narrative takes an intriguing turn as we delve into the distinctive features and technological innovations embedded within the resin printer. Unpacking these unique attributes not only showcases the printer's prowess but also delineates its niche within the broader spectrum of printing technology. Exploring the compatibility of the printer with other devices illuminates potential synergies and integrations that could enhance workflow efficiency for users seeking seamless connectivity.
Pros and Cons
In the pursuit of a comprehensive understanding of resin printer test prints, it is paramount to dissect the strengths and weaknesses inherent in the product. Identifying the strengths underscores the competitive advantages and standout features that make the resin printer a compelling choice for consumers. Simultaneously, delineating the areas earmarked for improvement offers a candid appraisal of the printer's limitations, guiding potential buyers towards informed decisions.
Value for Money
Unveiling the cost-effectiveness and long-term benefits associated with the resin printer bridges the gap between investment and returns. By juxtaposing the pricing of the printer with its value proposition, readers can gauge the feasibility of their purchase decisions. Furthermore, a comparative analysis with similar products underscores the unique value proposition offered by the resin printer, enriching the reader's deliberative process.
Introduction to Resin Printer Test Prints
Resin printer test prints are a fundamental aspect of resin printing technology. These test prints play a crucial role in ensuring the quality and accuracy of resin-printed objects. By examining various elements such as layer height, overhang capabilities, and bridging performance, test prints provide valuable insights into the performance of a resin printer. Understanding the significance of test prints is essential for resin printing enthusiasts and professionals seeking to achieve optimal results in their printing projects.
Importance of Test Prints
Ensuring Print Quality
Ensuring print quality is a paramount objective in resin printing. Test prints focused on print quality help in assessing the surface finish, level of detail, and overall fidelity of printed objects. For this article, emphasizing the importance of ensuring print quality sheds light on the meticulous approach required in resin printing to achieve high-resolution, flawless prints. The consistency and precision achieved through ensuring print quality are qualities highly sought after by resin printing enthusiasts.
Calibrating Printer Settings
Calibrating printer settings is a critical aspect of resin printing that greatly influences print outcomes. Proper calibration ensures that the printer operates optimally, resulting in accurate prints with minimal errors. In this article, highlighting the significance of calibrating printer settings underscores the meticulous process involved in preparing a resin printer for successful print production. Understanding the intricacies of calibrating printer settings is key to mastering the art of resin printing.
Identifying Issues Early
Identifying issues early in the printing process is essential for troubleshooting and optimizing print results. Test prints designed to uncover potential issues allow printers to address and rectify problems before committing to full-scale prints. In this article, discussing the importance of identifying issues early emphasizes the proactive approach necessary for achieving consistent print quality. Early issue detection can save time, materials, and frustration, making it a valuable practice in resin printing.
Types of Test Prints
Layer Height Tests
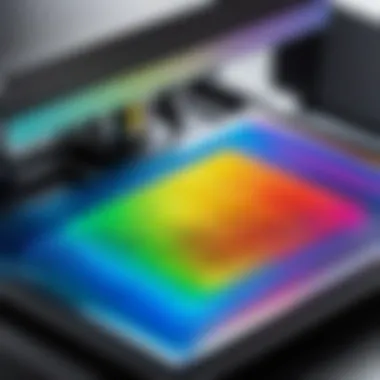
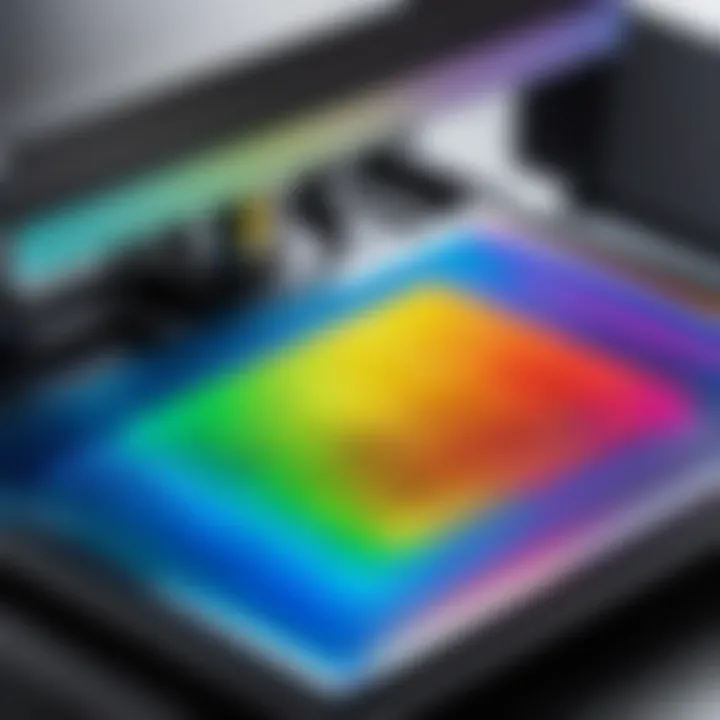
Layer height tests focus on evaluating the resolution capabilities of a resin printer by varying the thickness of each printed layer. Understanding the impact of layer height on print quality is crucial for achieving desired levels of detail and precision in resin prints. In this article, delving into layer height tests elucidates the intricate relationship between layer thickness and print fidelity, providing valuable insights for resin printing enthusiasts seeking optimal results.
Overhang Tests
Overhang tests assess a printer's ability to create horizontal features without the need for support structures. By testing the printer's overhang capabilities, users can evaluate its bridging performance and positional accuracy. Emphasizing overhang tests in this article underscores the importance of understanding a printer's limitations and capabilities when producing complex designs. Mastering overhang tests is essential for achieving successful prints with intricate geometries.
Bridging Tests
Bridging tests focus on the printer's ability to create horizontal structures spanning gaps in the print. These tests evaluate the printer's bridging capabilities and the structural integrity of the printed object. Discussing bridging tests in this article highlights the importance of assessing a printer's bridging performance to ensure the stability and functionality of printed designs. Mastery of bridging tests is essential for resin printing projects requiring robust and reliable structural elements.
Tools for Test Printing
Resin Calibration Tools
Resin calibration tools aid in fine-tuning resin properties to achieve optimal print results. These tools enable users to adjust resin settings such as exposure times, curing rates, and material properties for different print scenarios. Highlighting the importance of resin calibration tools in this article accentuates the precision and customization available to resin printers for enhancing print quality. Incorporating resin calibration tools into test prints is key to achieving consistent and high-quality resin prints.
Support Removal Tools
Support removal tools facilitate the removal of support structures from resin prints without causing damage to the printed object. These tools come in various forms, including snips, tweezers, and spatulas, designed to effectively and efficiently eliminate supports. Exploring support removal tools in this article emphasizes the crucial role these tools play in post-processing resin prints. Utilizing support removal tools correctly ensures clean and undamaged final prints, enhancing the overall aesthetics and functionality of resin-printed objects.
Post-Processing Equipment
Post-processing equipment includes curing stations, polishing tools, and cleaning solutions essential for refining resin prints post-printing. These tools aid in enhancing surface finish, ensuring dimensional accuracy, and improving the overall visual appeal of printed objects. Discussing post-processing equipment in this article underscores the comprehensive approach required in resin printing, from printing to finishing. Incorporating post-processing equipment into test prints is imperative for achieving professional-quality resin-printed products.
Testing Techniques for Resin Prints
In this section, we delve into the critical aspect of testing techniques for resin prints within the context of this comprehensive analysis. Understanding and implementing effective testing methodologies is paramount in ensuring the quality and accuracy of resin prints. By focusing on specific elements such as visual inspection, functional testing, and post-processing evaluation, we can identify potential issues, refine printing parameters, and enhance the overall print quality.
Visual Inspection
Surface Quality Examination
Surface quality examination plays a pivotal role in the assessment of resin prints. It involves scrutinizing the smoothness, finish, and overall quality of the printed surface. By carefully inspecting surface details, including layer lines, imperfections, and defects, manufacturers can gauge the print's overall aesthetic appeal and functional integrity. This method allows for the identification of any anomalies that may affect the part's performance or appearance, enabling timely adjustments and improvements. While surface quality examination is a labor-intensive process, its benefits in detecting flaws early on justify its prominent inclusion in this article.
Dimensional Accuracy Assessment
Dimensional accuracy assessment is a crucial aspect of resin print testing, focusing on verifying the dimensional precision of the printed part. By comparing the printed dimensions to the intended design specifications, manufacturers can assess the printer's accuracy and calibration. This assessment ensures that the final prints meet the desired size and geometry requirements, indicating the printer's reliability and consistency. Despite the inherently meticulous nature of dimensional accuracy assessment, its significance in guaranteeing print accuracy justifies its inclusion in this analysis.
Detail Verification
Detail verification involves examining the intricate features and fine details of resin prints to validate the part's fidelity to the original design. By scrutinizing intricate elements such as small text, embossed details, or complex geometries, manufacturers can ascertain the printer's capability to reproduce intricate designs accurately. This meticulous process aids in identifying potential issues related to resolution, layer adhesion, and fine feature reproduction, facilitating adjustments to optimize print quality. While detail verification demands meticulous attention to minute details, its role in ensuring high-precision prints makes it a valuable component of this analytical framework.
Functional Testing
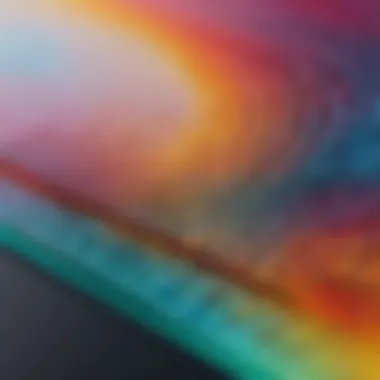
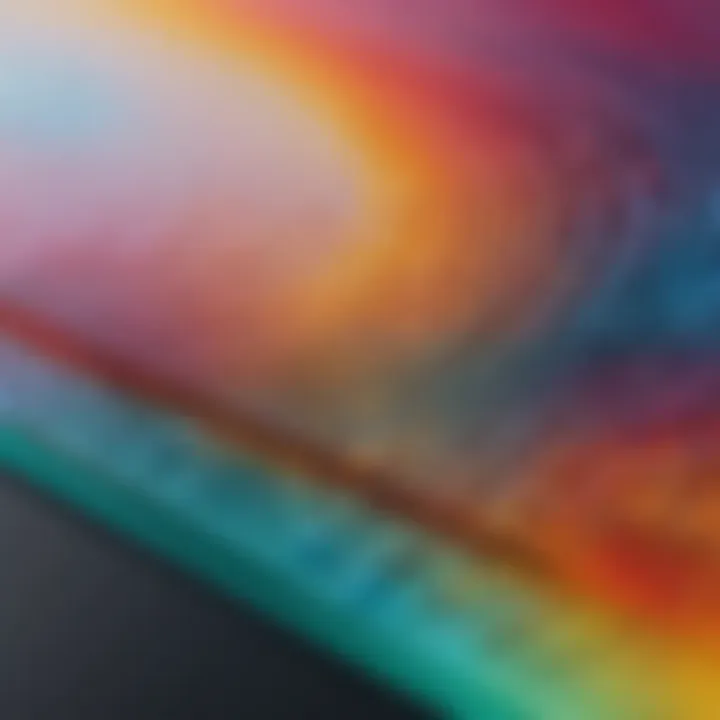
Mechanical Stress Tests
Mechanical stress tests are essential in evaluating the structural integrity and mechanical properties of resin prints under various stress conditions. By subjecting the prints to bending, torsion, or compression tests, manufacturers can assess the part's strength, resilience, and deformation characteristics. This type of testing is instrumental in determining the print's load-bearing capacity, impact resistance, and overall mechanical performance. Despite the complexities involved in conducting mechanical stress tests, their role in validating print durability and performance justifies their inclusion in this comprehensive analysis.
Fit and Assembly Checks
Fit and assembly checks focus on evaluating the dimensional accuracy and compatibility of printed parts within an assembly or mating component. By ensuring that the printed parts fit together seamlessly and align with design tolerances, manufacturers can verify the part's functionality and interconnectivity. Fit and assembly checks are crucial in detecting any discrepancies in part dimensions or geometric inconsistencies that may hinder assembly or functionality. Despite the meticulous nature of fit and assembly checks, their importance in verifying part compatibility and assembly precision necessitates their detailed examination within this article.
Moving Parts Evaluation
Moving parts evaluation involves testing the functionality and movement of mechanisms or assemblies within resin prints. By assessing the range of motion, friction levels, and operational smoothness of moving parts, manufacturers can validate the print's mechanical functionality and dynamic performance. This type of evaluation is essential for identifying any constraints, interferences, or failures in moving components, ensuring optimal functionality and operational efficiency. Although moving parts evaluation requires precise testing setups and observation techniques, its critical role in validating print functionality justifies its inclusion in this comprehensive analysis.
Post-Processing Evaluation
Support Removal Analysis
Support removal analysis focuses on evaluating the effectiveness and efficiency of support structure removal processes in resin prints. By meticulously inspecting the residual marks, surface imperfections, and structural integrity post-support removal, manufacturers can assess the quality of support removal techniques. This analysis allows for the identification of any damage, warping, or irregularities caused during support removal, informing adjustments to optimize post-processing workflows. Despite the detailed nature of support removal analysis, its indispensable contribution to enhancing print aesthetics and functionality warrants its comprehensive discussion within this article.
Surface Finishing Assessment
Surface finishing assessment involves scrutinizing the final surface qualities of resin prints post-processing, including finish texture, glossiness, and overall aesthetics. By assessing the smoothness, uniformity, and visual appeal of the printed surface, manufacturers can gauge the effectiveness of surface finishing techniques. This assessment helps identify any post-processing imperfections, discrepancies, or blemishes that may affect the print's final appearance and tactile qualities, enabling refinements to achieve desired surface finishes. Despite the meticulous scrutiny required in surface finishing assessment, its pivotal role in enhancing print aesthetics and quality necessitates its detailed exploration within this comprehensive analysis.
Curing and Final Inspection
Curing and final inspection entail verifying the completion of the curing process and conducting a final examination of resin prints before deployment or usage. By inspecting the cured parts for structural integrity, consistency, and curing completeness, manufacturers can ensure that the prints have attained optimal material properties. This final assessment helps detect any uncured resin, surface tackiness, or incomplete cures that may compromise the print's performance or longevity, guiding final finishing steps or reprints if necessary. Despite the meticulous nature of curing and final inspection, their critical role in certifying print readiness and quality justifies their holistic examination within this article.
Advanced Testing Methods and Protocols
When delving deeper into the realm of resin printing, understanding advanced testing methods and protocols becomes crucial. These methodologies play a pivotal role in ensuring the quality, accuracy, and performance of resin prints. By focusing on specific elements such as benchmarking, comparison, tolerance, and tensile testing, resin printing enthusiasts and professionals can fine-tune their processes and elevate the overall printing experience. Advanced testing methods provide invaluable insights into the intricacies of resin printing, allowing for precise adjustments and optimizations to achieve optimal results.
Benchmarking and Comparison
Print Speed Trials
Print speed trials are integral to the resin printing process, offering valuable data on the speed at which prints can be completed without compromising quality. By conducting thorough print speed trials, users can determine the optimal balance between efficiency and detail accuracy. This aspect of testing allows for the identification of printing speeds that maximize productivity while maintaining the desired print quality. Print speed trials are a popular choice for resin printing applications due to their ability to enhance workflow efficiency and streamline the printing process.
Accuracy Benchmarking
Accuracy benchmarking focuses on evaluating the precision and fidelity of resin prints in comparison to their digital models. This testing method enables users to assess the overall accuracy of their printing setup and make adjustments as needed. By scrutinizing the accuracy of printed dimensions and features, benchmarking ensures that resin prints meet the exacting standards required for various applications. Accuracy benchmarking is a beneficial tool for optimizing print settings and enhancing the consistency of print results.
Material Performance Evaluation
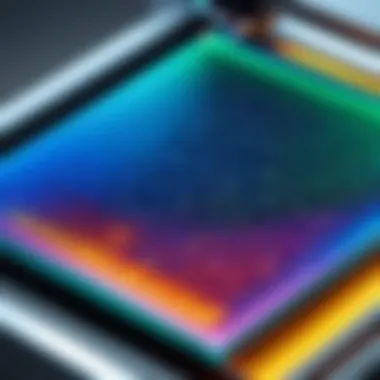
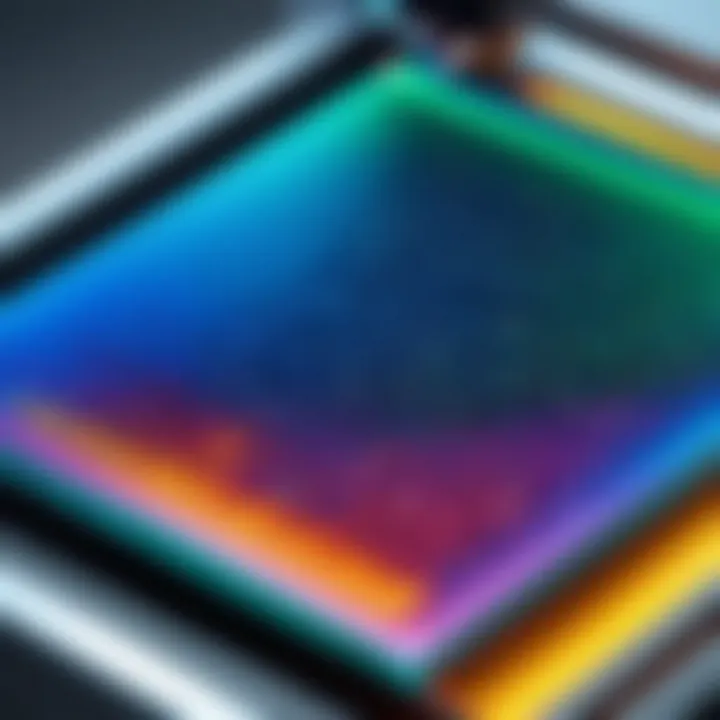
Material performance evaluation entails testing the mechanical properties and durability of resin prints under different conditions. By analyzing factors such as tensile strength, flexibility, and resistance to wear, users can determine the suitability of a resin material for specific applications. This testing method provides valuable insights into the performance characteristics of resin prints and aids in selecting the most appropriate materials for diverse printing needs. Material performance evaluation serves as a cornerstone for ensuring the quality and functionality of resin prints.
Tolerance and Tensile Testing
Dimensional Tolerance Checks
Dimensional tolerance checks focus on verifying the accuracy of printed dimensions against the intended design specifications. This testing process ensures that resin prints maintain dimensional integrity and adhere to precise measurements. By conducting dimensional tolerance checks, users can identify and address any deviations or inaccuracies in the printing process, ultimately enhancing print quality and consistency. Dimensional tolerance checks are essential for ensuring that resin prints meet stringent tolerance requirements for various applications.
Strength and Flexibility Analysis
Strength and flexibility analysis involves evaluating the structural integrity and flexibility of resin prints to gauge their suitability for functional purposes. This testing method assesses the ability of printed parts to withstand mechanical stress and deformation, providing valuable data on material strength and resilience. By conducting thorough strength and flexibility analysis, users can optimize print settings and material selection to ensure optimal performance in diverse applications. This testing process is instrumental in enhancing the functionality and durability of resin prints.
Material Durability Testing
Material durability testing focuses on assessing the long-term performance and wear resistance of resin prints. By subjecting printed parts to simulated real-world conditions and wear testing, users can evaluate the robustness and longevity of the printed objects. This testing method helps in identifying potential weak points or areas of improvement in the printing process, leading to enhanced durability and reliability of resin prints. Material durability testing is essential for ensuring that printed parts can withstand prolonged use and environmental factors, making it a critical aspect of resin printing evaluation.
Real-World Applications and Stress Testing
Prototyping Applications
Prototyping applications involve using resin prints for creating functional prototypes and test models across various industries. By leveraging the speed and accuracy of resin printing, prototyping applications enable rapid iteration and validation of design concepts. This aspect of resin printing is highly beneficial for product development, allowing designers and engineers to quickly visualize and test their ideas before full-scale production. Prototyping applications are a popular choice for resin printing due to their ability to accelerate the design process and reduce time-to-market.
Functional Parts Testing
Functional parts testing focuses on evaluating the performance and fit of resin-printed components in functional assemblies. This testing method involves verifying the functionality and compatibility of printed parts within the intended application, ensuring proper fit and operation. By conducting comprehensive functional parts testing, users can validate the structural integrity and performance of printed components, identifying any issues or optimizations required. Functional parts testing is essential for verifying the reliability and functionality of resin prints in real-world scenarios, making it a crucial step in the printing process.
Longevity and Wear Testing
Longevity and wear testing aim to assess the durability and resistance of resin prints to prolonged use and environmental factors. By subjecting printed parts to rigorous stress tests and wear simulations, users can evaluate the longevity and performance of the printed objects over time. This testing method helps in identifying potential failure points or weaknesses in the printed components, enabling users to enhance the durability and reliability of resin prints. Longevity and wear testing are essential for ensuring that printed parts can withstand the rigors of real-world applications and maintain their quality and functionality throughout their lifespan.
Conclusion: Enhancing Resin Printing Through Test Prints
In this final segment of our expansive exploration into resin printer test prints, we delve deeper into the pivotal role of enhancing resin printing through meticulous test prints. Optimizing print quality through iterative processes is crucial in the realm of resin printing. By meticulously calibrating settings and parameters, manufacturers can achieve unparalleled precision and output consistency. This emphasis on print quality not only elevates the final product but also streamlines production processes, enabling cost-effective and sustainable printing practices. The continuous improvement in print quality is a cornerstone of resin printing technology, underscoring the significance of refining printing methodologies for optimal results.
Continuous Improvement in Print Quality: Optimizing Settings and Parameters
When it comes to optimizing settings and parameters in resin printing, attention to detail is paramount. Fine-tuning parameters such as exposure times, layer heights, and resin types can yield significant improvements in print quality. By customizing these settings according to specific print requirements, manufacturers can achieve greater control over the printing process, leading to enhanced precision and reproducibility. The key characteristic of optimizing settings and parameters lies in its ability to fine-tune the printing process for optimal results, ensuring that each print meets the desired specifications with utmost accuracy.
Continuous Improvement in Print Quality: Incorporating Feedback and Iteration
Incorporating feedback and iteration into resin printing practices is essential for refining print quality and overall performance. By gathering feedback from test prints, manufacturers can identify areas for improvement and implement iterative changes to enhance print outcomes. This cyclical process of receiving feedback, implementing adjustments, and reevaluating results fosters an environment of continuous improvement, driving innovation and excellence in resin printing. The unique feature of incorporating feedback and iteration lies in its capacity to adapt to evolving production needs, facilitating agility and responsiveness in the face of changing printing requirements.
Continuous Improvement in Print Quality: Pushing Boundaries of Resin Printing
Pushing the boundaries of resin printing involves exploring novel techniques, materials, and capabilities to unlock new possibilities in additive manufacturing. By pushing the limits of conventional printing methodologies, manufacturers can pioneer advancements in resin printing that revolutionize product development and manufacturing processes. The key characteristic of pushing boundaries lies in its innovative approach to challenging established norms and embracing unconventional solutions to achieve breakthroughs in resin printing technology. While this pursuit of innovation may present its challenges, the rewards of expanding the horizons of resin printing are boundless, offering unparalleled opportunities for creativity and advancement.
Future Trends and Innovations
Looking ahead, the future of resin printing is poised for remarkable advancements driven by cutting-edge technologies and innovative practices. As resin formulations continue to evolve, manufacturers can expect enhanced material properties, print quality, and mechanical performance. Advances in resin formulations are paving the way for a new era of possibilities in additive manufacturing, where resilience, durability, and versatility are redefined. The integration of automation in testing processes signifies a shift towards more efficient and streamlined resin printing workflows. By automating repetitive tasks and standardizing testing protocols, manufacturers can optimize production efficiencies and ensure consistent print quality across various printing jobs. The introduction of artificial intelligence (AI) and machine learning in resin printing heralds a new chapter of intelligent manufacturing, where predictive analytics and data-driven insights empower manufacturers to make informed decisions and drive continuous improvement in resin printing technology. The fusion of AI and machine learning into resin printing processes not only enhances operational efficiencies but also augments precision, accuracy, and overall print quality. As these cutting-edge technologies become more integrated into resin printing ecosystems, the industry is poised for a transformative shift towards smarter, more adaptive manufacturing solutions.