Understanding Intel Fabrication Processes and Trends
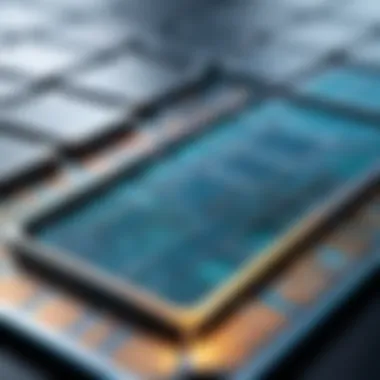
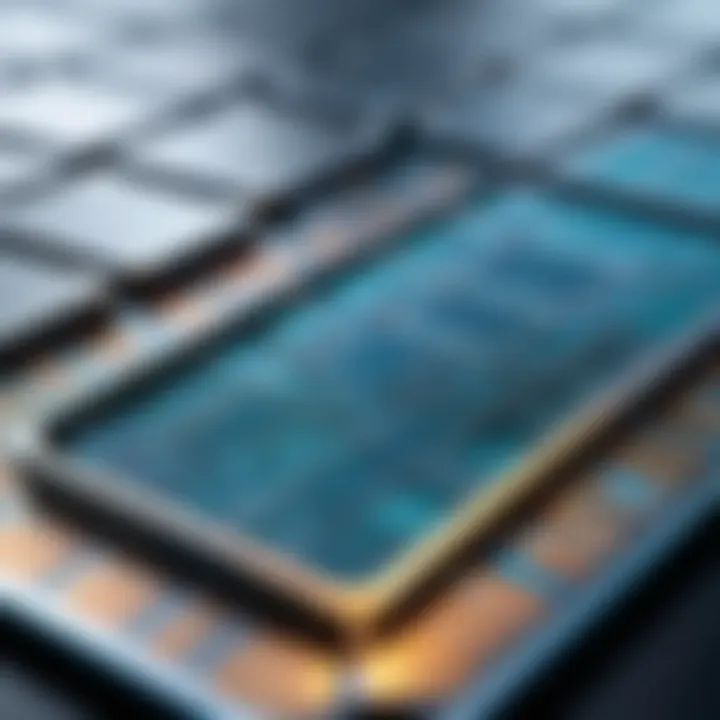
Intro
The semiconductor industry, often referred to as the backbone of modern technology, relies heavily on intricate fabrication processes to create the microprocessors that power everything from powerful gaming PCs to handheld devices. Intel, as a longstanding leader in this field, illustrates the dance between pioneering technology, operational efficiency, and market demands. In todayās fast-paced arena, understanding how Intel executes its fabrication processes offers invaluable insight into the broader dynamics influencing technology advancement. The tale here reflects Intel's formidable journey into the heart of semiconductor innovation.
From the earliest silicon wafers to todayās sophisticated fabrication facilities, Intel's methods have evolved remarkably. Itās not merely about cranking out chips; itās about a meticulous orchestration of design, material selection, and precision engineering. How has Intel managed to adapt and innovate in such a rapidly changing landscape? This article will explore crucial aspects of Intelās fabrication processes, shedding light on methodologies, future prospects, and industry challenges.
As we embark on this exploration, we will delve into key elements that shape fabrication, providing a comprehensive guide for those keen to understand this vital sector. Following sections will dive deeply into relevant product specifications, groundbreaking features, performance comparisons, as well as advantages and limitations associated with Intel's offerings in the semiconductor space.
Through this examination, it becomes clear that the intricacies of Intel's fabrication processes are not just technical details but a reflection of strategic prowess that underscores the companyās prominence in the tech world.
Prolusion to Intel Fabrication
In the realm of technology, understanding Intel fabrication is like holding the keys to a vast kingdom of microprocessors and semiconductors. This area is fundamental for anyone who cares about the performance of their devices, from gaming rigs to enterprise servers. Fabrication doesn't merely refer to the physical creation of chips; it encompasses a tapestry of processes that turn raw materials into the silicon we rely on every day. The intricacies of this process affect not just how fast a computer can calculate but also its energy usage, size, and overall capability. In this section, weāll delve into why this topic is vital, honing in on specific elements that impact the semiconductor landscape.
Understanding Semiconductor Fabrication
Semiconductor fabrication lays the groundwork for nearly everything in modern electronics. But what does that really entail? At its core, semiconductor fabrication is the process of creating complex devices from silicon. These steps range from polishing wafers to intricate doping processes that modify electrical properties. In essence, itās where the magic happens.
Fabrication processes play an unequivocal role in determining the characteristics and quality of semiconductor devices. Imagine if your smartphone could only operate at half its potential because of poor fabrication. That's how crucial these processes are.
A key benefit of knowing the ins and outs of these methods is understanding how they relate to performance optimization. For instance, mastering photolithography can lead to more precise and dense circuit patterns, akin to resizing a poster for clearer images, leading to improved efficiency and faster processing power.
Moreover, considerations about fabrication extend into the realm of technological innovation. With the ongoing competition in the semiconductor sector, companies like Intel are continually searching for methods to improve their processes. This seeks to avoid being left in the dust by competitors who may adopt new technologies faster.
Understanding fabrication isn't just for engineers; it's essential for anyone invested in technology's future. An informed consumer or industry professional can advocate for better products, pushing companies towards transparency in their manufacturing processes.
Lastly, mastering the concept of fabrication opens doors to appreciating future innovations. Intel is venturing into groundbreaking areas like quantum computing, and the state of its fabrication capabilities will play a pivotal role in these advancements.
In this article, we will move beyond the jargon, peeling back the layers of Intel's fabrication techniques and revealing the nuances that govern the industry. Whether you're a tech enthusiast, gamer, or an IT professional, there's something here that resonates with each of us, connecting our digital lives back to the intricate processes at Intel's fabrication facilities.
Historical Overview of Intelās Fabrication Techniques
The development of Intel's fabrication techniques stands as a crucial pillar in understanding not just their innovation but also the entire semiconductor industry. The historical journey of these techniques blends engineering advancements with strategic decisions, shaping the very threads of technology that power modern computation.
Intelās story began in the 1960s with the introduction of integrated circuits, a significant breakthrough that reduced the size and cost of computing power. This was a time when the technical community was transitioning from bulky, expensive hardware to more compact designs. The move to more sophisticated microfabrication processes laid the groundwork for Intelās future dominance, allowing them to space out transistors on chips like never before. With each iteration, they wielded their tools to develop smaller, more efficient structures, transforming microelectronics.
The Evolution of Microfabrication
The term microfabrication doesnāt just describe a process; it encompasses a revolutionary shift within the tech industry. Initially, Intel's fabrication techniques revolved around simple photolithography, but over the decades, there has been a substantial leap to more advanced methods. Here are some notable milestones that shaped Intelās landscape:
- 1971: Introduction of the 4004
The first microprocessor, the Intel 4004, was fabricated using a basic form of photolithography. This was the genesis of putting multiple functionality into a single chip, a hallmark of later techniques. - 1980s: The Rise of CMOS Technology
The implementation of Complementary Metal-Oxide-Semiconductor (CMOS) technology allowed for even greater complexity on a silicon wafer. It decreased power consumption, which was a game changer for portable devices. - 1990s: Deep Submicron Technologies
The push into deep submicron dimensions ushered in chips with minimal feature sizes. Intel's fabrication became a race to shrink transistor sizes further, leading to the introduction of the 90nm technology node that would become standard fare, allowing billions of transistors on a single die. - 2000s: FinFET and Beyond
By developing FinFET (Fin Field-Effect Transistor) technology, Intel responded to the heat and leakage challenges posed by small transistors. This three-dimensional structure effectively allowed for higher performance without the traditional power inefficiencies.
The evolution of these techniques was not merely a technical endeavor; it was a competitive necessity. Intel's constant innovation solidified its position at the forefront of the semiconductor industry, influencing countless applications from computing to telecommunications.
"Innovation is the ability to see change as an opportunity - not a threat."
ā Anonymous
As we parse through the timeline, it's evident that Intel's fabrication journey is marked by resilience and ingenuity. Their commitment to research and development helped to navigate through the industry's ever-changing landscape.
So, the historical narrative of Intel's fabrication techniques not only speaks volumes about their technological prowess but also shapes our understanding of future tech capabilities. Yet, as the tale of innovation continues, challenges loom on the horizon, pushing the boundaries of what can be achieved in semiconductor technology.
Core Fabrication Process
The core fabrication process is pivotal in the semiconductor industry. At Intel, this process involves various stages that transform raw materials into finely engineered microprocessors. The complexity of these steps directly impacts the performance, efficiency, and cost of the end products. Investing in optimizing each stage helps to ensure that Intel remains at the forefront of technology. Understanding this intricate process not only elucidates the workings behind Intel's successful chips but also highlights the various benefits and considerations necessary for maintaining high production standards.
Wafer Preparation
Before the actual fabrication can begin, wafer preparation must be on point. This stage starts with a thin slice of pure silicon, the essential ingredient in semiconductor devices. The silicon wafer needs to be polished to achieve a flawless surface, as any defects can lead to issues down the line. This meticulous approach sets the stage for layer deposition and is critical for ensuring minimal errors during later phases.
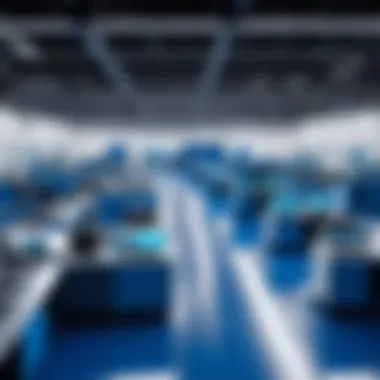
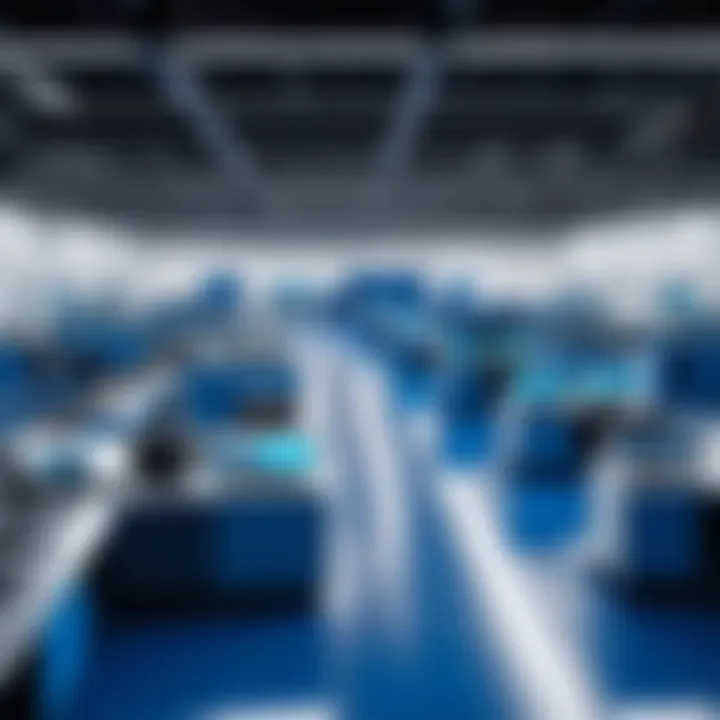
Additionally, precise cutting of the silicon during preparation allows for maximizing material usage, ultimately reducing waste. This process reflects a balance between quality and sustainability, both crucial for modern fabrication.
Photolithography Technologies
Photolithography stands as one of the most vital processes in semiconductor fabrication. It's akin to a detailed stencil work that defines how patterns of circuits are etched onto the silicon wafer. By projecting light through a mask onto a photosensitive layer, it allows specific areas to be coated and later developed.
Recent developments in extreme ultraviolet (EUV) lithography have pushed the boundaries, enabling smaller features on chips. This advancement is absolutely essential in the race for faster processing speeds and energy efficiency in chips. However, despite the cutting-edge technology, challenges remain with respect to equipment costs and the precision required for high yields.
Etching Processes
Once the photolithography patterns are in place, the etching process begins. This stage is crucial for removing unwanted material and creating the intricate electrical pathways on the silicon wafer. Different methods, including wet and dry etching, are employed based on the material and required precision.
Etching needs to be carried out with great care, as any misstep can compromise the intricate designs laid out during photolithography. Each etching process must be tailored to produce the desired results in terms of feature dimensions and profile shapes while maintaining the integrity of the underlying material. The demand for precision in this phase has led to innovative methods in etching technologies, showcasing the evolution in fabrication efficiencies.
Doping and Implantation Techniques
Doping is another fundamental step that enhances the electrical properties of silicon wafers. By introducing external elements into the silicon, the conductivity can be adjusted to meet specific needs. This implantation technique, often utilizing ion beams, allows for precise control over how much of an impurity is added and where it is placed. The right combination of dopants effectively transforms the wafer into n-type or p-type materials, which are the building blocks of transistors.
As semiconductor devices become more complex, the demand for achieving lower thresholds of dopant concentration increases. This presents new challenges for manufacturers such as Intel, requiring ongoing refinement of doping techniques to ensure that devices meet evolving performance standards.
Interconnect Formation
The last leg of the core fabrication process focuses on interconnect formation. This is where layers of metal are deposited to connect various components on the wafer. Copper and aluminum are often used, owing to their excellent conductive properties. The formation of these interconnections is crucial for the functionality of integrated circuits, allowing signals to pass between different areas efficiently.
However, as device dimensions shrink, the resistance of these interconnects can become problematic. Techniques like dual-damascene processing are being explored to tackle these challenges, allowing for adjustments that not only enhance conductivity but also contribute to the overall reliability of the devices.
The efficiency of these processes directly affects the performance and cost of semiconductor products, underscoring their importance in Intel's operations.
In summarizing the core fabrication process, we see a series of interlinked steps, each critical for the successful production of semiconductor devices. Understanding these intricacies equips us with valuable insights into Intel's capabilities and the overall semiconductor landscape.
Technological Innovations in Fabrication
The semiconductor industry stands on the shoulders of innovation, particularly in the sphere of fabrication. This not only pivots the future of microprocessors but also plays a significant role in the overarching landscape of technology. Intel, being a formidable player in this domain, continues to push the envelope with its ground-breaking strategies.
One of the central tenets of technological innovation is its intermittent evolution, often driven by advancements in efficiency, performance, and cost. These innovations often seek to meet the insatiable demand for smaller, faster, and more efficient chips. Notably, semiconductor fabrication encompasses a slew of processes from the foundational material science to complex machinery design. Here, it's vital to understand specific elements that have defined modern fabrication technologies, including advancements in process nodes, 3D packaging techniques, and the increasing integration of artificial intelligence.
"Innovation distinguishes between a leader and a follower." ā Steve Jobs
Advancements in Process Nodes
In semiconductor fabrication, a process node refers to the manufacturing technology used to create integrated circuits. A smaller node typically means more transistors in the same area, leading to improved performance and reduced power consumption. Intelās move from 14nm to 10nm and the more recent advancements toward 7nm and 5nm nodes illustrates this progression. The complexity involved increases with smaller nodes. Factors such as heat release and electron mobility become critical, necessitating cutting-edge materials and precision machinery. Moreover, the challenges encountered during this transition compel fabricators to innovate constantly, driving research into new materials like high-k dielectrics and FinFETs. These innovations are not merely steps toward technical superiority; they represent Intel's commitment to staying ahead in a competitive market.
3D Packaging Techniques
3D packaging is another striking innovation that plays a vital role in modern microfabrication. Traditional methods often relied on a two-dimensional approach, limiting density and performance. With 3D packaging, multiple chip layers are stacked and interconnected, significantly improving performance without enlarging the chip's footprint. Techniques like Through-Silicon Vias (TSVs) allow for vertical connections between layers, reducing the need for lengthy interconnects that can introduce delays.
The shift to 3D architecture aligns well with the industry's goal of creating high-performance computing solutions that do not compromise on energy efficiency. This innovation is also perceived as a way to optimize space and reduce overall manufacturing costs while packing more processing power into a smaller area.
Integration of AI in Fabrication
The integration of artificial intelligence into fabrication processes is fairly transformative. AI technologies streamline various stages, from design to manufacturing, enabling real-time data analysis and decision-making. For instance, AI algorithms can predict manufacturing defects or optimize the supply chain dynamically. This helps mitigate inefficiencies and enhances yield rates.
Furthermore, employing machine learning in design phases can lead to more innovative chip layouts that traditional design methods might overlook. By automating mundane tasks, engineers can focus on creative problem-solving, leading to breakthrough designs that better serve consumer needs.
This technological triadāprocess node advancements, 3D packaging techniques, and AI integrationānot only propels Intel into a league of its own but also notably reshapes the future of semiconductor fabrication. Each innovation layer contributes to a collective leap towards more advanced computing capabilities that cater to modern demands.
Global Impact of Intelās Fabrication Facilities
Intel's fabrication plants wield significant influence not only within the semiconductor industry but also in global economic landscapes. These facilities, often referred to as fabs, are massive production sites that harness cutting-edge technology to churn out microchips pivotal for myriad applicationsāfrom consumer electronics to cloud computing and artificial intelligence. Understanding the impact of these plants elucidates the role Intel plays in shaping technological advancements and labor markets on a global scale.
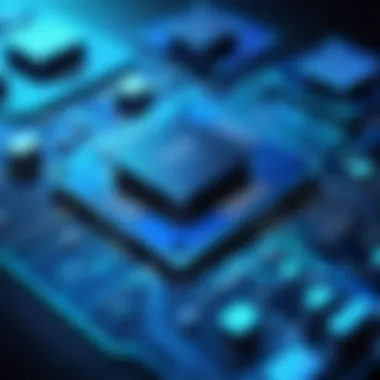
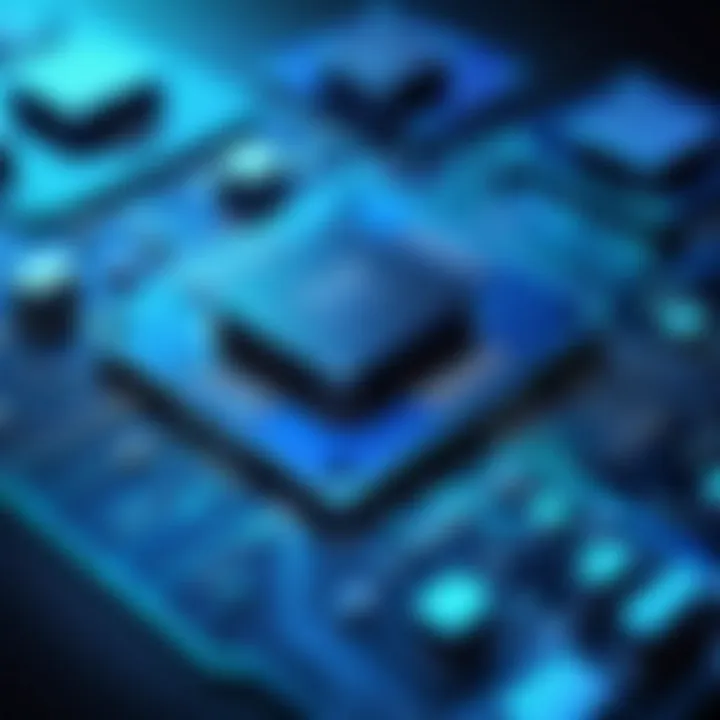
Major Fabrication Plants
Intel operates several major fabrication facilities worldwide, each tailored for specific production capabilities and scales. For instance:
- D1X Facility (Hillsboro, Oregon): This facility is known for its research innovations and is crucial for developing new fabrication technologies. It acts as a testbed for advanced manufacturing processes even before they are deployed in mass production.
- Fab 68 (Shenzhen, China): This plant not only caters to the growing demands of the Asian markets but also represents Intel's commitment to international expansion. The fab specializes in producing chips tailored for mobile devices.
- Fab 42 (Chandler, Arizona): This facility, among the largest, is designed for high-volume manufacturing of process nodes, which allows Intel to stay competitive in productivity.
These fabrication plants employ thousands of highly skilled workers and have established strong supply chains with local suppliers, contributing to economic growth in their respective regions. The plants are strategically located to leverage local talent pools and technological ecosystems, which is crucial for enhancing innovation.
Sustainability in Production
As the world grapples with environmental challenges, Intel's fabrication facilities are increasingly focusing on sustainable practices. The production of semiconductors is energy-intensive and generates a significant carbon footprint. However, Intel is taking strides to mitigate this impact.
- Energy Efficiency: Many fabs have implemented advanced energy management systems. They are designed to optimize energy consumption and use renewable sources such as solar and wind power. For instance, Intel's Fab 42 has put in place energy-efficient cooling systems that considerably reduce electricity usage.
- Water Conservation: Water is a critical resource in semiconductor fabrication. Intel aims to minimize water usage by recycling and treating wastewater to be reused in their processes. The company's facilities have reported up to a 30% reduction in water use due to these initiatives.
- Waste Reduction: The adoption of lean manufacturing techniques has helped Intel lessen waste output. Scrap material from fabrication processes is systematically recycled, resulting in a closed-loop system that not only reduces waste but also cuts costs.
"Intel's commitment to sustainability in semiconductor fabrication is not just a corporate responsibility; itās a strategic necessity for maintaining relevance in an eco-conscious market."
Challenges in Modern Fabrication
In today's fast-paced technological landscape, the challenges faced in modern fabrication are multifaceted and significant. Intel, as a trailblazer in semiconductor manufacturing, has to navigate a labyrinth of difficulties that influence production timelines, cost efficiency, and product performance. These challenges are not merely barriers but rather essential considerations that shape the company's strategy and future outlook.
Supply Chain Disruptions
Supply chain disruptions have become the new norm rather than the exception, especially in the context of global events that impact logistics and transportation. For Intel, these disruptions can stall production lines and lead to shortages of essential materials like silicon wafers and specialized chemicals needed in the fabrication process.
- The Covid-19 pandemic, as an example, showcased how interconnected global supply chains can falter. A temporary factory closure in one part of the world sends ripples throughout the entire manufacturing ecosystem.
- A delay in the delivery of photolithography machines can halt an entire production cycle, affecting the availability of microprocessors in the market almost instantly.
These challenges compel Intel to rethink its supply chain strategies, leading to greater emphasis on local sourcing and stockpiling critical components. In some cases, companies have had to pivot to alternative suppliers, which sometimes compromises quality or increases costs. To illustrate, roughly a year ago, Intel announced partnerships with newer suppliers to lessen their dependence on single-source vendors.
Cost Management in Production
Cost management in fabrication is not just about trimming the fat; it's about making astute investments in technology and innovation to maintain competitive edge. As the demand for high-performance computing continues to soar, the pressure on Intel to deliver cutting-edge microchips at a reasonable cost intensifies.
- Research and Development: Significant funds must still be allocated towards R&D. Intel needs to innovate continuously; neglect can lead to missed opportunities and lost market share to competitors like AMD and TSMC.
- Precision Manufacturing: The rise in the intricacy of chip designs means that slight variations can incur catastrophic costs. Defective wafers must be discarded, raising the per-unit cost significantly.
- Labor Costs: Skilled workers command higher wages as the semiconductor industry becomes more competitive. Intel has to balance fair compensation with keeping overall costs down, which is no small feat.
"In a world driven by technology, how effectively a company manages its production costs can ultimately dictate its survival in a fiercely competitive environment."
Intel's ongoing efforts to streamline these operational challenges involve rigorous analysis and strategic foresight that integrates innovative methodologies, even examining automation technologies that promise not only cost savings but improved consistency in output. This delicate dance of managing supply chain complexities and production costs outlines the current landscape of semiconductor manufacturingāone that demands both resilience and adaptability.
Comparative Analysis of Competitors
Understanding the competitive landscape in semiconductor fabrication is crucial to grasping how Intel positions itself as a leader in this ever-evolving field. The rivalry primarily exists between major players like AMD and TSMC, each offering unique methodologies, production capabilities, and technological advancements. By examining these competitors, we can uncover what sets Intel apart and what it needs to do to remain at the forefront.
AMD and TSMC: A Benchmark Study
When Intelās performance is scrutinized, AMD and TSMC emerge as key benchmarks. AMD, operating as a direct competitor in microprocessors, leverages TSMC for its own manufacturing, establishing a rather interesting relationship that highlights the intricacies of outsourcing in semiconductor manufacturing. This partnership has allowed AMD to focus on design while TSMC handles fabrication, leading to products like the Ryzen and EPYC series that have gained significant traction in the market.
To understand AMD and TSMC's advantage, consider their exceptional adaptation to the 7nm process node. TSMC has refined its fabrication techniques to achieve remarkable efficiency and lower power consumption, placing AMD in a strong position against Intel's traditional manufacturing. Moreover, the synergy between AMD's innovative designs and TSMC's advanced fabrication technologies showcases how the duo continuously raises the bar for performance.
Highlights of this competitive analysis include:
- Process Technology: AMDās ability to harness TSMCās advanced nodes allows them to push boundaries in terms of performance and energy efficiency.
- Market Positioning: AMDās strategy of aggressive pricing for high-performance products attracts consumers away from Intel.
- Future Strategies: Both companies are carving out paths forward that may heavily impact Intelās standing, with TSMC venturing into even smaller fabrication nodes.
Intel, on the other hand, has deeply invested in its manufacturing capabilities and development of its advanced process nodes, aiming for a shift back in the competition.
Market Share Trends
In the world of semiconductor fabrication, market share trends offer vital insights into the health and direction of the industry. Intel has traditionally held a significant piece of the pie, but market dynamics are slowly shifting. As of 2023, AMD and TSMC have seen an upward trajectory in their respective shares, indicating a changing tide in consumer preference.
- AMDās Share: With the rise of their Ryzen processor, AMDās market share in desktop CPUs has surged, now standing at roughly 30%, challenging Intel's long-held dominance.
- TSMC's Role: Holding around 50% of the global foundry market, TSMC serves as a backbone for many tech companies, creating a robust business model centered on continuous innovation.
- Future Projections: Analysts predict that by 2025, if trends persist, we may observe significant shifts, with AMD possibly overtaking Intel in key segments if the latter does not accelerate its technological advancements.
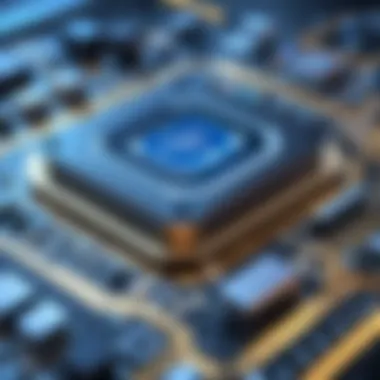
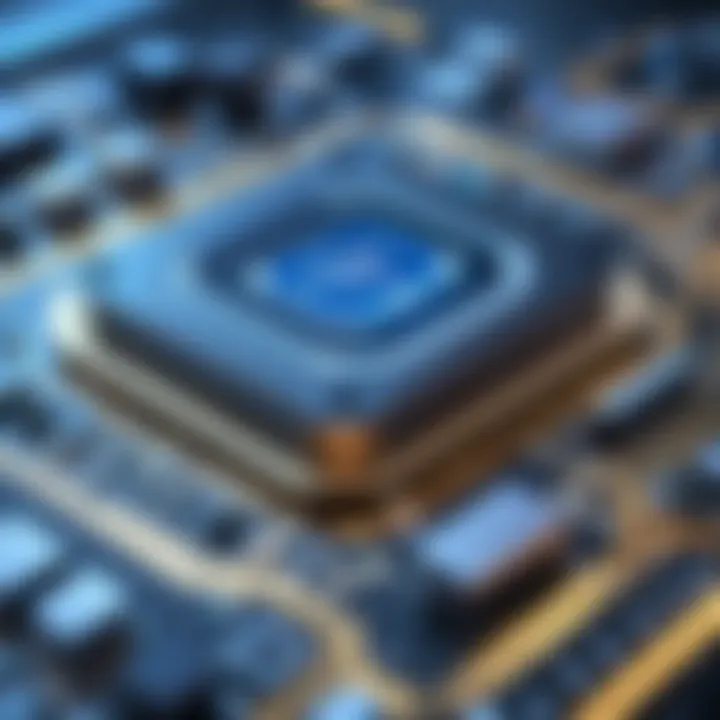
This comparative landscape between Intel, AMD, and TSMC showcases the pressures exerted on Intel and highlights the importance of innovation and adaptability. With an increasing need to monitor and respond to competitors, Intel must strategize effectively to navigate the challenges presented by these formidable rivals.
The Role of Research and Development in Fabrication
Research and Development (R&D) stands as a crucial pillar in the realm of semiconductor fabrication. In a world where technology evolves at breakneck speed, sustaining a competitive edge relies heavily on how much effort companies like Intel invest in discovering and fine-tuning new methodologies for chip production. R&D not only fuels innovation but also plays a pivotal role in addressing performance demands from consumers who expect quicker, more efficient, and ultimately more powerful devices. As we explain below, two key areas within R&D bear significant impact on Intel's futureāthe investment in future technologies and collaborations with academic institutions.
Investment in Future Technologies
Investment in future technologies isn't just a catchphrase; it's foundational. For Intel to remain at the forefront of the semiconductor industry, it needs to pour resources into research that may seem speculative today but promises substantial returns tomorrow.
Take quantum computing, for instance. Although we might not be running quantum-powered applications just yet, the groundwork laid today could lead to substantial breakthroughs in the coming years. The money spent on understanding quantum bits (qubits) and their operations can one day revolutionize our computing experience.
- Increased Efficiency: Updating existing fabrication processes with new technologies often leads to cost-saving efficiencies. Investments that focus on better material usage, waste reduction, and energy efficiencies stand to yield significant benefits.
- Product Development Timelines: A robust R&D sector can drastically shorten the time from concept to consumer, enabling quicker testing and deployment of new products. This speed can maintain or even improve market share in a crowded landscape.
- Futuristic Products: Regular investments in cutting-edge innovations pave the way for products that were once on the drawing board. Look no further than the introduction of integrated AI in semiconductors, which optimizes how chips manage resources and perform computations in real time.
Collaborations with Academic Institutions
Working closely with academic institutions enhances the R&D landscape, providing companies like Intel access to fresh ideas and emerging talent. Universities host clusters of innovative thinkers who often bring unorthodox perspectives on traditional challenges. The partnership is symbioticāwhile academia gains access to real-world testing grounds for theories, companies can leverage the latest research discoveries without bearing all costs.
- Interdisciplinary Approaches: The best advancements often come from blending disciplines. Intel can tap into fields like materials science and metallurgy, guided by top-tier researchers working at universities.
- Talent Acquisition: The collaboration also serves a dual purpose of fostering strong relationships with potential future employees. Students engaged in cutting-edge research at their universities often become key hires upon graduation, bringing fresh viewpoints and skills into the company.
- Funding Research & Development: Many partnerships see Intel funding specific academic projects that align with its business objectives. Often, these collaborations yield patents that serve both entitiesāwhere Intel might commercialize a finding, and the university can enhance its reputation as an innovator in the field.
Thus, it becomes evident that R&D is more than just a line item in Intel's budget; it is a definitive strategy providing a beacon through the fog of technological complexity, guiding the path toward future success.
Future Directions in Intel Fabrication
The landscape of semiconductor fabrication is evolving at an astonishing pace. For Intel, being at the forefront of innovation is not merely important; it is essential for maintaining its competitive edge and ensuring sustainability in an industry that sees rapid advancements. The future directions in Intel fabrication encompass several emerging technologies and methodologies that may redefine the benchmarks of performance, efficiency, and adaptability. This section highlights key facets of this evolution, focusing particularly on the push for quantum computing and the continuous miniaturization of process nodes.
The Push for Quantum Computing
Quantum computing represents a monumental leap from classical computing, leveraging the principles of quantum mechanics to process information in ways previously thought impossible. Intel recognizes how crucial this technology is for future developments in computing power. The fabrication techniques need to adapt to accommodate quantum bits, or qubits, as they manipulate data using quantum states.
Technical innovations for quantum processing units have been surfacing, including
- Superconducting qubits: These are among the most researched and reliable forms of qubits, allowing for the faster computation required for practical quantum processes.
- Silicon qubits: Intel has invested in developing silicon-based qubits, aiming to tap into existing semiconductor manufacturing processes. This promotes scalability and integration with current technologies.
Intel's focus on quantum computing is not just about future potential; it's a strategic response to emerging areas such as cryptography, drug discovery, and complex systems modeling, all of which stand to benefit significantly from quantum capabilities.
5nm and Beyond: Expectations and Predictions
As we cast our eyes on the next generation of semiconductor technology, the movement towards 5 nanometer process technology, and beyond, reflects not just a trend but a necessity. Smaller nodes mean more transistors can fit on a chip, leading to enhanced performance and energy efficiency.
Key considerations for Intel in this realm include:
- Manufacturing Challenges: As nodes shrink, the complexity in fabricating these chips increases, requiring sophisticated techniques in design and manufacturing.
- Compatibility: Ensuring that new materials and processes are compatible with existing architectures is crucial. Without this, the transition to smaller nodes could lead to significant integration issues.
- Performance Metrics: The main goal is to maintain or even exceed the performance gains achieved with previous nodes. Leveraging technologies like extreme ultraviolet lithography (EUV) becomes pivotal.
Intel also looks to leverage advances in materials science, focusing on semiconductor materials beyond traditional silicon to enhance performance and efficiency at such small scales.
"As the physical limits of silicon technology approach, our goal is to highlight how Intelās future depends on continuous innovation and exploration of cutting-edge techniques."
In summary, the future directions in Intel fabrication are marked by innovative strategies for harnessing quantum computing while striving to maintain leadership in smaller process technologies. The adaptability of Intelās fabrication processes will determine its success in navigating the multifaceted challenges of a fast-evolving technological landscape.
Epilogue
In summarizing the complex panorama of Intel's fabrication processes, itās crucial to recognize the synergy of innovation, efficiency, and adaptability that characterizes the company's approach. This article has navigated through various critical facets of semiconductor manufacturing, shedding light on the multifarious techniques and methodologies that Intel employs. The insights presented here underscore not just the technical capabilities, but also the strategic thinking behind Intel's operations, which are essential for maintaining its competitive advantage in a fast-paced technology landscape.
Summarizing Key Insights
To encapsulate the article's crux:
- Significance of Fabrication: Intel's fabrication is a cornerstone of its success, enabling the production of high-performance microprocessors critical in everything from consumer electronics to advanced computers for gamers and IT professionals.
- Technological Evolution: Over the years, Intel has made leaps in microfabrication techniques, which have not only improved the performance of their products but also reduced costs and increased production scalability.
- Global Influence: With fabrication plants strategically located worldwide, Intelās operations not only contribute to local economies but also influence global supply chains and market dynamics.
- Challenges and Adaptations: The challenges Intel faces, whether from supply chain disruptions or the necessity for cost management, highlight the pressing need for continued innovation and strategic foresight.
- Future Prospects: As Intel looks to the horizon, the potential shift towards quantum computing and advancements in smaller process nodes signal an upward trajectory in technology that promises enhanced capabilities and new possibilities.
Understanding these points unveils the intricate design and execution behind Intel's fabrication strategies, providing rich context for enthusiasts, professionals, and anyone with a vested interest in the semiconductor industry. In essence, Intel's commitment to research and development, along with collaborations and cutting-edge innovations, reinforces its position as a leading force in shaping the future of fabrication.
"In the world of technology, the only constant is change."
This observation resonates deeply with the narrative we've explored, emphasizing that Intel's journey in fabrication is as much about resolving current challenges as it is about anticipating and innovating for the future.